An Inverted Air-cooled nine Explained
Page 44
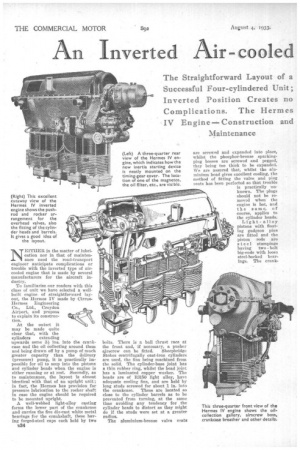
Page 45
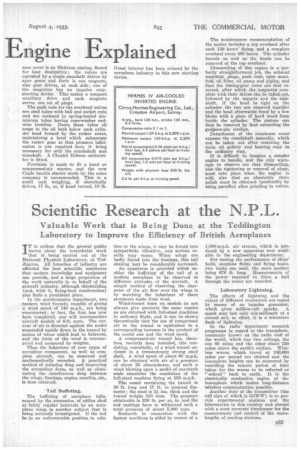
If you've noticed an error in this article please click here to report it so we can fix it.
The Straightforward. Layout of a Successful Four-cylindered Unit ; Inverted Position Creates no mplications. The Hermes IV Engine Construction and Maintenance
NEITHER in the matter of lubrication nor in that of maintenance need the road-transport engineer anticipate complications or trouble with the inverted type of aircooled engine that is made by several manufacturers for the aircraft industry.
To familiarize our readers with this class of unit we have selected a wellbuilt engine of straightforward layout, the Hermes IV made by CirrusHermes Engineering Co., Ltd., Croydon Airport, and propose to explain its construction.
At the outset it may be made quite clear that, with the cylinders extending upwards some4.3-1 ins, into the crankcase and the oil collecting around them and being drawn off by a pump of much greater capacity than the delivery (pressure) pump, it is practically impossible for oil to seep into the pistons and cylinder heads when the engine is either running or at rest. Secondly, as to maintenance, the layout is almost identical with that of an upright unit ; in fact, the Hermes has provision for pressure lubrication to the rocker shaft in case the engine should be required to be mounted upright.
A well-webbed light-alloy casting forms the lower part of the crankcase and carries the five die-cast white metal bearings for the crankshaft, these having forged-steel caps each held by two
B34
bolts. There is a ball thrust race at the front and, if necessary, a pusher airscrew can be fitted. Sheepbridge Stokes centrifugally east-iron cylinders are used, the fins being machined from the solid. The cylinder-base joint has a thin rubber ring, whilst the head joint has a laminated copper washer. The heads are of RR50 light alloy, have adequate cooling fins, and are held by long studs screwed for about 1 in. into the crankcase. These are located so close to the cylinder barrels as to be prevented from turning, at the same time avoiding any tendency for the cylinder heads to distort as they might do if the studs were set at a greater radius.
The aluminium-bronze valve seats are screwed and expanded into place, whilst the phosphor-bronze sparkingplug bosses are screwed and pegged, they being too thick to be expanded. We are assured that, whilst the aluminium head gives excellent cooling, the method of fitting the valve and ping seats has been perfected so that trouble is practically unknown. The plugs should not be removed when the engine is hot, and the same, of course, applies to the cylinder beads.
Light -allay pistons with floating gudgeon pins • are fitted and the piston rods are steel stampings having two bolt big-ends with loose steel-backed bearings. The crank case cover is an Elektron casting, finned for heat dissipation ; the valves are operated by a single camshaft driven by spur gears and there is one magneto, also gear driven, at each side; one of the magnetos has an impulse easystarting device. This makes a compact auxiliary drive and each magneto serves one set of plugs.
The push rods for the overhead valves are steel tubes with ball and socket ends and are enclosed in spring-loaded aluminium tubes having cone-washer endwise location. Down these tubes oil seeps to the oil bath below each cylinder head formed by the rocker cover, maintaining a level which submerges the rocker gear so that pressure lubrication is not required here, it being necessary for only the crankshaft and camshaft. A Claudel Hobson carburetter is fitted.
Provision is made to fit a hand or compressed-air starter, and the new Caple inertia starter made by the same company is recommended. This is a small unit weighing, if electrically driven, 17 lb., or, if hand turned, 10 lb. Great interest has been evinced by the aeroplane industry in this new starting device.
The maintenance recommendation of the maker includes a top overhaul after each 130 hours' flying, and a complete overhaul every 400 hours. The cylinder barrels as well as the heads can be removed at the top overhaul, Dismantling of this engine is aperfectly straightforward job, the exhaust manifold, plugs, push rods, inlet manifold, oil filter, oil pump and piping, and then the timing-gear cover are first removed, after which the magnetos complete with their drives can be taken out, followed by the tappets and the CAMshaft. If the head be tight on the cylinder the two are removed together and the head afterwards freed by a few blows with a piece of hard wood from inside the cylinder. The pistons can then be removed by first extracting the gudgeon-pin cirelips.
Detachment of the crankcase cover exposes the crankshaft assembly, which can be taken out after removing the main oil gallery and bearing caps in the ordinary way.
It is difficult to imagine a simpler engine to handle, and the only warnings to observe are that dismantling, also the tightening or removal of plugs, must take place when the engine is cold, also that an absolutely clean polish must he obtained (preferably by using paraffin) after grinding in valves.