RIDING HIGI RIDING RIGHT
Page 88
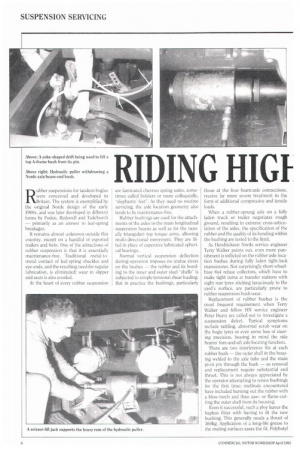
Page 89
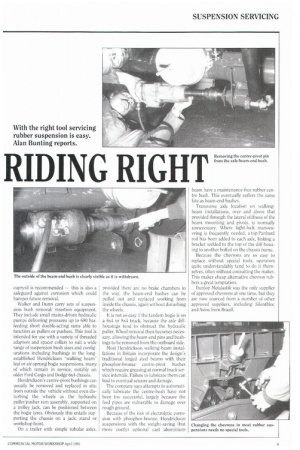
If you've noticed an error in this article please click here to report it so we can fix it.
Rubber suspensions for tandem bogies were conceived and developed in Britain. The system is exemplified by the original Norde design of the early 1960s, and was later developed in different forms by Foden, Rydewell and Tadchurch — primarily as an answer to leaf-spring breakages.
It remains almost unknown outside this country. except on a handful of exported trailers and 6x4s. One of the attractions of rubber suspension is that iL is essentially maintenance-free. Traditional metal-tometal contact of leaf-spring shackles and eye-ends, and the resulting need for regular lubrication, is eliminated; wear in slipper end seats is also avoided.
At the heart of every rubber suspension
are laminated chevron spring units, sometimes called bolsters or more colloquially, "elephants. feet". As they need no routine servicing. the axle location geometry also lends to be maintenance-free.
Rubber bushings are used for the attachments of the axles to the main longitudinal suspension beams as well as for the (usually triangular) top torque arms, allowing multi-directional movement. They are fitted in place of expensive lubricated spherical hearings.
Normal vertical suspension deflection during operation imposes no undue stress on the bushes — the rubber and its bonding to the inner and outer steel -shells" is subjected to simple torsional shear loading. But in practice the bushings, particularly
those at the four beam/axle connections, receive far more severe treatment in the form of additional compressive and tensile loads.
When a rubber-sprung axle on a fully laden truck or trailer negotiates rough ground. resulting in extreme cross-articulation of the axles, the specification of the rubber and the quality of its bonding within the bushing are tested to the limit.
As I lendrickson Norde service engineer.
Terry Walker points out, even more punishment is inflicted on the rubber axle-loca tion bushes during fully laden tight-lock manoeuvres. Not surprisingly short-wheelbase 6x4 refuse collectors, which have to make tight turns at transfer stations with eight rear tyres sticking tenaciously to the yard's surface, are particularly prone to rubber suspension bush wear.
Replacement of rubber bushes is the most frequent requirement when Terry Walker and fellow HN service engineer Peter Dunn are called out to investigate a suspension defect. Typical symptoms include rattling, abnormal scrub wear on the bogie tyres or even some loss of steering precision, bearing in mind the side beams' fore-and-aft axle locating function.
There are two interference fits at each rubber bush — the outer shell in the hous ing welded to the axle tube and the main pivot pin through the bush — so removal and replacement require substantial end thrust. This is not always appreciated by the operator attempting to renew bushings for the first time: methods encountered have included burning out the rubber with a blow-torch and then sawor flame-cutling the outer shell from its housing.
Even if successful, such a ploy leaves the hapless fitter with having to fit the new bushing. This generally needs a thrust of 360kg. Application of a long-life grease to the mating surfaces eases the fit. Polybutyl cuprysil is recommended — this is also a safeguard against corrosion which could hamper future removal.
Walker and Dunn carry sets of suspension bush removal/ insertion equipment. They include small mains-driven hydraulic pumps delivering pressures up to 680 bar, feeding short double-acting rams able to function as pullers or pushers. This tool is intended for use with a variety of threaded adaptors and spacer collars to suit a wide range of suspension hush sizes and configurations including bushings in the longestablished Hendrickson "walking beam" leaf or air-sprung bogie suspensions, many of which remain in service, notably on older Ford Cargo and Dodge 6x4 chassis.
Ilendrickson's centre-pivot bushings can usually be removed and replaced in situ from outside the vehicle without even disturbing the wheels as the hydraulic puller/pusher ram assembly, supported on a trolley jack, can be positioned between the bogie tyres. Obviously this entails supporting the chassis on a jack, stand or workshop hoist.
On a trailer with simple tubular axles, provided there are no brake chambers in the way, the beam-end bushes can be pulled out and replaced working from inside the chassis, again without disturbing the wheels, It is not so easy if the tandem bogie is on a 6x4 or 8x4 truck, because the axle diffhousings Lend to obstruct the hydraulic puller. Wheel removal then becomes necessary, allowing the beam-end pins and bushings to be removed from the outboard side.
Most Hendrickson walking-beam installations in Britain incorporate the design's traditional forged steel beams with their phosphor-bronze centre-pivot bushes which require greasing at normal truck service intervals, Failure to lubricate them can lead to eventual seizure and damage.
The company says attempts to automatically lubricate the centre-bush have not been too successful, largely because the feed pipes are vulnerable to damage over rough ground.
Because of the risk of electrolytic corrosion with phosphor-bronze. Hendrickson suspensions with the weight-saving (but more costly) optional cast aluminium beam have a maintenance-free rubber centre bush. This eventually suffers the same fate as beam-end bushes.
Transverse axle location on walkingbeam installations, over and above that provided through the lateral stiffness of the beam mounting and pivots, is normally unnecessary. Where Light-lock manoeuvring is frequently needed, a top Panhard rod has been added to each axle, linking a bracket welded to the top of the diff-housing to another bolted on the chassis frame.
Because the chevrons are so easy to replace without special tools, operators quite understandably tend to do it themselves, often without consulting the maker. This makes cheap alternative chevron rubbers a great temptation.
Dunlop Melalaslik was the only supplier of approved chevrons at one time, hut they are now sourced from a number of other approved suppliers, including Silentbloc and Axios from Brazil.