WALLS OF CONFUSION
Page 84

Page 85
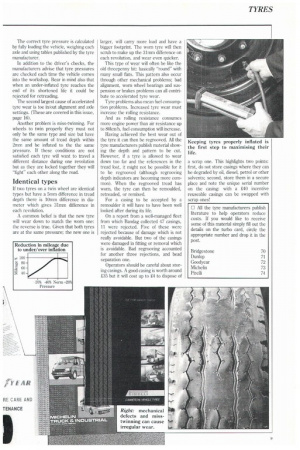
If you've noticed an error in this article please click here to report it so we can fix it.
Getting the right tyre is just the first important step in reducing costs.
Any attempt to reduce truck running costs must consider tyres. Commercial Motor's "Table of Operating Costs" shows tyres are the fourth highest running expense after fuel, depreciation and maintenance on 38tonners. One maximum weight articulated unit total tyre costs are calculated at 10.72 pence per mile.
The first step is to ensure the right tyres are fitted to each vehicle. There are 10 truck and five trailer tyres in Michelin's range, for example. The designs go from high-mileage/high-speed tyres for motorway work to on/off road tyres capable of handling all types of work.
The wrong choice can be disastrous. High-speed road tyres on a vehicle doing on/off road work will be ruined in a matter of days. Similarly if you put on/off road tyres on a trunking vehicle they will not give the life or the fuel consumption available from tyres designed for the job. But they will give reasonable service. In a nutshell the trick is to select the tyre suitable for the most arduous work expected of the vehicle. It's cheaper that way.
Legal aspects
However, there are legal aspects to be considered. CSEU regulations say that the tyre must be rated for the maximum weight and speed allowed for that vehicle. This raises complications.
All the information needed is on the side of the tyre but it is coded. Referring to the illustration, the 295 is the nominal section width in millimetres. The 80 is the aspect ratio, ie tyre height divided by tyre width expressed as a percentage. Where there is no aspect ratio marked it will be 100% for tubed and 90% for tubeless tyres. R denotes a radial tyre and 22.5 is the rim diameter in inches. The 152/147 M marking is the load and speed index. To understand these requires a chart. The first number (152) denotes the load carrying capacity when used singularly and the second (147) is when it is twinned. The relevant chart shows these equate to 3,550kg (single) and 3.075kg (twin).
A 10.5 tonne drive axle using four tyres must have a
twinned loadcarrying capacity of at least 2,625kg. On a 6.5 tonne front axle single tyres must have a load-carrying capacity of more than 3,250kg. Speed rating is indicated by the letter following the load rating, in this case an M. That represents a maximum speed of 130km/h (81mph).
Among the other information on the sidewall is the only one which is legally important: the E mark. All new CV tyres must be E-marked to show they conform to the relevant regulations. Remoulds need not be E-marked but in the UK they must conform to BSAU144B and have that marked on the sidewall.
Now that you have the right tyre which can legally carry the load imposed on it at the right speed all you have to do is make it last as long as possible.
All tyre manufacturers agree the most important part of a tyre for durability is the air inside it. Central Tyres surveyed more than 25,000 truck tyres and found that almost 25% were under inflated by more than 10%. This will lead to a 15% reduction in tyre life, says the manufacturer. However, to keep the tyres at the right pressure you first have to determine what the pressure should be. The correct tyre pressure is calculated by fully loading the vehicle, weighing each axle and using tables published by the tyre manufacturer.
In addition to the driver's checks, the manufacturers advise that tyre pressures are checked each time the vehicle comes into the workshop. Bear in mind also that when an under-inflated tyre reaches the end of its shortened life it could be rejected for retreading.
The second largest cause of accelerated tyre wear is toe in/out alignment and axle settings. (These are covered in this issue, page 16).
Another problem is miss-twinning. For wheels to twin properly they must not only be the same type and size but have the same amount of tread depth within 2nim and be inflated to the the same pressure. If these conditions are not satisfied each tyre will want to travel a different distance during one revolution but as they are locked together they will "fight" each other along the road.
Identical types
If two 4,res on a twin wheel are identical types but have a 5mm difference in tread depth there is 10nun difference in diameter which gives 31nun difference in each revolution.
A common belief is that the new tyre will wear down to match the worn one: the reverse is true. Given that both tyres are at the same pressure; the new one is larger, will carry more load and have a bigger footprint. The worn tyre will then scrub to make up the 31mm difference on each revolution, and wear even quicker.
This type of wear will often he like the old threepenny bit: basically "round" with many small flats. This pattern also occur through other mechanical problems; bad alignment, worn wheel bearings and suspension or brakes problems can all contribute to accelerated tyre wear.
Tyre problems also mean fuel consumption problems. Increased tyre wear must increase the rolling resistance.
And as rolling resistance consumes more engine power than air resistance up to 80km/h, fuel consumption will increase.
Having achieved the best wear out of the tyre it can then be regrooved. All the tyre manufacturers publish material showing the depth and pattern to be cut. However, if a tyre is allowed to wear down too far and the references in the tread lost, it might not be possible for it to be regrooved (although regrooving depth indicators are becoming more common). When the regrooved tread has worn, the tyre can then be remoulded, retreaded, or remixed.
For a casing to be accepted by a remoulder it will have to have been well looked after during its life.
On a report from a well-managed fleet from which Bandag collected 47 casings, 11 were rejected. Five of these were rejected because of damage which is not really avoidable. But two of the casings were damaged in fitting or removal which is avoidable. Bad regrooving accounted for another three rejections, and bead separation one.
Operators should be careful about storing casings. A good casing is worth around 25 but it will cost up to kcl to dispose of
a scrap one. This highlights two points: first, do not store casings where they can be degraded by oil, diesel, petrol or other solvents; second, store them in a secure place and note the unique serial number on the casing: with a 8:40 incentive reuseable casings can be swapped with scrap ones!