Hydraulic valve tappets
Page 34
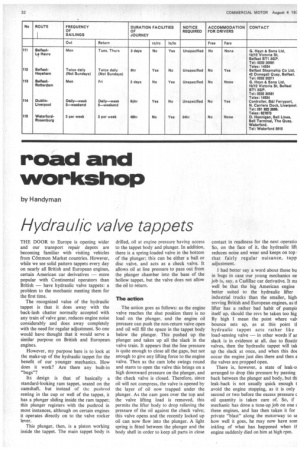
If you've noticed an error in this article please click here to report it so we can fix it.
THE DOOR to Europe is opening wider and our transport repair depots are becoming familiar with visiting vehicles from Common Market countries. However, while we see solid pattern tappets every day on nearly all British and European engines, certain American car derivatives — more popular with Continental operators than British — have hydraulic valve tappets: a problem to the mechanic meeting them for the first time.
The •recognized value of the hydraulic tappet is that it does away with the back-lash chatter normally accepted with any train of valve gear, reduces engine noise considerably and does away completely with the need for regular adjustment. So one would have thought that it would serve a similar purpose on British and European. engines.
However, my purpose here is to look at the make-up of the hydraulic tappet for the benefit of our younger mechanics. How does it work? Are there any built-in "bugs"?
Its design is that of basically a standard-looking ram tappet, seated on the camshaft, but instead of the pushrod resting in the cup or well of the tappet, it has a plunger sliding inside the ram tappet; this plunger registers with the pushrod in most instances, although on certain engines it operates directly on to the valve rocker lever.
This plunger, then, is a piston working inside the tappet. The main tappet body is drilled, oil at engine pressure having access to the tappet body and plunger. In addition, there is a spring-loaded valve in the bottom of the plunger; this can be either a ball or disc valve, and acts as a check valve. It allows oil at line pressure to pass out from the plunger chamber into the base of the hollow tappet, but the valve does not allow the oil to return.
The action
The action goes as follows: as the engine valve reaches the shut position there is no load on the plunger, and the engine oil pressure can push the non-return valve open and oil will fill the space in the tappet body below the plunger. This pushed up the plunger and takes up all the slack in the valve train. It appears that the line pressure is quite enough to close all the gaps, but not enough to give any lifting force to the engine valve. Then as the cam lobe swings round and starts to open the valve this brings on a high downward pressure on the plunger, and the check valve is closed. Therefore, since oil will not compress, the valve is opened by the layer of oil now trapped under the plunger. As the cam goes over the top and the valve lifting load is removed, this permits the lifter body to drop relieving the pressure of the oil against the check valve; this valve opens and the recently locked up oil can now flow into the plunger. A light spring is fitted between the plunger and the body shell in order to keep all parts in close contact in readiness for the next operatio So, on the face of it, the hydraulic lift reduces noise and wear and keeps on top , that fairly regular nuisance, tapp adjustment.
I had better say a word about those bu in bugs in case our young mechanics ne job is, say, a Cadillac car derivative. It ME well be that the big American engine better suited to the hydraulic lifter industrial trucks than the smaller, high, revving British and European engines, as ti lifter has a rather bad habit of pumpir itself up, should the revs be taken too hig By high I mean the point where vali bounce sets up, as at this point ti hydraulic tappet acts rather like load-sensing valve — in other words if ar slack is in evidence at all, due to floatir valves, then the -hydraulic tappet will tak up the slack at once, and when this doc occur the engine just dies there and then a the valves are propped open.
There is, however, a state of leak-o: arranged to drop this pressure by passing back between the plunger and body, but thi leak-back is not usually quick enough t avoid the engine stopping, as it is only second or two before the excess pressure c oil quantity is taken care of. So, if mechanic has done a tune-up job on one c these engines, and has then taken it for private "blast" along the motorway to se how well it goes, he may now have sorn inkling of what has happened when a engine suddenly died on him at high rpm.