KEEP It
Page 124
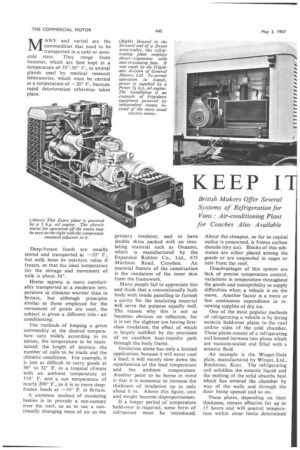
Page 125
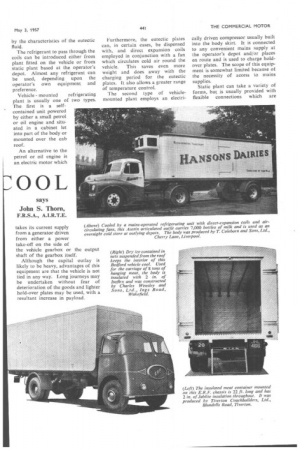
Page 126
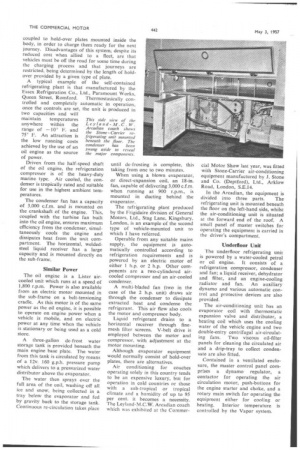
If you've noticed an error in this article please click here to report it so we can fix it.
OOL
says John S. Thorn,
F.R.S.A., A.I.R.T.E.
British Makers Offer Several Systems of Refrigeration for Vans : Air-conditioning Plant for Coaches Also Available
MANY and varied are the commodities that need to be transported in a cold or semicold state. They range from bananas, which are best kept in a temperature of 55°-56° F., to animal glands used by medical research laboratories, which must be carried at a temperature of —20° F., because rapid deterioration otherwise takes place.
Deep-frozen foods are usually stored and transported at —10° F., but milk loses its nutritive value if frozen, so that the ideal temperature for the storage and movement of milk is about 34°.
Homo sapiens is more comfortably transported at a moderate temperature in climates warmer than in Britain, but although principles similar to those employed for the movement of goods are used, the subject is given a different title—air conditioning.
The methods of keeping a given commodity at the desired temperature vary widely according to its nature, the temperature to be maintained, the length of journey, the number of calls to be made and the climatic conditions. For example, it is just as difficult to carry goods at 30° to 32° F. in a tropical climate with an ambient temperature of 110° F. and a sun temperature of nearly 200° F., as it is to move deepfrozen foods at —10° F. in Britain.
A common method of insulating bodies is to provide a sun-canopy over the roof, so as to use a continually changing mass of air as the primary insulator, and to have double skins packed with an insulating material such as Onazote, which is manufactured by the Expanded Rubber Co., Ltd., 675 Mitcham Road, Croydon. An essential feature of the construction is the insulation of the inner skin from the framework.
Many people fail to appreciate this and think that a conventionally built body with inside panelling to furnish a cavity for the insulating material will serve the purpose equally well. The reason why this is not so becomes obvious on reflection, for it is not the slightest use having firstclass insulation, the effect of which is largely nullified by the provision of an excellent heat-transfer path through the body frame.
Insulation alone has only a limited application, because it will never cool a load; it will merely slow down the equalization of the load temperature and the ambient temperature. Another point to be borne in mind is that it is economic to increase the thickness of insulation up to only about 6 in. Above this figure. cost and weight become disproportionate.
If a longer period of temperature hold-over is required, some form of refrigerant must be introduced.
About the cheapest, so far as capital outlay is concerned, is frozen carbon dioxide (dry ice). Blocks of this substance are either placed among the goods or are suspended in cages or nets from the roof.
Disadvantages of this system are lack of precise temperature control, variations in temperature throughout the goods and susceptibility to supply difficulties when a vehicle is on the move. Another factor is a more or less continuous expenditure in renewing supplies of dry ice.
One of the most popular methods of refrigerating a vehicle is by fitting eutectic hold-over plates to the roof and/or sides of the cold chamber. These plates consist of a refrigerating coil housed between two plates which are vacuum-sealed and filled with a eutectic fluid.
An example is the Winget-Dole plate, manufactured by Winget, Ltd., Rochester, Kent. The refrigerating coil solidifies the eutectic liquid and the melting of the solid absorbs heat which has entered the chamber by way of the walls and through the door being opened and so on.
These plates, depending on their thickness, remain effective for up to 15 hours and will control temperature within close limits determined by the characteristics of the eutectic fluid.
The refrigerant to pass through the coils can be introduced either from plant fitted on the vehicle or from static plant based at the operator's depot. Almost any refrigerant can be used, depending upon the operator's own equipment and preference.
Vehicle mounted refrigerating plant is usually one of two types. The first is a selfcontained unit powered by either a small petrol or oil engine and situated in a cabinet let into part of the body or mounted over the cab roof.
An alternative to the petrol or oil engine is an electric motor which takes its current supply from a generator driven from either a power take-off on the side of the vehicle gearbox or the output shaft of the gearbox itself.
Although the capital outlay is likely to be heavy, advantages of this equipment are that the vehicle is not tied in any way. Long journeys may be undertaken without fear of deterioration of the goods and lighter hold-over plates may be used, with a resultant increase in payload. Furthermore, the eutectic plates can, in certain cases, be dispensed with, and direct expansion coils employed in conjunction with a fan which circulates cold air round the vehicle. This saves even more weight and does away with the charging period for the eutectic plates. It also allows a greater range of temperature control.
The second type of vehiclemounted plant employs an electri cally driven compressor usually built into the body skirt. It is connected to any convenient mains supply at the operator's depot and/or places en route and is used to charge holdover plates. The scope of this equipment is somewhat limited because of the necessity of access to mains supplies.
Static plant can take a variety of forms, but is usually provided with flexible connections which are coupled to hold-over plates mounted inside the body, in order to charge them ready for the next journey. Disadvantages of this system, despite its reduced cost when allied to a fleet, are that vehicles must be off the road for some time during the charging process and that journeys are restricted, being determined by the length of holdover provided by a given type of plate.
A typical example of the self-contained refrigerating plant is that manufactured by the Essex Refrigeration Co., Ltd., Paramount Works,
Queen Street. Romford. Thermostatically controlled and completely automatic in operation, once the controls are set, the unit is produced in two capacities and will
maintain temperatures anywhere within the range of —10° F. and 75° F. An attraction is the low running costs achieved by the use of an oil engine as the source of power.
Driven from the half-speed shaft of the oil engine, the refrigeration compressor is of the heavy-duty marine type. Air cooled, the condenser is tropically rated and suitable for use in the highest ambient temperatures.
The condenser fan has a capacity of 3,000 c.f.m. and is mounted on the crankshaft of the engine. This, coupled with the turbine fan built into the oil engine, ensures maximum efficiency from the condenser, simultaneously cools the engine and dissipates heat from the unit compartment. The horizontal, weldedsteel liquid receiver has a large capacity and is mounted directly on the sub-frame.
This side view of the Leyland-M.C.W. Arcadian coach shows the Stone-Carrier refrigerating unit mounted beneath the floor. The condenser has been swung aside to reveal the major components.
Similar Power
The oil engine is a Lister aircooled unit which runs at a speed of 1,800 r.p.m. Power is also available from an electric motor mounted in the sub-frame on a belt-tensioning cradle. As this motor is of the same power as the oil engine, it is possible to operate on engine power when a vehicle is mobile, and on electric power at any time when the vehicle is stationary or being used as a cold store.
A three-gallon de-frost water storage tank is provided beneath the main engine base plate. The water from this tank is circulated by means of a 12v. 160 g.p.h. pressure pump which delivers to a pressurized water distributor above the evaporator.
The water then sprays over the full area of the coil, washing off all ice and snow, being collected in a tray below the evaporator and fed by gravity back to the storage tank. Continuous re-circulation takes place until de-frosting is complete, this taking from one to two minutes.
When using a blown evaporator, or direct-expansion coil, an 18-in. fan, capable of delivering 3,000 c.f.m. when running at 900 r.p.m., is mounted in ducting behind the evaporator.
The refrigerating plant produced by the Frigidaire division of General Motors, Ltd., Stag Lane, Kingsbury, London, is an example of the second type of vehicle-mounted unit to which I have referred.
Operable from any suitable mains supply, the equipment is automatically controlled according to refrigeration requirements and is powered by an electric motor of either 1 h.p. or 2 h.p. Other components are a two-cylindered aircooled compressor and an air-cooled condenser.
A multi-bladed fan (two in the case of the 2 h.p. unit) draws air through the condenser to dissipate extracted heat and condense the refrigerant. This air flow also cools the motor and compressor body.
Liquid refrigerant drains to a horizontal receiver through finemesh filter screens. V-belt drive is employed between the motor and compressor, with adjustment at the motor mounting.
Although evaporator equipment would normally consist of hold-over plates, there are alternatives.
Air conditioning for coaches operating solely in this country tends to be an expensive luxury, but for operation in cold countries or those with a sub-tropical or tropical climate and a humidity of up to 95 per cent, it becomes a necessity. The Leyland-M.C.W. Arcadian coach which was exhibited at the Commer cial Motor Show last year, was fitted with Stone-Carrier air-conditioning equipment manufactured by J. Stone and Co. (Deptford), Ltd., Arklow Road, London, S.E.14.
In the Arcadian, the equipment is
divided into three parts. The refrigerating unit is mounted beneath the floor on the left-hand side, whilst the air-conditioning unit is situated at the forward end of the roof. A small panel of master switches for Operating the equipment is carried in the driver's compartment.
Underfloor Unit
The underfloor refrigerating unit is powered by a water-cooled petrol or oil engine. It consists of a refrigeration compressor, condenser and fan; a liquid receiver, dehydrator and filter, and an engine-cooling radiator and fan. An auxiliary dynamo and various automatic control and protective devices are also provided.
The air-conditioning unit has an evaporator coil with thermostatic expansion valve and distributor, a heating coil which uses the cooling water of the vehicle engine and two double-entry centrifugal air-circulating fans. Two viscous oil-filter panels for cleaning the circulated air and a drip-tray to collect condensate are also fitted.
Contained in a ventilated enclosure, the master control panel comprises a dynamo regulator, a contactor for operating the air circulation motor, push-buttons for the engine starter and choke, and a rotary main switch for operating the equipment either for cooling or heating. Interior temperature is controlled by the Vapor system.