M ercedes-Benz launched its 3025K eight-legger tipper chassis in the UK
Page 149
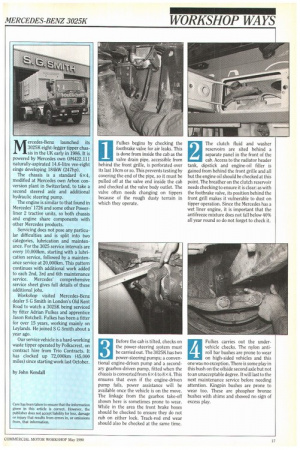
Page 150
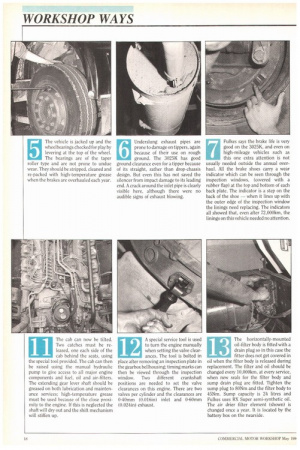
Page 151
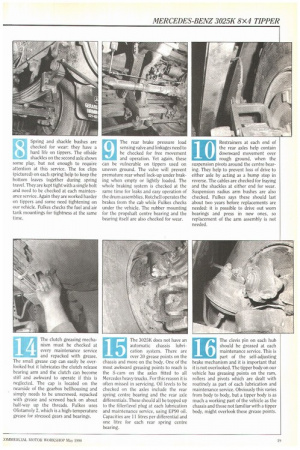
Page 152
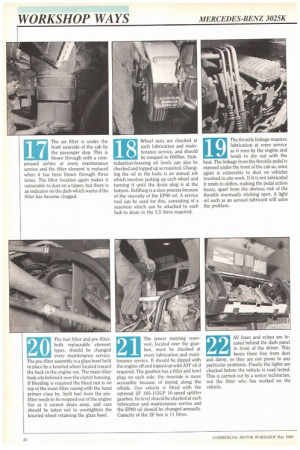
If you've noticed an error in this article please click here to report it so we can fix it.
early in 1986. It is powered by Mercedes own 0422.111 naturally-aspirated 14.6-litre vee-eight einge developing 184kW (247hp).
The chassis is a standard 6 x 4, modified at Mercedes own Arbon conversion plant in Switzerland, to take a second steered axle and additional hydraulic steering pump.
The engine is similar to that found in Mercedes' 1726 and some other Powerliner 2 tractive units, so both chassis and engine share components with other Mercedes products.
Servicing does not pose any particular difficulties and is split into two categories, lubrication and maintenance. For the 3025 service intervals are every 10,0001mi, starting with a lubrication service, followed by a maintenance service at 20,000km. This pattern continues with additional work added to each 2nd, 3rd and 6th maintenance service. Mercedes' comprehensive service sheet gives full details of these additional jobs.
Workshop visited Mercedes-Benz dealer S G Smith in London's Old Kent Road to watch a 3025K being serviced by fitter Adrian Fulkes and apprentice Jason Rotchell. Fulkes has been a fitter for over 15 years, working mainly on Leylands. He joined S G Smith about a year ago.
Our service vehicle is a hard-working waste tipper operated by Polkacrest, on contract hire from Trio Contracts. It has clocked up 72,000km (45,000 miles) since starting work last October.
by John Kendall Fulkes begins by checking the footbrake valve for air leaks. This is done from inside the cab as the valve drain pipe, accessible from behind the front grille, is perforated over its last 10cm or so. This prevents testing by covering the end of the pipe, so it must be pulled off at the valve end inside the cab and checked at the valve body outlet. The valve often needs changing on tippers because of the rough dusty terrain in which they operate.
1
The clutch fluid and washer reservoirs are sited behind a separate panel in the front of the cab. Access to the radiator header tank, dipstick and engine-oil filler is gained from behind the front grille and all but the engine oil should be checked at this point. The breather on the clutch reservoir needs checking to ensure it is clear: as with the footbrake valve, its position behind the front grill makes it vulnerable to dust on tipper operation. Since the Mercedes has a wet liner engine, it is important that the antifreeze mixture does not fall below 40% all year round so do not forget to check it.
Before the cab is tilted, checks on the power-steering system must be carried out. The 3025K has two power-steering pumps; a conventional engine-driven pump and a secondary gearbox-driven pump, fitted when the chassis is converted from 6x4 to 8 x4. This ensures that even if the engine-driven pump fails, power assistance will be available once the vehicle is on the move. The linkage from the gearbox take-off shown here is sometimes prone to wear. While in the area the front brake hoses should be checked to ensure they do not rub on either lock. Track-rod end wear should also be checked at the same time.
3
Fulkes carries out the undervehicle checks. The nylon antiroll bar bushes are prone to wear on high-sided vehicles and this one was no exception. There is some play in this bush on the offside second axle but not to an unacceptable degree. It will last to the next maintenance service before needing attention. Kingpin bushes are prone to wear too. These are phosphor bronze bushes with shims and showed no sign of excess play.
The vehicle is jacked up and the wheelbearings checked for play by levering at the top of the wheel. The bearings are of the taper roller type and are not prone to undue wear. They should be stripped, cleaned and re-packed with high-temperature grease when the brakes are overhauled each year. Underslung exhaust pipes are prone to damage on tippers, again because of their use on rough ground. The 3025K has good ground clearance even for a tipper because of its straight, rather than drop-chassis design. But even this has not saved the silencer from impact damage to its leading end. A crack around the inlet pipe is clearly visible here, although there were no audible signs of exhaust blowing.
7 Fulkes says the brake life is very
good on the 3025K, and even on high-mileage vehicles such as this one extra attention is not usually needed outside the annual overhaul. All the brake shoes carry a wear indicator which can be seen through the inspection windows, (covered with a rubber flap) at the top and bottom of each back plate. The indicator is a step on the back of the shoe — when it lines up with the outer edge of the inspection window the linings need replacing. The indicators all showed that, even after 72,000km, the linings on this vehicle needed no attention.
Spring and shackle bushes are checked for wear: they have a hard life on tippers. The offside shackles on the second axle shows some play, but not enough to require attention at this service. The fox clips (pictured) on each spring help to keep the bottom leaves together during spring travel. They are kept tight with a single bolt and need to be checked at each maintenance service. Again they are worked harder on tippers and some need tightening on our vehicle. Fulkes checks the fuel and air tank mountings for tightness at the same time.
The rear brake pressure load sensing valve and linkages need to be checked for free movement and operation. Yet again, these can be vulnerable on tippers used on uneven ground. The valve will prevent premature rear wheel lock-up under braking when empty or lightly loaded. The whole braking system is checked at the same time for leaks and easy operation of the drum assemblies. Rotchell operates the brakes from the cab while Fulkes checks under the vehicle. The rubber mounting for the propshaft centre hearing and the bearing itself are also checked for wear.
10 Restrainers at each end of
the rear axles help contain downward movement over rough ground, when the suspension pivots around the centre bearing. They help to prevent loss of drive to either axle by acting as a bump stop in reverse. The cables are checked for fraying and the shackles at either end for wear. Suspension radius arm bushes are also checked. Fulkes says these should last about two years before replacements are needed: it is possible to drive out worn bearings and press in new ones, so replacement of the arm assembly is not needed.
11 The cab can now be tilted.
Two catches must be re leased, one each side of the cab behind the seats, using the special tool provided. The cab can then be raised using the manual hydraulic pump to give access to all major engine components and fuel, oil and air-filters. The extending gear lever shaft should be greased on both lubrication and maintenance services; high-temperature grease must be used because of the close proximity to the engine. If this is neglected the shaft will dry out and the shift mechanism will stiffen up.
12 A special service tool is used
to turn the engine manually when setting the valve clear ances. The tool is bolted in place after removing an inspection plate in the gearbox bellhousing; timing marks can then be viewed through the inspection window. Two different crankshaft positions are needed to set the valve clearances on this engine. There are two valves per cylinder and the clearances are 0-40mm (0.0161n) inlet and 0-60mm (0.024in) exhaust.
13 The horizontally-mounted
oil-filter body is fitted with a drain plug so in this case the fitter does not get covered in oil when the filter body is released during replacement. The filter and oil should he changed every 10,000km, at every service, when new seals for the filter body and sump drain plug are fitted. Tighten the sump plug to 80Nm and the filter body to 45Nm. Sump capacity is 24 litres and Fulkes uses RX Super semi-synthetic oil. The air drier filter element (shown) is changed once a year. It is located by the battery box on the nearside.
IEI The clutch greasing mecha
nism must be checked at every maintenance service and repacked with grease. The small grease cap can easily be overlooked but it lubricates the clutch release bearing arm and the clutch can become stiff and awkward to operate if this is neglected. The cap is located on the nearside of the gearbox bellhousing and simply needs to be unscrewed, repacked with grease and screwed back on about half-way up the threads. Fulkes uses Olistamoly 2, which is a high-temperature grease for stressed gears and bearings. The 3025K does not have an automatic chassis lubrication system. There are over 30 grease points on the chassis and more on the body. One of the most awkward greasing points to reach is the S-cam on the axles fitted to all Mercedes heavy trucks. For this reason it is often missed in servicing. Oil levels to be checked on the axles include the rear spring centre bearing and the rear axle differentials. These should all be topped up to the filler/level plug at each lubrication and maintenance service, using EP90 oil. Capacities are 11 litres per differential and one litre for each rear spring centre bearing.
16 The clevis pin on each hub
should be greased at each maintenance service. This is part of the self-adjusting brake mechanism and it is important that it is not overlooked. The tipper body on our vehicle has greasing points on the ram, rollers and pivots which are dealt with routinely as part of each lubrication and maintenance service. Obviously this varies from body to body, but a tipper body is as much a working part of the vehicle as the chassis and those not familiar with a tipper body, might overlook these grease points.
th The air filter is under the
front nearside of the cab by the passenger step. This is blown through with a compressed airline at every maintenance service and the filter element is replaced when it has been blown through three times. The filter location again makes it vulnerable to dust on a tipper, but there is an indicator on the dash which warns if the filter has become clogged. Wheel nuts are checked at each lubrication and maintenance service, and should be torqued to 600Nm. Hubreduction-housing oil levels can also be checked and topped up as required. Changing the oil in the hubs is an annual job which involves jacking up each wheel and turning it until the drain plug is at the bottom. Refilling is a slow process because of the viscosity of the EP90 oil. A service tool can be used for this, consisting of a reservoir which can be attached to each hub to drain in the 3.5 litres required.
19 The throttle linkage requires
lubrication at every service as it runs by the engine and tends to dry out with the heat. The linkage from the throttle pedal is exposed under the front of the cab so, once again is vulnerable to dust on vehicles involved in site work. If it is not lubricated it tends to stiffen, making the pedal action heavy, apart from the obvious risk of the throttle eventually sticking open. A light oil such as an aerosol lubricant will solve the problem.
20 The fuel filter and pre-filter,
both replaceable element types, should be changed every maintenance service. The pre-filter assembly is a glass bowl held in place by a knurled wheel located toward the back in the engine vee. The main filter body sits behind it over the clutch housing. If bleeding is required the bleed nut is on top of the main filter casing with the hand primer close by. Spilt fuel from the prefilter needs to be mopped out of the engine Vee as it cannot drain away, and care should be taken not to overtighten the knurled wheel retaining the glass bowl.
21 The power steering reservoir, located over the gearbox, must be checked at every lubrication and maintenance service. It should be dipped with the engine off and topped up with ATF oil if required. The gearbox has a filler and level plug on each side: the nearside is more accessible because of piping along the offside. Our vehicle is fitted with the optional ZF 16S-112CP 16-speed splitter gearbox. Its level should be checked at each lubrication and maintenance service and the EP90 oil should be changed annually. Capacity of the ZF box is 11 litres. 22 All fuses and relays are located behind the dash panel
in front of the driver. This keeps them free from dust and damp, so they are not prone to any particular problems. Finally the lights are checked before the vehicle is road tested. This is carried out by a senior technician, not the fitter who has worked on the vehicle.