BY D. A. KELSO
Page 43
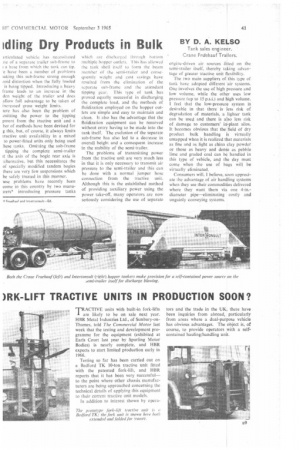
Page 42
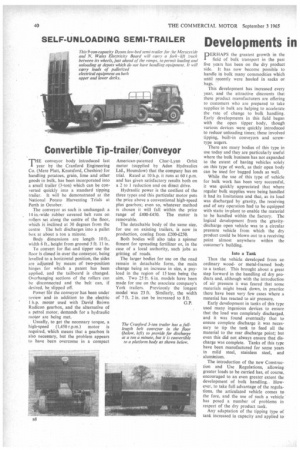
If you've noticed an error in this article please click here to report it so we can fix it.
nolERHAPS the greatest growth in the
I field of bulk transport in the past five years has been on the dry product side. It has now become possible to handle in bulk many commodities which until recently were hauled in sacks or bags.
This development has increased every year, and the attractive discounts that these product manufacturers are offering to customers who are prepared to take supplies in bulk are helping to accelerate the rate of change to bulk handling. Early developments in this field began with the open tipper body, though various devices were quickly introduced to reduce unloading times; these involved tipping, built-in conveyors and screwtype augers.
There are many bodies of this type in use today and they are particularly useful where the bulk business has not expanded to the extent of having vehicles solely on this type of work, as their open body can be used for bagged loads as well.
While the use of this type of vehicle for bulk work has been very successful, it was quickly appreciated that where regular bulk supplies were being handled it had its limitations and that, as its load was discharged by gravity, the receiving end of any operation had to be equipped with static in-plant to enable the material to be handled within the factory. The logical development from the gravitydischarge open vehicle was to a circular pressure vehicle from which the dry product could be blown out to a receiving point almost anywhere within the customer's building.
Into a Tank
Thus the vehicle developed from an ordinary woodor metal-framed body to a tanker. This brought about a great step forward in the handling of dry products and, although with the introduction of air pressure it was feared that some materials might break down, in practice there have been very few cases where a material has reacted to air pressure.
Early development in tanks of this type used many ingenious devices to ensure that the load was completely discharged, and it was found eventually that to ensure complete discharge it was necessary to tip the tank to feed all the material to the rear discharge point; but even this did not always ensure that discharge was complete. Tanks of this type have been manufactured for some years in mild steel, stainless steel, and aluminium.
The introduction of the new Construction and Use Regulations, allowing greater loads to be carried has, of course, encouraged to an even greater extent the development of bulk handling. However, to take full advantage of the regulations, the articulated vehicle comes to the fore, and the use of such a vehicle has posed a number of problems in respect of the dry product tank.
Any adaptation of the tipping type of tank increased in capacity and applied to trticulated vehicle has necessitated Ise of a separate trailer sub-frame to a base from which the tank can tip. .e have been a number of problems taking this sub-frame strong enough loid distortion when the fully loaded is being tipped. Introducing a heavy frame leads to an increase in the den weight of the trailer and does allow full advantage to be taken of increased gross weight limits.
tere has also been the problem of ;mining the power to the tipping pment from the tractive unit and a her of methods have been devised for g this, but, of course, it always limits tractive unit availability in a mixed to power-fitted units only being used hese tanks. Omitting the sub-frame tipping the complete semi-trailer it the axis of the bogie rear axle is .alternative, but this necessitates the of specially modified tandem bogies there are very few suspensions which be safely treated in this manner.
tese problems have recently been come in this country by two manutrers* introducing pressure tanks
which are discharged through bottom multiple hopper outlets. 1 his has allowed the tank shell itself to form the beam member of the semi-trailer and consequently weight and cosi savings have resulted from the elimination of the separate sub-frame and the attendant tipping gear. This type of tank has proved equally successful in discharging the complete load, and the methods of fluidization employed on the hopper outlets are simple and easy to maintain and clean. It also has the advantage that the fluidization equipment can be removed without entry having to be made into the tank itself. The exclusion of the separate sub-frame has also led to a decrease in overall height and a consequent increase in the stability of the semi-trailer.
The problems of transmitting power from the tractive unit are very much less in that it is only necessary to transmit air pressure to the semi-trailer and this can be done with a normal jumper hose connection from the tractive unit. Although this is the established method of providing auxiliary power using the power take-off, many operators are now seriously considering the use of separate engine-driven air sources fitted on the semi-trailer itself, thereby taking advantage of greater tractive unit flexibility.
The two main suppliers of this type of tank have adopted different air systems. One involves the use of high pressure and low volume, while the other uses low pressure (up to 15 p.s.i.) and high volume. I feel that the low-pressure system is desirable in that there; is less risk of degradation of materials, a lighter tank can be used and there. is also less risk of damage to customers' in-plant silos. It becomes obvious that the .field of dry product bulk handling is virtually untapped when it is realized that materials as fine and as light as china clay powder or those as heavy and dense as pebble lime and graded coal can be bandied in this type of vehicle, and the day must come when the use of bags will be virtually eliminated.
Consumers will, I believe, soon appreciate the advantage of air handling systems when they see their commodities delivered where they want them via one 4-in.diameter pipe—eliminating costly and ungainly conveying systems.