WHEELS & TYRES
Page 42
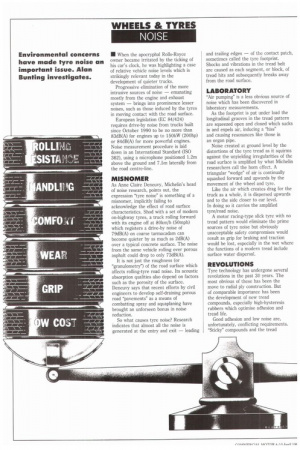
Page 43
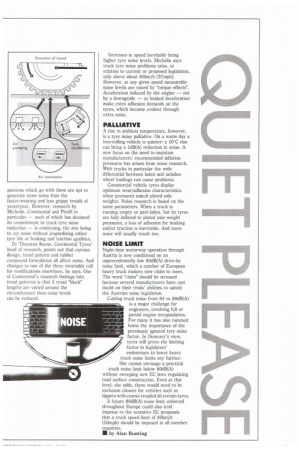
If you've noticed an error in this article please click here to report it so we can fix it.
NOISE
• When the apocryphal Rolls-Royce owner became irritated by the ticking of his car's clock, he was highlighting a case of relative vehicle noise levels which is strikingly relevant today in the development of quieter trucks.
Progressive elimination of the more intrusive sources of noise — emanating mostly from the engine and exhaust system — brings into prominence lesser noises, such as those induced by the tyres in moving contact with the road surface.
European legislation (EC 84/424) requires drive-by noise from trucks built since October 1990 to be no more than 83dB(A) for engines up to 150kW (200hp) or 84dB(A) for more powerful engines. Noise measurement procedure is laid down in an International Standard (ISO 362), using a microphone positioned 1.2m above the ground and 7.5m laterally from the road centre-line.
MISNOMER
As Anne Claire Deneuvy, Michelin's head of noise research, points out, the expression "tyre noise" is something of a misnomer, implicitly failing to acknowledge the effect of road surface characteristics. Shod with a set of modern on-highway tyres, a truck rolling forward with its engine off at 80km/h (50mph) which registers a drive-by noise of 79dB(A) on coarse tarmacadam can become quieter by as much as 2dB(A) over a typical concrete surface. The noise from the same vehicle rolling over porous asphalt could drop to only 73dB(A).
It is not just the roughness (or "granulometry'D of the road surface which affects rolling-tyre road noise. Its acoustic absorption qualities also depend on factors such as the porosity of the surface. Deneuvy says that recent efforts by civil engineers to develop self-draining porous road "pavements" as a means of combatting spray and aquaplaning have brought an unforseen bonus in noise reduction.
So what causes tyre noise? Research indicates that almost all the noise is generated at the entry and exit — leading and trailing edges — of the contact patch, sometimes called the tyre footprint. Shocks and vibrations in the tread belt are caused as each segment, or block, of tread hits and subsequently breaks away from the road surface.
LABORATORY
"Air pumping" is a less obvious source of noise which has been discovered in laboratory measurements.
As the footprint is put under load the longitudinal grooves in the tread pattern are squeezed open and closed which sucks in and expels air, inducing a "hiss" and causing resonances like those in an organ pipe.
Noise created at ground level by the distortions of the tyre tread as it squirms against the unyielding irregularities of the road surface is amplified by what Michelin researchers call the horn effect. A triangular "wedge" of air is continually squashed forward and upwards by the movement of the wheel and tyre.
Like the air which creates drag for the truck as a whole, it is dispersed upwards and to the side closer to ear level. In doing so it carries the amplified tyre/road noise.
A motor racing-type slick tyre with no tread pattern would eliminate the prime sources of tyre noise but obviously unacceptable safety compromises would result as grip for braking and traction would be lost, especially in the wet where the functions of a modern tread include surface water dispersal.
REVOLUTIONS
Tyre technology has undergone several revolutions in the past 30 years. The most obvious of these has been the move to radial ply construction. But of comparable importance has been the development of new tread compounds, especially high-hysteresis rubbers which optimise adhesion and tread life.
Good adhesion and low noise are, unfortunately, conflicting requirements. "Sticky" compounds and the tread
patterns which go with them are apt to generate more noise than the faster-wearing and less grippy treads of yesteryear. However, research by Michelin, Continental and Pirelli in particular — each of which has declared its commitment to truck tyre noise reduction — is continuing, the aim being to cut noise without jeopardising either tyre life or braking and traction qualities.
Dr Thorsten Reese, Continental Tyres' head of research, points out that carcass design, tread pattern and rubber compound formulation all affect noise. And changes to one of the three invariably call for modifications elsewhere, he says. One of Continental's research findings into tread patterns is that if tread "block" lengths are varied around the circumference then noise levels can be reduced. Increases in speed inevitably bring higher tyre noise levels. Michelin says truck tyre noise problems arise, in relation to current or proposed legislation, only above about 60km/h (37mph). However, at any given speed measurable noise levels are raised by "torque effects". Acceleration induced by the engine — not by a downgrade — or braked deceleration make extra adhesion demands on the tyres, which become evident through extra noise.
PALLIATIVE
A rise in ambient temperature, however, is a tyre noise palliative. On a warm day a free-rolling vehicle is quieter: a 10°C rise can bring a ldB(A) reduction in noise. A new focus on the need to maintain manufacturers' recommended inflation pressures has arisen from noise research. With trucks in particular the wide differential between laden and unladen wheel loadings can cause problems.
Commercial vehicle tyres display optimum wear/adhesion characteristics when pressures match plated axle weights. Noise research is based on the same parameters. When a truck is running empty or part-laden, but its tyres are fully inflated to plated axle weight pressures, a loss of adhesion for braking and/or traction is inevitable. And more noise will usually result too.
NOISE LIMIT
Night-time motorway operation through Austria is now conditional on an unprecedentedly low 80dB(A) drive-by noise limit, which a number of European heavy truck makers now claim to meet. The word "claim" should be stressed because several manufacturers have cast doubt on their rivals' abilities to satisfy the Austrian noise legislation.
Cutting truck noise from 84 to 80dB(A) is a major challenge for engineers, involving full or partial engine encapsulation. For many it has also rammed home the importance of the previously ignored tyre noise factor. In Deneuvy's view, tyres will prove the limiting factor in legislators' endeavours to lower heavy truck noise limits any further. She cannot envisage a practical truck noise limit below 80dB(A) without sweeping new EC laws regulating road surface construction. Even at that level, she adds, there would need to be exclusion clauses for vehicles such as tippers with coarse-treaded all-terrain tyres.
A future 80dB(A) noise limit enforced throughout Europe could also lend impetus to the tentative EC proposals that a truck speed limit of 80km/h (50mph) should be imposed in all member countries.
• by Alan Bunting