Denniss plans Euro bar code
Page 35
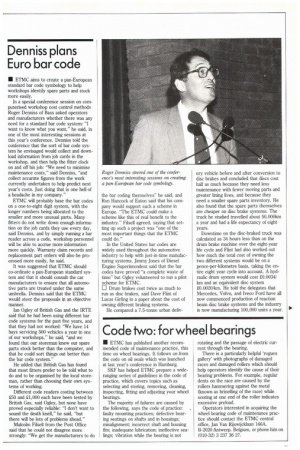
If you've noticed an error in this article please click here to report it so we can fix it.
• ETMC aims to create a pan-European standard bar code symbology to help workshops identify spare parts and stock more easily.
In a special conference session on computerised workshop cost control methods Roger Denniss of Bass asked operators and manufacturers whether there was any need for a standard bar code system: "1 want to know what you want," he said, in one of the most interesting sessions at this year's conference. Denniss told the conference that the sort of bar code system he envisaged would collect and download information from jab cards in the workshop, and then help the fitter clock on and off his job: "We need to minimise maintenance costs," said Denniss, "and collect accurate figures from the work currently undertaken to help predict next year's costs. Just doing that is one hell of a headache in my company."
ETMC will probably base the bar codes on a one-to-eight digit system, with the longer numbers being allocated to the smaller and more unusual parts. Many fitters do not write down enough information on the job cards they use every day, said Denniss, and by simply running a bar reader across a code, workshop personnel will be able to accrue more information more quickly. Warranty claim records and replacement part orders will also be processed more easily, he said.
It was suggested that ETMC should co-ordinate a pan-European standard system and that it should consult the car manufacturers to ensure that all automotive parts are treated under the same umbrella. Denniss said that the ETMC would steer the proposals in an objective manner.
Ian Ogley of British Gas and the IRTE said that he had been using different bar code systems for the past five years, and that they had not worked: "We have 14 bays servicing 500 vehicles a year in one of our workshops," he said, "and we found that our storeman knew our spare parts stock better than the computer, and that he could sort things out better than the bar code system."
He added that British Gas has found that most fitters prefer to be told what to do and to be organised by the local storeman, rather than choosing their own systems of working.
Different code readers costing between £50 and 21,000 each have been tested by British Gas, said Ogley, but none have proved especially reliable: "I don't want to sound the death knell," he said, "but there will be lots of problems ahead."
Malcolm Filsell from the Post Office said that he could not disagree more strongly: "We get the manufacturers to do the bar coding themselves" he said, and Ron Hancock of Eaton said that his company would support such a scheme in Europe. "The ETMC could make a scheme like this of real benefit to the industry." Filsell agreed, saying that setting up such a project was "one of the most important things that the ETMC could do."
In the United States bar codes are widely used throughout the automotive industry to help with just-in-time manufacturing systems. Jimmy Jones of Diesel Engine Superintendent said that the bar codes have proved "a complete waste of time" but Ogley volunteered to run a pilot scheme for ETMC.
ED Drum brakes cost twice as much to run as disc brakes, said Dave Flint of Lucas Girling in a paper about the cost of owning different braking systems.
He compared a 7.5-tonne urban deliv ery vehicle before and after conversion to disc brakes and concluded that discs cost half as much because they need less maintenance with fewer moving parts and greater lining lives, and because they need a smaller spare parts inventory. He also found that the spare parts themselves are cheaper on disc brake systems. The truck he studied travelled about 50,000km a year and had a life expectancy of eight years.
Downtime on the disc-braked truck was calculated as 34 hours less than on the drum brake machine over the eight-year life cycle and Flint had also worked out how much the total cost of owning the two different systems would be on a pence-per-kilometre basis, taking the entire eight year cycle into account. A hydraulic drum system would cost £0.0034/ km and an equivalent disc system £0.0020/kna. He told the delegates that Mercedes, Volvo, and Iveco Ford have all now commenced production of reaction beam disc brake systems and the industry is now manufacturing 100,000 units a year.