Mixed fleet problems
Page 54
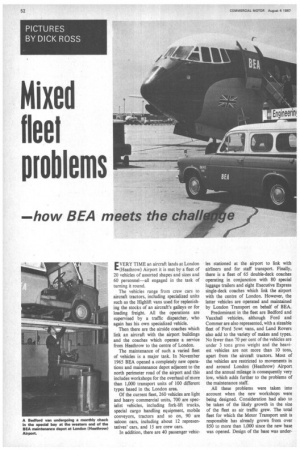
Page 55
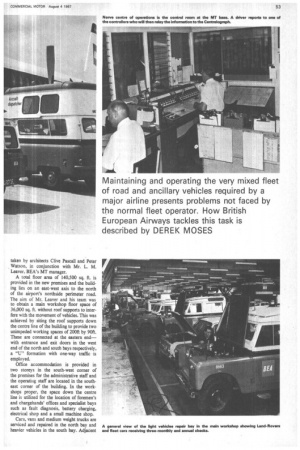
Page 56
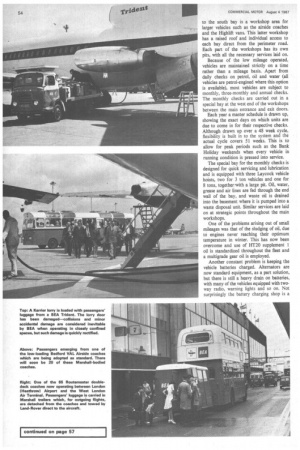
Page 59
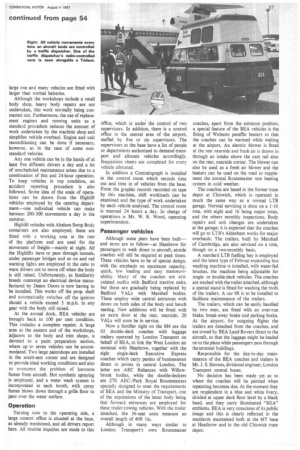
If you've noticed an error in this article please click here to report it so we can fix it.
how BEA meets the chall
C VERY TIME an aircraft lands at London (Heathrow) Airport it is met by a fleet of 20 vehicles of assorted shapes and sizes and 60 personnel all engaged in the task of turning it round.
The vehicles range from crew cars to aircraft tractors, including specialized units such as the Highlift vans used for replenishing the stocks of an aircraft's galleys or for loading freight. All the operations are supervised by a traffic dispatcher, who again has his own specialized vehicle.
Then there are the airside coaches which link an aircraft with the airport buildings and the coaches which operate a service from Heathrow to the centre of London.
The maintenance of such a varied fleet of vehicles is a major task. In November 1965 BEA opened a completely new operations and maintenance depot adjacent to the north perimeter road of the airport and this includes workshops for the overhaul of more than 1.000 transport units of 100 different types based in tilt; London area.
Of the current fleet, 260 vehicles are light and heavy commercial units, 700 are specialist vehicles, including fork-lift trucks, special cargo handling equipment, mobile conveyors, tractors and so on, 90 are saloon cars, including about 12 representatives' cars, and 15 are crew cars.
In addition, there are 40 passenger vehic
les stationed at the airport to link with airliners and for staff transport. Finally, there is a fleet of 65 double-deck coaches operating in conjunction with 80 special luggage trailers and eight Executive Express single-deck coaches which link the airport with the centre of London. However, the latter vehicles are operated and maintained by London Transport on behalf of BEA.
Predominant in the fleet are Bedford and Vauxhall vehicles, although Ford and Cornmer are also represented, with a sizeable fleet of Ford 5cwt vans, and Land Rovers also add to the variety of makes and types. No fewer than 70 per cent of the vehicles are under 3 tons gross weight and the heaviest vehicles are not more than 10 tons, apart from the aircraft tractors. Most of the vehicles are restricted to movements in and around London (Heathrow) Airport and the annual mileage is consequently very low, which adds further to the problems of the maintenance staff.
All these problems were taken into account when the new workshops were being designed. Consideration had also to be taken of the likely growth in the size of the fleet as air traffic grew. The total fleet for which the Motor Transport unit is responsible has already grown from over 850 to more than 1,000 since the new base was opened. Design of the base was under taken by architects Clive Pascall and Peter Watson, in conjunction with Mr. L. M. Leaver, BEA's MT manager.
A total floor area of 140,500 sq. ft. is provided in the new premises and the building lies on an east-west axis to the north of the airport's northside perimeter road. The aim of Mr. Leaver and his team was to obtain a main workshop floor space of 36,000 sq. ft. without roof supports to interfere with the movement of vehicles. This was achieved by siting the roof supports down the centre line of the building to provide two unimpeded working spaces of 200ft by 90ft. These are connected at the eastern end— with entrance and exit doors in the west end of the north and south bays respectively, a "U" formation with one-way traffic is employed.
Office accommodation is provided in two storeys in the south-west corner of the premises for the administrative staff and the operating staff are located in the southeast corner of the building. In the workshops proper, the space down the centre line is utilized for the location of foremen's and chargehands' offices and specialist bays such as fault diagnosis, battery charging, electrical shop and a small machine shop.
Cars, vans and medium weight trucks are serviced and repaired in the north bay and A general view of the fight vehicles repair bay in the main workshop showing Land-Rovers heavier vehicles in the south bay. Adjacent and fleet cars receiving three-monthly and I checks.
to the south bay is a workshop area for Larger vehicles such as the airside coaches and the Highlift vans. This latter workshop has a raised roof and individual access to each bay direct from the perimeter road. Each part of the workshops has its own pits, with all the necessary services laid on.
Because of the low mileage operated, vehicles are maintained strictly on a time rather than a mileage basis. Apart from daily checks on petrol, oil and water (all vehicles are petrol-engined where this option is available), most vehicles are subject to monthly, three-monthly and annual checks. The monthly checks are carried out in a special bay at the west end of the workshops between the main entrance and exit doors.
Each year a master schedule is drawn up, showing the exact days on which units are due to come in for their respective checks. Although drawn up over a 48 week cycle, flexibility is built in to the system and the actual cycle covers 51 weeks. This is to allow for peak periods such as the Bank Holiday weekends when every vehicle in running condition is pressed into service.
The special bay for the monthly checks is designed for quick servicing and lubrication and is equipped with three Laycock vehicle hoists, two for 3 ton vehicles and one for 8 tons, together with a large pit. Oil, water, grease and air lines are fed through the end wall of the bay, and waste oil is drained into the basement where it is pumped into a waste disposal unit. Similar services are laid on at strategic points throughout the main workshops.
One of the problems arising out of small mileages was that of the sludging of oil, due to engines never reaching their optimum temperature in winter. This has now been overcome and use of HT20 supplement 1 oil is standardized throughout the fleet and a multigrade gear oil is employed.
Another constant problem is keeping the vehicle batteries charged. Alternators are now standard equipment, as a part solution, but there is still a heavy drain on batteries, with many of the vehicles equipped with twoway radio, warning Lights and so on. Not surprisingly the battery charging shop is a large one and many vehicles are fitted with larger than normal batteries.
Although the workshops include a small body shop, heavy body repairs are not undertaken, this work normally being contracted out. Furthermore, the use of replacement engines and running units as a standard procedure reduces the amount of work undertaken by the machine shop and simplifies vehicle overhaul. Engine and unit reconditioning can be done if necessary, however, as in the case of some nonstandard vehicles.
Any one vehicle can be in the hands of at least five different drivers a day and a lot of unscheduled maintenance arises due to a combination of this and 24-hour operation. To keep vehicles in top condition, an accident reporting procedure is also followed. Some idea of the scale of operations can be drawn from the Highlift vehicles employed by the catering department—one individual vehicle can make between 200-300 movements a day in the summ er.
Highlift vehicles with Abelson Swop Body containers are also employed; these are fitted with a working area at the rear of the platform and are used for the movement of freight—mainly at night. All the Highlifts have to pass through tunnels, under passenger bridges and so on and red warning lights are employed in the cabs to warn drivers not to move off when the body is still raised. Unfortunately, as familiarity breeds contempt an electrical device manufactured by Deans Doors is now having to be installed. This works off the prop. shaft and automatically switches off the ignition should a vehicle exceed 5 m.p.h. in any gear with the body still raised.
At the annual dock, BEA vehicles are brought back to 100 per cent condition. This includes a complete repaint. A large area at the eastern end of the workshops, adjacent to the body and trim shops, is devoted to a paint preparation section, where up to seven vehicles can be accommodated. Two large paintshops are installed in the south-east corner and are designed to provide ideal working conditions and also to overcome the problem of kerosene fumes from aircraft. Hot synthetic spraying is employed, and a water wash system is incorporated in each booth, with spray fumes blown down through a grille floor to pass over the water surface.
Operation
Turning now to the operating side, a large control office is situated at the base, as already mentioned, and all drivers report here. All routine inquiries are made to this office, which is under the control of two supervisors. In addition, there is a control office in the central area of the airport, staffed by five or six supervisors. The supervisors at the base have a list of people or departments authorized to demand transport and allocate vehicles accordingly. Requisition sheets are completed for every vehicle allocated.
In addition a Centralograph is installed in the control room which records time out and time in of vehicles from the base. From the graphic records recorded on tape by this machine, shift workloads can be examined and the type of work undertaken by each vehicle analysed. The control room is manned 24 hours a day. In charge of operations is Mr. W. R. Wood, operating superintendent.
Passenger vehicles
Although some piers have been built— and more are to follow—at Heathrow for passengers to walk direct to aircraft, airside coaches will still be required at peak times. These vehicles have to be of special design, with the emphasis on maximum capacity, quick, low loading and easy manoeuvrability. Many of the coaches are articulated outfits with Bedford tractive units, but these are gradually being replaced by Bedford VALs with Marshall bodies. These employ wide central entrances with doors on both sides of the body and bench seating. New additions will be fitted with an extra door at the rear, nearside; 20 VALs will soon be in service.
Now a familiar sight on the M4 are the 65 double-deck coaches with luggage trailers operated by London Transport on behalf of BEA, to link the West London air terminal with Heathrow, together with the eight single-deck Executive Express coaches which carry parties of businessmen direct to points in central London. The latter are AEC Reliances with Willowbrook bodies, while the double-deckers are 27ft AEC /Park Royal Routemasters specially designed to meet the requirements of BEA and the Ministry of Transport, one of the stipulations of the latter body being that forward entrances are employed for these trailer-towing vehicles. With the trailer attached, the 56-seat units measure an overall length of 40ft lin.
Although in many ways similar to London Transport's own Routemaster coaches, apart from the entrance position, a special feature of the BEA vehicles is the fitting of Webasto paraffin heaters so that the coaches can be warmed while waiting at the airport. An electric blower is fitted at the rear nearside and fresh air is drawn in through an intake above the cant rail also on the rear, nearside corner. The blower can also be used as a fresh air blower and the heaters can be used on the road to supplement the normal Routemaster ram heating system in cold weather.
The coaches are based in the former tram depot at Chiswick, which is operated in much the same way as a normal LTB garage. Normal servicing is done on a 1-16 rota, with eight and 16 being major rotas, and the others monthly inspections. Body repairs and unit changes are undertaken at the garage; it is expected that the coaches will go to LTB's Aldenham works for major overhauls. The trailers, built by Marshall of Cambridge, are also serviced on a rota, though on a two-monthly basis.
A standard LTB fuelling bay is employed and the latest type of Februat expanding bus washing machine is installed, with water-fed brushes, the machine being adjustable for singleor double-deck vehicles, The coaches are washed with the trailer attached, although a special stand is fitted for washing the roofs of the trailers. A car lift is to be installed to facilitate maintenance of the trailers.
The trailers, which can be easily handled by two men, are fitted with an over-run brake, break-away brake and parking brake. At the airport, for outgoing flights the trailers are detached from the coaches, and are towed by BEA Land Rovers direct to the aircraft, so that the luggage might be loaded on to the plane while passengers pass through the terminal buildings.
Responsible for the day-to-day maintenance of the BEA coaches and trailers is Mr. J. S. Stevens, divisional engineer, London Transport central buses.
No decision has been made yet as to where the coaches will be painted when repainting becomes due. At the moment they are resplendent in a blue and white livery, divided at upper deck floor level by a black band, and they carry illuminated "BEA" emblems. BEA is very conscious of its public image and this is clearly reflected in the standards maintained both at the MT base at Heathrow and in the old Chiswick tram depot.