Keeping the Wheels Turning
Page 97
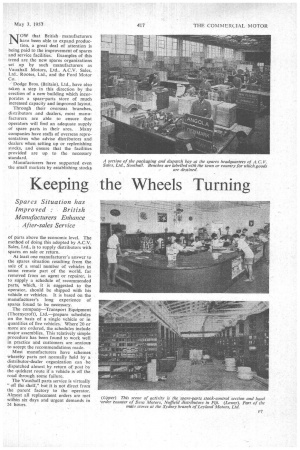
Page 98
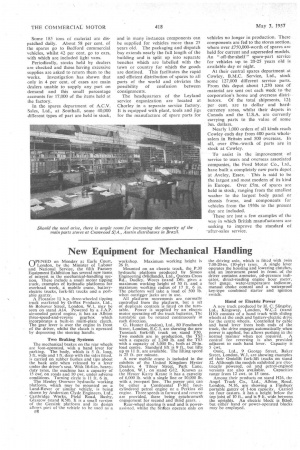
If you've noticed an error in this article please click here to report it so we can fix it.
Spares Situation has Improved : • British Manufacturers Enhance After-sales Service
NOW that British manufacturers have been able to expand production, a great deal of attention is being paid to the improvement of spares and service facilities. Examples of this trend are the new spares organizations set up by such manufacturers as Vauxhall Motors, Ltd., A.C.V. Sales, Ltd.. Rootes, Ltd., and the Ford Motor Co.
Dodge Bros. (Britain), Ltd., have also taken a step in this direction by the erection of a new building which incorporates a spare-parts store of much increased capacity and improved layout.
Through their overseas branches, distributors and dealers, most manufacturers are able to ensure that operators will find an adequate supply of spare parts in their area. Many companies have staffs of overseas representatives who advise distributors and dealers when setting up or replenishing stocks, and ensure that the facilities provided are up to the necessary standard.
Manufacturers have supported even the small markets by establishing stocks of parts above the economic level. The method of doing this adopted by A.C.V. Sales, Ltd., is to supply distributors with spares on sale or return.
At least one manufacturer's answer to the spares situation resulting from the sale of a small number of vehicles in some remote part of the world, far removed from an agent or repairer, is to supply a schedule of recommended parts, which, it is suggested to the operator, should be shipped with his vehicle or vehicles. It is based on the manufacturer's long experience of spares found to be necessary.
The company—Transport Equipment (Thornycroft), Ltd.—prepare schedules on the basis of a single vehicle or in quantities of five vehicles. Where 20or more are ordered, the schedules include major assemblies. This relatively simple procedure has been found to work well in practice and customers are anxious to accept the recommendations made.
Most manufacturers have schemes whereby parts not normally held by a distributor-dealer organization can be dispatched almost by return of post by the quickest route if a vehicle is off the road through some failure.
The Vauxhall parts service is virtually " off the shelf," but it is not direct from the parent factory to the operator. Almost all replacement orders are met within six days and urgent demands in 24 hours. Some 185 tons of material are dispatched daily. About 58 per cent, of the spares go to Bedford commercial vehicles, whilst 42 per cent. go to cars, with which are included light vans.
Periodically, stocks held by dealers are checked and those having excessive supplies are asked to return them to the works. Investigation has shown that only in 4 per cent, of cases are main dealers unable to supply any part on demand and this small percentage accounts for 17,000 of the items held at the factory.
In the spares department of A.C.V. Sales, Ltd., at Southall, some 40,000 different types of part are held in stock, and in many instances components can be supplied for vehicles more than 25 years old, The packaging and dispatch bay extends nearly the full length of the building and is split up into separate benches which are labelled with the town or country for which the goods are destined. This facilitates the rapid and efficient distribution of spares to all parts of the world and obviates the possibility of confusion between consignments.
The headquarters of the Leyland service organization are located at Chorley in a separate service factory. It is equipped with plant, tools and jigs for the manufacture of spare parts for vehicles no longer in production. These components are fed to the stores section, where over 1750,000-worth of spares are held for current and superseded models. An " off-the-shelf " spare-part service for vehicles up to 20-25 years old is available day or night.
At their central spares department at Cowley, B.M.C. Service, Ltd., stock some 127,000 different service parts. From this depot about 1,250 tons of material are sent out each week to the corporation's home and overseas dislri• butors. Of the total shipments, 124 per cent. are to dollar and hardcurrency areas, whilst their depots in Canada and the U.S.A. are currently carrying parts to the value of some 3m. dollars.
Nearly 1,000 orders of all kinds reach Cowley each day from 400 parts wholesalers in Britain and 500 overseas. In all, over 19m.-worth of parts are in stock at Cowley.
To assist in the improvement of service to users and overseas associated companies, the Ford Motor Co., Ltd., have built a completely new parts depot at Aveley, Essex. This is said to be the largest and most modern of its kind in Europe. Over 15m. of spares are held in stock, ranging from the smallest washer to the largest body panel or chassis frame, and components for vehicles from the 1930s to the present day are included.
These are just a few examples of the way in which British manufacturers are seeking to improve the standard of -after-sales service.