Passing Comments
Page 66
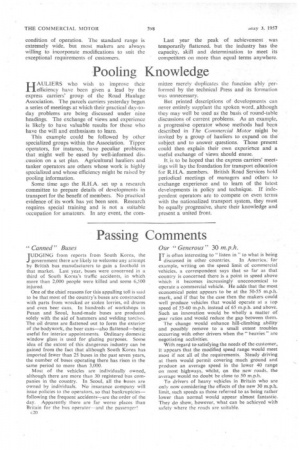
Page 67
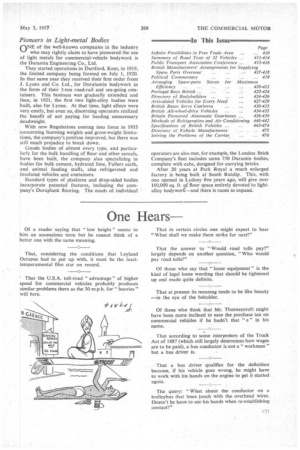
If you've noticed an error in this article please click here to report it so we can fix it.
"Canned" Buses
J UDGING from reports from South Korea, the government there are likely to welcome any attempt by British bus manufacturers to gain a foothold in that market. Last year, buses were concerned in a third of South Korea's traffic accidents, in which more than 2,000 people were killed and some 6,500 injured.
One of the chief reasons for this appalling toll is said to be that most of the country's buses are constructed with parts from wrecked or stolen lorries, oil drums and even beer cans. In hundreds of workshops in Pusan and Seoul, hand-made buses are produced solely with the aid of hammers and welding torches. The oil drums are flattened out to form the exterior of the bodywork, the beer cans—also flattened—being useful for interior appointments. Ordinary domestic window glass is used for glazing purposes. Some idea of the extent of this dangerous industry can be gained from the fact that although South Korea has imported fewer than 25 buses in the past seven years, the number of buses operating there has risen in the same period to more than 3,000.
Most of the vehicles are individually owned, although there are more than 30 registered bus companies in the country. Tn Seoul, all the louses are owned by individuals. No insurance company will issue policies to the operators, so that bankruptcies— following the frequent accidents:—.--are the order of the day. Apparently there are far worse places than Britain for the bus operator—and the passenger!
c20
Our "Generous" 30 m.p.h.
TT is often interesting to "listen in" to what is being I discussed in other countries. In America, for example, writing on the speed limit of commercial vehicles, a correspondent says that so far as that country is concerned there is a point in speed above which it becomes increasingly uneconomical to operate a commercial vehicle. He adds that the most economical point appears to be at the 50-55 m.p.h.. mark, and if that be the case then the makers could well produce vehicles that would operate at a top speed of 55-60 mph. instead of 65 m.p.h and above. Such an innovation would be wholly a matter of gear ratios and would reduce the gap between them.
The change would enhance bill-climbing ability and possibly remove to a small extent troubles occurring with other drivers when the " heavies " are negotiating acclivities: With regard to satisfying the needs of the customer, it appears that the modified speed range would meet most if not all of the requirements. Steady driving at them would permit covering much ground and produce an average speed in the lower 40 range on most highways. whilst, on the new roads, the average would no doubt be close to 50 m.p.h.
To drivers of heavy vehicles in Britain who are only now considering the effects of the new 30 m.p.h. limit, such speeds as those referred to as being rather lower than normal would appear almost fantastic. They do show, however, what can be achieved with safety where the roads are suitable.
Pioneers in Light-metal Bodies
nNE of the well-known companies in the industry who may rightly claim to have pioneered the use of light metals for commercial-vehicle bodywork is the Durarnin Engineering Co., Ltd.
They started operations in Dartford, Kent, in 1919, the limited company being formed on July 1, 1920. In that same year they received their first order from J. Lyons and Co. Ltd., for Duralumin bodywork in the form of their 3-ton road-rail and sea-going containers. This business was gradually extended and then, in 1921, the first two light-alloy bodies were built, also for Lyons. At that time, light alloys were very costly, but even so, discerning operators realized the benefit of not paying for hauling unnecessary deadweight.
With new Regulations coming into force in 1933 concerning licensing weights and gross-weight limitations, the company's position improved, but there was still much prejudice to break down.
Goods bodies of almost every type, and particularly for the bulk handling of flour and other cereals, have been built, the company also specializing in bodies for bulk cement, hydrated lime, Fullers earth, and animal feeding stuffs, also refrigerated and insulated vehicles and containers.
Standard types of platform and drop-sided bodies incorporate patented features, including the company's Duraplank flooring. The needs of individual operators are also met, for example, the London Brick Company's fleet includes some 750 Duramin bodies,complete with cabs, designed for carrying bricks.
After 20 years at Park Royal a much enlarged factory is being built at South Ruislip. This, with one opened in Lydney five years ago, will give over 100,000 sq. ft. of floor space entirely devoted to lightalloy bodywork—and there is room to expand.