New Tubular Seat Construction
Page 38
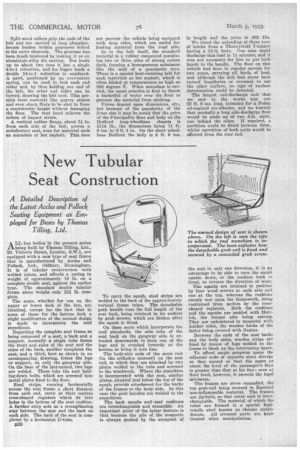
If you've noticed an error in this article please click here to report it so we can fix it.
A Detailed Description of the Latest Accles and Pollock Seating Equipment as Employed for Buses by Thomas
Tilling, Ltd.
ALL bus bodies in the present series being built by Thomas Tilling, Ltd., 20, Victoria Street, London, S.W.1, are equipped with a new type of seat frame that is manufactured by Accles and Pollock, Ltd., Oldbury, Birmingham. It is of tubular construction with welded joints, and affords a saving in weight of approximately 18 lb. on a complete double seat, against the earlier type. The standard double tubular frame alone weighs only 12* lb. complete.
The seats, whether for use on the upper or lower deck of the bus, are identical, except for the fact that in some of those for the bottom deck a slight modification of the normal design is made to incorporate the roof stanchions.
Regarding the complete seat frame as being composed of a seat, a back and a support, normally a single tube forms the front and sides of the seat and the sides of the back, another completes the seat, and a third, bent as shown in an accompanying drawing, forms the legs or support, on only the gangway side. On the base of the last-named, two lugs are welded. These take the seat holding-down bolts, which are screwed into metal plates fixed to the floor.
Steel strips, running horizontally across the seat frame a short distance from each end, carry at their centres cone-shaped registers 'which fit into holes in the bottom of the seat cushion. A further strip acts as a strengthening stay* between the seat and the back on each aide. The back of the seat is completed by a horizontal D-tube. To carry the squab, steel strips are welded to the back of the approximately vertical frame tubes. The detachable grab handle runs the full length of the seat back, being retained in its sockets by grub screws, which are hidden after the squab is fitted.
On those seats which incorporate the roof standards, the side tube of the seat back on the gangway side is extended downwards to form one of the legs and is cranked inwards at the bottom to bring it into line.
The body-side ends of the seats rest (in the orthodox manner) on the seat rail, to which they are attached by two plates welded to the tube and screwed to the woodwork. Where the stanchion is incorporated with the seat, similar plates, situated just below the top of the squab, provide attachment for the backs of the frames to the body side. in this case the grab handles are welded to the stanchions.
The back squabs and' seat cushions are interchangeable and reversible. An important point of the latter feature is that because the pile of the moquette is always pushed by the occupant of
the seat in only one direction, it is an advantage to be able to turn the squab upside down, or the cushion back to front, to reverse the direction of wear.
The squabs are retained in position by four wood screws at each side and one at the top, whereas the cushions simply rest upon the framework, being restrained from motion by the coneshaped registers. Both the cushions and the squabs are padded with Hairlok, the former also being sprung. They are upholstered in moquette with leather sides, the wooden backs of the latter being covered with Rexine.
Between the ends of the seat backs and the body sides, wooden strips are fixed by means of lugs welded to the frame to block up the intervening space.
To afford ample gangway space the adjacent ends of opposite seats diverge ' as they ascend so that the space at about the level of the passenger's hips is greater than that at his feet; even at floor level, however, it exceeds the legal minimum.
The frames are stove enamelled, the top grab-rail being covered in Excelohl non-inflammable material. The frames are jig-built, so that every unit is interchangeable. The material of which the tubes are formed is a special hightensile steel known as chrome molybdenum. All stressed parts are heattreated after manipulation,