Air Suspension and the Bodybuilder
Page 66
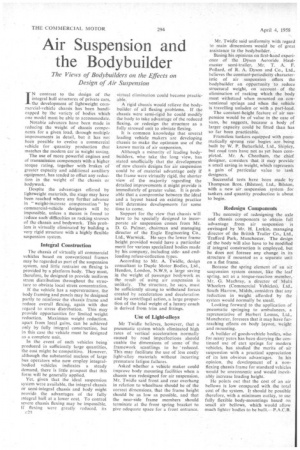
If you've noticed an error in this article please click here to report it so we can fix it.
The Views of Bodybuilders on the Effects on Design of Air Suspension
IN contrast to the design of the integral hull structures of private cars, the development of lightweight com
mercial-vehicle chassis has been handicapped by the variety of bodies which one model must be able to accommodate.
Notable advances have been made in reducing the weight of chassis compo, nents for a given load, through multiple improvements in detail, but it has not been possible to evolve a commercial vehicle for quantity production that matches the modern car in weight saving.
The use of more powerful engines and of transmission components with a higher torque rating, together with brakes of greater capacity and additional auxiliary equipment, has tended to offset any reduction in the weight of the chassis or bodywork.
Despite the advantages offered by lightweight materials, the stage may have been reached where any further advance in " weight-increase compensation" by commercial-vehicle designers will he impossible, unless a means is found to reduce such' difficulties as racking stresses of the chassis and bodywork. This problem is virtually eliminated by building a very rigid structure with a highly flexible suspension system.
Integral Construction
The chassis of virtually all commercial vehicles based on conventional frames may be regarded as part of the suspension system, and little restraint on flexing is provided by a platform body. They must, therefore, be designed to provide uniform stress distribution throughout the structure to obviate local stress concentration.
If the vehicle has a superstructure, the body framing and panels may be designed partly to reinforce the chassis frame and reduce overall flexing, again with due regard to stress distribution. This may provide opportunities for limited weight reduction. Maximum weight reduction, apart from local gains, can be achieved only by fully integral construction, but in this case the vehicle must be designed as a complete unit.
In the event of such vehicles being produced in sufficiently large quantities, the cost might be competitive. However, although the substantial nucleus of large bus operators who now employ integralbodied vehicles indicates a steady demand, there is little prospect that this form will be generally applied.
Yet, given that the ideal suspension system were available, the integral chassis or semi-integral chassis and body might provide the advantages of the fully integral hull at a lower cost. To control severe chassis flexing may be impossible. If flexing were greatly reduced, its c2q virtual elimination could become practicable.
A rigid chassis would relieve the bodybuilder of all flexing problems. if the chassis were semi-rigid he could modify the body to take advantage of the reduced flexing, or redesign the structure as a fully stressed unit to obviate flexing.
It is common knowledge that several leading vehicle makers are developing chassis to make the optimum use of the known merits of air suspension.
Although a minority of leading bodybuilders, who take the long view, has
slated unofficially that the development of new chassis designs for air suspension could be of material advantage only if the frame were virtually rigid, the shorter view of the majority regarding the detailed improvements it might provide is immediately of greater value. It is probable that a compromise between the ideal and a layout based on existing practice will determine developments for some time to come.
Support for the view that chassis will have to be specially designed to incor porate air suspension comes from Mr.
D. G. Palmer, chairman and managing director of the Eagle Engineering Co., Ltd., Warwick. He says the lower frame height provided would have a particular merit for various specialized bodies made by his company, including sideand endloading refuse-collection types.
According to Mr. A. Twidle, design consultant to Duple Motor Bodies, Ltd., Hendon, London, N.W.9, a large saving in the weight of passenger bodywork as the result of using air suspension is unlikely. The structure, he says, must be sufficiently strong to withstand forces created by acceleration and deceleration and by centrifugal action, a large proportion of the total weight of a luxury coach is derived from trim and fittings.
Use of Light-alloys
Mr Twidle believes, however, that a pneumatic system which eliminated high rates of vertical acceleration normally caused by road imperfections should enable the dimensions of some of the framework scantlings to be reduced. This may facilitate the use of less costly light-alloy materials without incurring premature fatigue failures.
Asked whether a vehicle maker could improve body mounting facilities when a chassis was redesigned for air suspension, Mr. Twidle said front and rear overhang in relation to wheelbase should be of the correct dimensions, that the frame height should be as low as possible, and that the near-side frame members should terminate at the front spring bracket to give adequate space for a front entrance. Mr. Twidle said uniformity with regard to main dimensions would be of great assistance to the bodybuilder.
Basing his opinions on first-hand experience of the Dyson Aeroride Haulmaster semi-trailer, Mr. T. A. F. Pollard, of R. A. Dyson and Co., Ltd., believes the constant-periodicity characteristic of air suspension offers the bodybuilder an opportunity to reduce structural weight, on account of the elimination of racking which the body must withstand when mounted on conventional springs and when the vehicle is travelling unladen or with a part-load.
The constant-height feature of air suspension would be of value in the case of vans, he suggests, because a body of larger capacity could be fitted than has so far been practicable.
Frameless tankers equipped with pneumatically sprung rear bogies are being built by W. P. Butterfield, Ltd., Shipley, but road tests have not as yet been completed.' Mr. A. Cheetham, the chief designer, considers that it may provide a small saving in weight, which represents a gain of particular value to tank designers.
Successful tests have been made by Thompson Bros. (Bilston), Ltd., Bilston, with a new air suspension system for tankers and quantity production is about to begin.
Redesign Components
The necessity of redesigning the axle and chassis components to obtain full advantage from air suspension is envisaged by Mr. H. Larkin, managing director of the British Trailer Co., Ltd., Trafford Park, Manchester. The design of the body will also have to be modified if integral construction is employed, but he does not foresee any change in its structure if mounted as a separate unit on a flat frame.
Because the spring element of an air suspension system cannot, like the leaf spring, act as a torque-reaction member, Mr. G. Machray, a director of Multi Wheelers (Commercial Vehicles), Ltd., South Harrow, Middx, considers that any reduction in weight afforded by the system would normally be small.
Looking forward to the application of pneumatic springing to ambulances, a representative of Herbert Lomas, Ltd., Manchester, foresees that it may have farreaching effects on body layout, weight and mounting.
A builder of goods-vehicle bodies, who for many years has been decrying the continued use of cart springs for modern vehicles, has studied the merits of air suspension with a practical appreciation of its less obvious advantages. In his opinion, the development of a nonflexing chassis frame for standard vehicles would be uneconomic and would inevitably increase loading height.
He points out that the cost of an air bellows is low compared with the total cost of the system. It should be possible therefore, with a minimum outlay, to use fully flexible body-mountings based on small air bellows, which would allow much lighter bodies to be built.—P.A.C.B.