Cutting Costs with Autolube...
Page 51
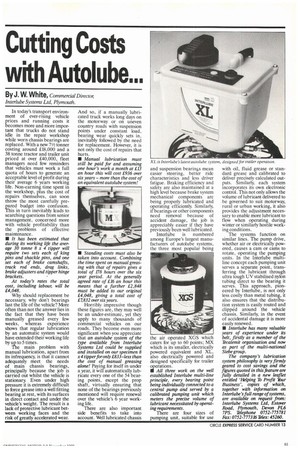
If you've noticed an error in this article please click here to report it so we can fix it.
By J. W. White, Commercial Director; Interlube Systems Ltd, Plymouth.
In today's transport environment of ever-rising vehicle prices and running costs it becomes more and more important that trucks do not stand idle in the repair workshop while worn chassis bearings are replaced. With a new 71/2 tanner costing around £18,000 and a 38 tonne tractor and trailer unit priced at over £40,000, fleet managers need few reminders that vehicles must work a full quota of hours to generate an acceptable level of profit during their average 6 years working life. Non-earning time spent in the workshop, plus the cost of repairs themselves, can soon throw the most carefully prepared budget into confusion, This in turn inevitably leads to searching questions from senior management, concerned more with vehicle profitability than the problems of effective maintenance.
• It has been estimated that during its working life the average 30 tonne 8 x 4 tipper will require two sets each of king pins and shackle pins, and one set each of brake camshafts, track rod ends, drag links, brake adjusters and tipper hinge brackets.
At today's rates the total cost, including labour, will be £4,048.
Why should replacement be necessary, why don't bearings last the life of the vehicle? More often than not the answer lies in the fact that they have been manually greased every few weeks, whereas experience shows that regular lubrication by an automatic system would have extended their working life by up to 5 times. The main problem with manual lubrication, apart from its infrequency, is that it cannot adequately meet the needs of main chassis bearings, principally because the job is carried out whilst the vehicle is stationary Even under high pressure it is extremely difficult to force grease into a well fitting bearing at rest, with its surfaces in direct contact and under the vehicle's weight. The result is a lack of protective lubricant between working faces and the risk of greatly accelerated wear. And so, if a manually lubricated truck works long days on the motorway or on uneven country roads with suspension points under constant load, bearing wear quickly sets in, inevitably followed by the need for replacement. However, it is not only the cost of repairs that hurts.
• Manual lubrication must still be paid for and assuming one hour's work a month at .£13 an hour this will cost £936 over six years — more than the cost of an equivalent autolube system!
• Standing costs must also be taken into account. Combining the time spent on manual greasing with that of repairs gives a total of 178 hours over the six year period. At the generally agreed rate of i16 an hour this means that a further £2,848 must be added to our original £4,048, giving a total cost of fZ832 over six years.
Horribly impressive though these figures are, they may well be an under-estimate, yet they apply to many thousands of commercial vehicles on our roads. They become even more significant when you appreciate that an autolube system of the type available from Interlube Systems Ltd could be supplied and installed on our specimen 8 x4 tipper for only .£833—less than the cost of manual greasing alone! Paying for itself in under a year, it will automatically lubricate every one of the 54 bearing points, except the prop shaft, virtually ensuring that none of the bearings previously mentioned will require renewal over the vehicle's 6 year working life.
There are also important side benefits to take into account. Well lubricated chassis and suspension bearings mean easier steering, better ride characteristics and less driver fatigue. Braking efficiency and safety are also maintained at a high level because brake system mechanical components are being properly lubricated and operating efficiently. Similarly, if bearings or other components need removal because of accident damage, the job is appreciably easier if they have previously been well lubricated.
Interlube is numbered among Europe's largest manufacturers of autolube systems, the three most popular being the air operated XGS which caters for up to 60 points; MX which is its smaller, electrically powered equivalent and XL, also electrically powered and designed specifically for trailer operations. • All three work on the well established Interlube multi-line principle, every bearing point being individually connected to a central pump and served by a calibrated pumping unit which meters the precise volume of lubricant necessitated by operating requirements.
There are four sizes of pumping unit, suitable for use with oil, fluid grease or standard grease and calibrated to deliver precisely calculated outputs. Similarly, each system incorporates its own electronic control. This not only allows the volume of lubricant delivered to be governed to suit motorway, rural or urban working, it also provides the adjustment necessary to enable more lubricant to flow when operating during winter or similarly hostile working conditions.
The systems function on similar lines. The pump drive, whether air or electrically powered, causes a cam or cams to rotate, operating the pumping units. In the Interlube multiline concept each pumping unit serves a separate point, transferring the lubricant through ultra tough UV stabilised nylon tubing direct to the bearing it serves. This approach, pioneered by Interlube, is not only less costly than metal tubing, it also ensures that the distribution system is easily routed and clipped around the vehicle chassis. Similarly, in the event of accidental damage it is more easily renewed. • Interlube has many valuable years of experience under its belt, firstly as a member of the lecalemit organisation and now as part of the multi-national Siebe group.
The company's lubrication system philosophy is very firmly geared to cost savings and the figures quoted in this feature are fully detailed in a new leaflet entitled 'Helping 7s Profit bur Business', copies of which, together with information on Interlube's full range of systems, are available on request from: Interlube Systems Ltd, Estover Road, Plymouth, Devon PL6 7PS. Telephone 0752-775781 Fax: 0752-777316 1elex: 45260.