Spread betting
Page 42
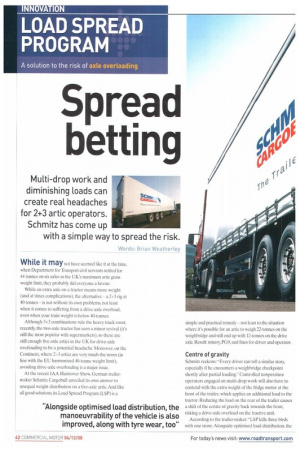
Page 43
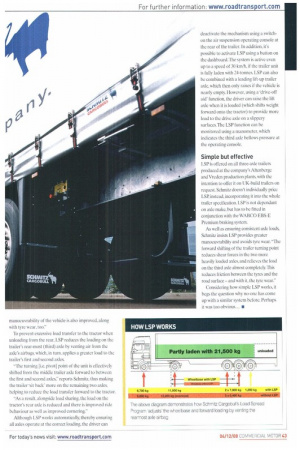
If you've noticed an error in this article please click here to report it so we can fix it.
Multi-drop work and diminishing loads can create real headaches for 2+3 artic operators. Schmitz has come up with a simple way to spread the risk.
Words: Brian Weatherley While it may not have seemed like it at the time, when Department for Transport civil servants settled for 44 tonnes on six axles as the UK's maximum artic gross weight limit, they probably did everyone a favour.
While an extra axle on a tractor means more weight (and at times complications), the alternative a 2+3 rig at 40 tonnes is not without its own problems, not least when it comes to suffering from a drive-axle overload, even when your train weight is below 40-tonnes.
Although 3+3 combinations rule the heavy truck roost, recently, the two-axle tractor has seen a minor revival (it's still the most popular with supermarkets), so there are still enough five-axle artics in the UK for drive-axle overloading to be a potential headache. Moreover, on the Continent, where 2+3 artics are very much the norm (in line with the EU harmonised 40-tonne weight limit), avoiding drive-axle overloading is a major issue.
At the recent IAA Hannover Show, German trailermaker Schmitz Cargobull unveiled its own answer to unequal weight distribution on a five-axle artic. And like all good solutions, its Load Spread Program (LSP) is a simple and practical remedy not least to the situation where it's possible for an artic to weigh 22-tonnes on the weighbridge and still end up with 12-tonnes on the drive axle. Result: misery,PG9, and fines for driver and operator.
Centre of gravity
Schmitz reckons: "Every driver can tell a similar story, especially if he encounters a weighbridge checkpoint shortly after partial loading." Controlled temperature operators engaged on multi-drop work will also have to contend with the extra weight of the fridge motor at the front of the trailer, which applies an additional load to the tractor. Reducing the load on the rear of the trailer causes a shift of the centre of gravity back towards the front, risking a drive-axle overload on the tractive unit.
According to the trailer-maker: "LSP kills three birds with one stone. Alongside optimised load distribution, the manoeuvrability of the vehicle is also improved, along with tyre wear, too.
To prevent excessive load transfer to the tractor when unloading from the rear. LSP reduces the loading on the trailer's rear-most (third) axle by venting air from the axle's airbags, which, in turn, applies a greater load to the trailer's first and second axles.
-The turning [i.e. pivot l point of the unit is effectively shifted from the middle trailer axle forward to between the first and second axles," reports Schmitz, thus making the trailer 'sit hack' more on the remaining two axles. helping to reduce the load transfer forward to the tractor.
"As a result, alongside load sharing, the load on the tractor's rear axle is reduced and there is improved ride behaviour as well as improved cornering."
Although LSP works automatically, thereby ensuring all axles operate at the correct loading, the driver can deactivate the mechanism using a switchon the air suspension operating console at the rear of the trailer. In addition, it's possible to activate LSP using a button on the dashboard, The system is active even up to a speed of 30 km/h, if the trailer unit is fully laden with 24-tonnes. LSP can also be combined with a leading lift-up trailer axle, which then only raises if the vehicle is nearly empty. However, using a 'drive-off aid' function, the driver can raise the lift axle when it is loaded (which shifts weight forward onto the tractor) to provide more load to the drive axle on a slippery surfaces.'The LSP function can be monitored using a manometer, which indicates the third axle bellows pressure at the operating console.
Simple but effective
LSP is offered on all three-axle trailers produced at the company's Altenberge and Vreden production plants, with the intention to offer it on UK-build trailers on request. Schmitz doesn't individually price LSP, instead, incorporating it into the whole trailer specification. LSP is not dependant on axle make, but has to be fitted in conjunction with the WABCO EBS-E Premium braking system.
As well as ensuring consistent axle loads. Schmitz insists LSP provides greater manoeuvrability and avoids tyre wear. "The forward shifting of the trailer turning point reduces shear forces in the two more heavily loaded axles, and relieves the load on the third axle almost completely. This reduces friction between the tyres and the road surface and with it, the tyre wear."
Considering how simple LSP works, it begs the question why no-one has come up with a similar system before. Perhaps it was too obvious... •