Largest Lorry Moves Heaviest Load Ever
Page 38
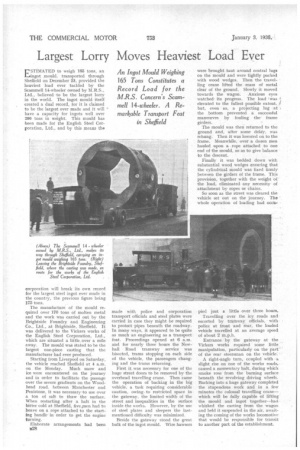
If you've noticed an error in this article please click here to report it so we can fix it.
An Ingot Mould Weighing 165 Tons Constitutes a Record Load for the M.R.S. Concern's Scammell 14-wheeler. A Remarkable Transport Feat
in Sheffield
ESTIMATED to weigh 105 tons, an ingot mould transported through Sheffield on December 23, provided the heaviest load ever tackled by the Scammell 14-wheeler owned by MRS., Ltd., believed to be the largest lorry in the world. The ingot mould• itself created a dual record, for it is claimed to be the largest ever made and it will have a capacity for ingots well over 200 tons in weight. This mould has been made for the English Steel Corporation, Ltd., and by this means the
corporation will break its own record for the largest steel ingot ever made in the country, the previous figure being 175 tons, The manufacture of the mould required over 170 tons of molten metal and the work was carried out by the Brightside Foundry and Engineering Co., Ltd., at•13rightside, Sheffield. It was delivered to the Vickers works of the English Steel Corporation, Ltd., which are situated a little over a mile away. The mould was stated to be the largest one-piece casting that the manufacturer had ever produced.
Starting from Liverpool on Saturday, the vehicle reached Sheffield at 4 a.m. on the Monday. Much snow and ice were encountered on the journey and in order to facilitate the passage over the severe gradients on the Woodhead road. between Manchester and Penistone, it was necessary-to use over a ton of salt to thaw the surface. When restarting after a halt in the bitter cold at Sheffield, five .men had to heave on a rope attached to the starting handle in order to get the engine turning.
Elaborate arrangements had been B28 made with police and corporation transport officials and steel plates were carried in case they might be required to protect pipes beneath the roadway. In many ways, it appeared to be quite as much an engineering as a transport feat. Proceedings opened at 6 a.m. and for nearly three hours the Newhall Road tramway service was bisected, trams stopping on each side of the vehicle, the passengers changing and the trams returning.
First it was necessary for one of the huge street doors to be removed by the overhead travelling crane. Then came the operation of backing in the big vehicle, a task requiring considerable caution, owing to restricted space in the gateway, the limited width of the street and inequalities in the surface inside the works. However, by the use of steel plates and sleepers the lastmentioned difficulty was minimized.
Beside the gateway stood the great bulk of the ingot mould. Wire hawsers
were brought taut around central lugs on the mould and were tightly packed with wood wedges. Then the travelling crane lifted the mass of metal clear of the ground. Slowly it moved towards the wagon. Anxious eyes watched its progress. The load was elevated to the fullest possible extent. but, even so, a projecting lug at the bottom prevented a successful manieuvre. by fouling the frame girders.
The mould was then returned to the ground •and, after some delay, was rehung. Then it was lowered on to the frame. Meanwhile, over a dozen men hauled upon a rope attached to one end of the mould, so as to give balance to the descent. • Finally it was bedded down with substantial wood wedges ensuring that the cylindrical mould was fixed firmly between the girders of the frame. This provision, together with the weight of • the load, eliminated any necessity of attachment by ropes or chains.
So soon as the street was cleared the vehicle set out on the journey. Theowhole operation of loading had occti-.
pied just a little over three hours.
Travelling over the icy roads and escorted by tramway officials, with police at front and rear, the loaded vehicle travelled at an average speed of about 2 m.p.h.
Entrance by the gateway at the Vickers works required some little manipulation, particularly on the part of the rear steersman on the vehicle.
A right-angle turn, ccupled with a slight rise on one of the works roads, caused a momentary halt, during which smoke rose from the burning surface beneath the revolving driving wheels. Backing into a huge gateway completed the stupendous work and in a few minutes the colossal travelling crane— which will be fully capable of lifting the mould and ingot together—had. whisked the casting from the wagon and held it suspended in the air, awaiting the coming of the works locomotive that would be responsible for transit to another part of the establishment.