Dolt yourself axle weighing
Page 48
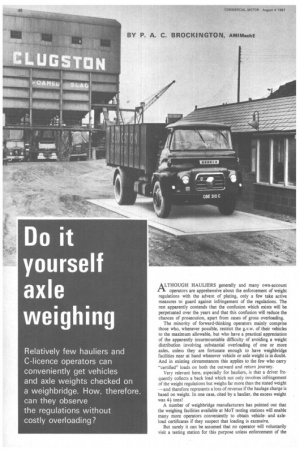
Page 49
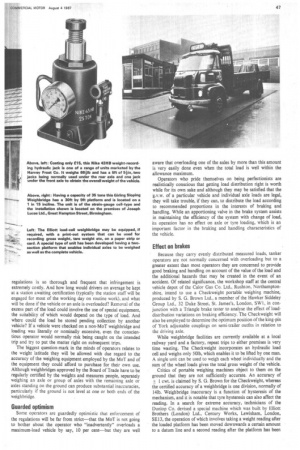
Page 50
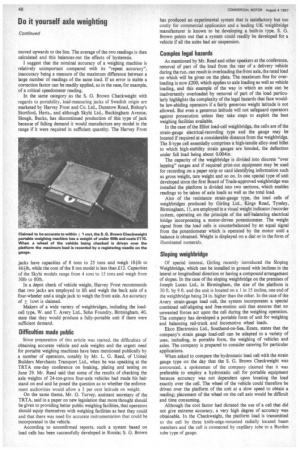
If you've noticed an error in this article please click here to report it so we can fix it.
ALTHOUGH HAULIERS generally and many own-account operators are apprehensive about the enforcement of weight regulations with the advent of plating, only a few take active measures to guard against infringement of the regulations. The rest apparently contends that the confusion which exists will be perpetuated over the years and that this confusion will reduce the chances of prosecution, apart from cases of gross overloading.
The minority of forward-thinking operators mainly comprise those who, whenever possible, restrict the g.v.w. of their vehicles to the maximum allowable, but who have a practical appreciation of the apparently insurmountable difficulty of avoiding a weight distribution involving substantial overloading of one or more axles, unless they are fortunate enough to have weighbridge facilities near at hand whenever vehicle or axle weight is in doubt. And in existing circumstances this applies to the few who carry "certified" loads on both the outward and return journey.
Very relevant here, especially for hauliers, is that a driver frequently collects a back load which not only involves infringement of the weight regulations but weighs far more than the stated weight —and therefore represents a loss of revenue if the haulage charge is based on weight. In one case, cited by a haulier, the excess weight was 4+ tons!
A number of weighbridge manufacturers has pointed out that the weighing facilities available at MoT testing stations will enable many more operators conveniently to obtain vehicleand axleload certificates if they suspect that loading is excessive.
But surely it can be assumed that no operator will voluntarily visit a testing station for this purpose unless enforcement of the regulations is so thorough and frequent that infringement is extremely costly. And how long would drivers on average be kept at a station awaiting certification (typically the station staff will be engaged for most of the working day on routine work), and what will be done if the vehicle or an axle is overloaded? Removal of the excess part of the load could involve the use of special equipment, the suitability of which would depend on the type of load. And where could the load be stored pending collection by another vehicle? If a vehicle were checked on a non-MoT weighbridge and loading was literally or nominally excessive, even the conscientious operator would normally risk being caught on the intended trip and try to put the matter right on subsequent trips.
The biggest question-mark in the minds of operators relates to the weight latitude they will be allowed with due regard to the accuracy of the weighing equipment employed by the MoT and of the equipment they could afford to purchase for their own use. Although weighbridges approved by the Board of Trade have to be regularly certified by the weights and measures people, separately weighing an axle or group of axles with the remaining axle or axles standing on the ground can produce substantial inaccuracies, particularly if the ground is not level at one or both ends of the weighbridge.
Guarded optimism Some operators are guardedly optimistic that enforcement of the regulations will be far from strict—that the MoT is not going to bother about the operator who "inadvertently" overloads a maximum-load vehicle by say, 10 per cent—but they are well aware that overloading one of the axles by more than this amount is very easily done even when the total load is well within the allowance maximum.
Operators who pride themselves on being perfectionists are realistically conscious that getting load distribution right is worth while for its own sake and although they may be satisfied that the g.v.w. of a particular vehicle and individual axle loads are legal, they will take trouble, if they can, to distribute the load according to recommended proportions in the interests of braking and handling. While an apportioning valve in the brake system assists in maintaining the efficiency of the system with change of load, its operation has no effect on axle or tyre loading, which is an important factor in the braking and handling characteristics of the vehicle.
Effect on brakes Because they carry evenly distributed measured loads, tanker operators are not normally concerned with overloading but to a greater extent than most operators they are concerned to provide good braking and handling on account of the value of the load and the additional hazards that may be created in the event of an accident. Of related significance, the workshop staff at the central vehicle depot of the Calor Gas Co. Ltd., Rushton, Northamptonshire, intend to use a Checkweight portable weighing machine, produced by S. G. Brown Ltd., a member of the Hawker Siddeley Group Ltd.. 32 Duke Street, St. James's, London, SW1, in conjunction with a Triangle brake tester to analyse the effect of loaddistribution variations on braking efficiency. The Checkweight will also be employed to determine the optimum position of the king-pin of York adjustable couplings on semi-trailer outfits in relation to the driving axle.
While weighbridge facilities are currently available at a local railway yard and a factory, repeat trips to either premises is very time wasting. The Checkweight incorporates an hydraulic load cell and weighs only 501b, which enables it to be lifted by one man. A single unit can be used to weigh each wheel individually and the sum of the wheel loads gives the total gross weight of the vehicle.
Critics of portable weighing machines object to them on the ground that they are not sufficiently accurate. An accuracy of + 1 cwt, is claimed by S. G. Brown for the Checkweight, whereas the certified accuracy of a weighbridge is one division, normally of 141b. Weighbridge inaccuracy is a function of hysteresis of the mechanism, and it is notable that tyre hysteresis can also affect the reading. In a search for extreme accuracy, technicians of the Dunlop Co. devised a special machine which was built by Elliott Brothers (London) Ltd., Century Works, Lewisham, London, SE13, the operation of which involves taking a weight reading after the loaded platform has been moved downwards a certain amount to a datum line and a second reading after the platform has been moved upwards to the line. The average of the two readings is then calculated and this balances-out the effects of hysteresis.
I suggest that the nominal accuracy of a weighing machine is relatively unimportant compared with its "repeat accuracy", inaccuracy being a measure of the maximum difference between a large number of readings of the same load. If an error is stable a correction factor can be readily applied, as in the case, for example, of a critical speedometer reading.
In the same category as the S. G. Brown Checkweight with regards to portability, load-measuring jacks of Swedish origin are marketed by Harvey Frost and Co. Ltd., Dunmow Road, Bishop's Stortford, Herts., and although Skyhi Ltd., Buckingham Avenue, Slough, Bucks, has discontinued production of this type of jack because of falling demand it would manufacture any model in the range if it were required in sufficient quantity. The Harvey Frost
jacks have capacities of 8 tons to 25 tons and weigh 1841b to 664lb, while the cost of the 8 ton model is less than £12. Capacities of the Skyhi models range from 4 tons to 15 tons and weigh from 301b to 801b.
In a depot check of vehicle weight, Harvey Frost recommends that two jacks are employed to lift and weigh the back axle of a four-wheeler and a single jack to weigh the front axle. An accuracy of + Icwt is claimed.
Makers of a wide variety of weighbridges, including the loadcell type, W. and T. Avery Ltd., Soho Foundry, Birmingham, 40, state that they would produce a fully-portable unit if there were sufficient demand.
Difficulties made public
Since preparation of this article was started, the difficulties of obtaining accurate vehicle and axle weights and the urgent need for portable weighing machines have been mentioned publically by a number of operators, notably by Mr. L. G. Reed, of United Builders Merchants Transport Ltd., when he was speaking at the TRTA one-day conference on braking, plating and testing on June 29. Mr. Reed said that some of the results of checking the axle weights of 24-ton-gross four-axle vehicles had made his hair stand on end and he posed the question as to whether the enforcement authorities would allow a 5 per cent latitude on weight.
On the same theme, Mr. G. Turvey, assistant secretary of the TRTA, said in a paper on new legislation that more thought should be given to providing better public weighing facilities, that operators should equip themselves with weighing facilities as best they could and that there was need for accurate instrumentation that could be incorporated in the vehicle.
According to unconfirmed reports, such a system based on load cells has been successfully developed in Russia; S. G. Brown has produced an experimental system that is satisfactory but too costly for commercial application and a leading UK weighbridge manufacturer is known to be developing a built-in type. S. G. Brown points out that a system could readily be developed for a vehicle if all the axles had air suspension.
Complex legal hazards
As mentioned by Mr. Reed and other speakers at the conference, removal of part of the load from the rear of a delivery vehicle during the run, can result in overloading the front axle, the rated load on which will be given on the plate. The maximum fine for overloading is now £200, which applies to axle loading as well as vehicle loading, and this example of the way in which an axle can be inadvertently overloaded by removal of part of the load particularly highlights the complexity of the legal hazards that face wouldbe law-abiding operators if a fairly generous weight latitude is not allowed. But even a generous latitude will not safeguard operators against prosecution unless they take steps to exploit the best weighing facilities available.
In the case of the Elliot load-cell weighbridge, the cells are of the strain-gauge electrical-recording type and the gauge may be located if required at a considerable distance from the weighbridge. The S-type cell essentially comprises a high-tensile alloy-steel billet to which high-stability strain gauges are bonded, the deflection under full load being about 0.0041n.
The capacity of the weighbridge is divided into discrete "over lapping" ranges and if required print-out equipment may be used for recording on a paper strip or card identifying information such as gross weight, tare weight and so on. In one special type of unit developed since the first Board of Trade-approved weighbridge was installed the platform is divided into two sections, which enables readings to be taken of axle loads as well as the total load.
Also of the resistance strain-gauge type, the load cells of weighbridges produced by Girling Ltd., Kings Road, Tyseley, Birmingham, 11, are employed in a visual weight indicator /recorder system, operating on the principle of the self-balancing electrical bridge incorporating a motor-driven potentiometer. The weight signal from the load cells is counterbalanced by an equal signal from the potentiometer which is operated by the motor until a balance is obtained. Weight is displayed on a dial or in the form of illuminated numerals.
Sloping weighbridge
Of special interest, Girling recently introduced the Sloping Weighbridge, which can be installed in ground with inclines in the lateral or longitudinal direction or having a compound arrangement of slopes. In the case of the sloping weighbridge on the premises of Joseph Lucas Ltd., in Birmingham, the size of the platform is 30 ft. by 9 ft. and the unit is located on a 1 in 15 incline, one end of the weighbridge being 24 in. higher than the other. In the case of the Avery strain-gauge load cell, the system incorporates a special combined self-aligning and free-motion unit that ensures that no unwanted forces act upon the cell during the weighing operation. The company has developed a portable form of unit for weighing and balancing rail-truck and locomotive wheel loads.
Ekco Electronics Ltd., Southend-on-Sea, Essex, states that the company,s strain gauge load-cell can be adapted to a variety of uses, including, in portable form, the weighing of vehicles and axles. The company is prepared to consider catering for particular applications.
When asked to compare the hydrostatic load cell with the strain gauge type on the day that the S. G. Brown Checkweight was announced, a spokesman of the company claimed that it was preferable to employ a hydrostatic cell for portable equipment because accuracy was not dependent upon locating the load exactly over the cell, The wheel of the vehicle could therefore be driven over the platform of the unit at a slow speed to obtain a reading; placement of the wheel on the cell axis would be difficult and time consuming.
Although the cost factor had dictated the use of a cell that did not give extreme accuracy, a very high degree of accuracy was obtainable. In the Checkweight, the platform load is transmitted to the cell by three knife-edge-mounted radially located beam members and the cell is connected by capillary tube to a Burdon tube type of gauge.