Testing in Turin and inking of tomorrow
Page 36
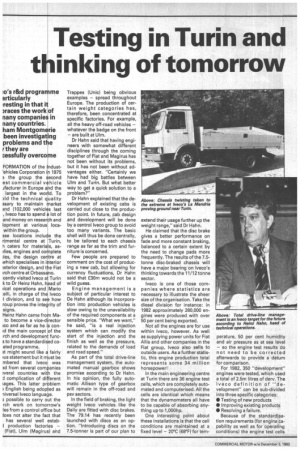
Page 37
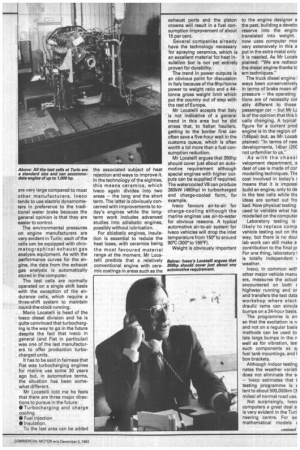
Page 38
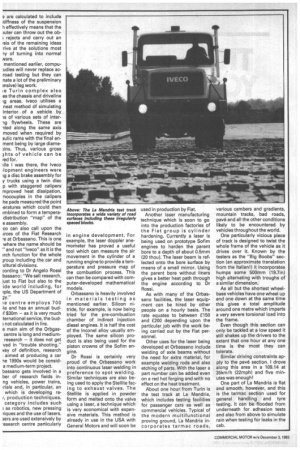
If you've noticed an error in this article please click here to report it so we can fix it.
:o's r&d programme articularly resting in that it races the work of nany companies in nany countries. ham Montgornerie been investigating problems and the r they are Dessfully overcome
FORMATION of the ndust'ehicles Corporation in 1975 a the group the second est commercial vehicle Jfacturer in Europe and the largest in the world. To )Id the technical quality ssary to maintain inarket and (102,000 vehicl s last , Iveco has to spend lot of and money on resear h and lopment at various locawithin the group.
3se locations inclu e the rimental centre at Turin, 1 caters for materia s, asflies, engines and co plete :les, the design ce tre at which specialises in 1 terior axterior design, and tie Fiat irch centre at Orbass no. cently visited Iveco at Turin k to Dr Heinz Hahn, head of iical operations and Mario :elli, in charge of the Iveco I division, and to see how roup proves the integrity of signs.
Heinz Hahn came fro)n Mato become a vice-d rector 3co and as far as he i con:d the main concept f the rch and development func s to have a standardi ed coated programme.
at might sound like fairly
■ us statement but it rrust be II)
mbered that Iveco was ad from several com anies )veral countries with the I complication of different iages. This latter problem ) English being adopted as iiversal Iveco language.
3 possible to carry out the rch work on tomorrow's les from a control office but Ioes not alter the fact that has several well estabi production factories — (Fiat), Ulm (Magirus) and
Trappes (Unic) being obvious examples — spread throughout Europe. The production of certain weight categories has, therefore, been concentrated at specific factories. For example, all the heavy off-road vehicles — whatever the badge on the front — are built at Ulm.
Dr Hahn said that having engineers with somewhat different disciplines through the coming together of Fiat and Magirus has not been without its problems, but it has not been without advantages either. "Certainly we have had big battles between Ulm and Turin. But what better way to get a quick solution to a problem?"
Dr Hahn explained that the development of existing cabs is carried out close to the production point. In future, cab design and development will be done by a centrol Iveco group to avoid too many variants. The basic shell will thus be done centrally, to be tailored to each chassis range as far as the trim and furniture is concerned.
Few people are prepared to comment on the cost of producing a new cab, but allowing for currency fluctuations, Dr Hahn said that £30m would not be a wild guess.
Engine management is a subject of particular interest to De Hahn although its incorporation into production vehicles is slow owing to the unavailability of the required components at a sensible price. "What we want," he said, "is a real injection system which can modify the start of the injection and the finish as well as the pressure, related to the demands of load and road speed."
As part of the total drive-line management system, the automated manual gearbox shows promise according to Dr Hahn. In his opinion, the fully automatic Allison type of gearbox will remain in the off-road and psv sectors.
In the field of braking, the light weight Iveco vehicles like the Daily are fitted with disc brakes. The 79.14 has recently been launched with discs as an option. "Introducing discs on the 7.5-tanner is part of our plan to extend their usage further up the weight range," said Dr Hahn.
He claimed that the disc brake gives a better performance on fade and more constant braking, balanced to a certain extent by the need to change pads more frequently. The results of the 7.5tonne disc-braked chassis will have a major bearing on Iveco's thinking towards the 11/12 tonne sector.
Iveco is one of those cornpan es where statistics are necessary to illustrate the sheer size of the organisation. Take the diesel division for instance: in 1982 approximately 280,000 engines were produced with over 50 per cent being exported.
Not all the engines are for use within Iveco, however. As well as supplying power units for Fiat Allis and other companies in the Fiat group, Iveco also sells to outside users. As a further statistic, this engine production total represents some 34 million horsepower!
In the main engineering centre at Turin there are 36 engine test cells, which are completely automated and computerised. All the cells are identical which means that the dynamometers all have to be capable of absorbing anything up to 1,000hp.
One interesting point about these installations is that the cell conditions are maintained at a fixed level — 20°C (68°F) for tern perature, 50 per cent humidity and air pressure as at sea level — so the engine test results do not need to be corrected afterwards to provide a datum for comparison.
For 1982, 350 "development" engines were tested, which used a total of 2.5m litres of derv. The Iveco definition of "development" can be sub-divided into three specific categories: • Testing of new products • Improving existing products • Resolving a failure.
Because of the standardisation requirements (for engine capability as well as for operating conditions) the engine test cells are very large compared to most other manufacturers. Iveco tends to use electric dynamometers in preference to the traditional water brake because the general opinion is that they are easier to control.
The environmental pressures on engine manufacturers are very evident in Turin; each of the cells can be equipped with chromatographical exhaust gas analysis equipment. As with the performance curves for the engine, the data from the exhaust gas analysis is automatically stored in the computer.
The test cells are normally operated on a single shift basis with the exception of the endurance cells, which require a three-shift system to maintain round-the-clock running.
Mario Locatelli is head of the Iveco diesel division and he is quite convinced that tu rbocharging is the way to go in the future despite the fact that Iveco in general (and Fiat in particular) was one of the last manufacturers to offer production turbocharged units.
It haste be said in fairness that Fiat was turbocharging engines for marine use some 30 years ago but, in automotive terms, the situation has been somewhat different.
Mr Locatelli told me he feels that there are three major directions to pursue in the future: • Turbocharging and charge cooling • Fuel injection • Insulation.
To the last area can be added the associated subject of heat rejection and ways to improve it. In the technology of the eighties, this means ceramics, which Iveco again divides into two areas — the long and the short term. The latter is obviously concerned with improvements to today's engines while the longterm work includes advanced studies into adiabatic engines, possibly without lubrication.
For abiabatic engines, insulation is essential to reduce the heat loses, with ceramics being the most favoured material range at the moment. Mr Locatelli predicts that a relatively conventional engine with ceramic coatings in areas such as the exhaust ports and the piston crowns will result in a fuel consumption improvement of about 15 per cent.
Several companies already have the technology necessary for spraying ceramics, which is an excellent material for heat insulation but is not yet entirely proven for durability.
The trend in power outputs is an obvious point for discussion in Italy because of the 8hp/tonne power to weight ratio and a 44tonne gross weight limit which put the country out of step with the rest of Europe.
Mr Locatelli accepts that Italy is not indicative of a general trend in this area but he did stress that, to Italian hauliers, getting to the border first can often save a five-hour wait in the customs queue, which is often worth a lot more than a fuel consumption reduction.
Mr Locatelli argues that 350hp should cover just about an automotive requirement although special engines with higher outputs can be supplied if required. The watercooled V8 can produce 360kW (480hp) in turbocharged and charge-cooled form, for example.
Iveco favours air-to-air for charge-cooling although the marine engines use air-to-water for obvious reasons. A typical automotive air-to-air system for Iveco vehicles will drop the inlet temperature from 150° to around 90°C (300° to 195°F).
Weight is obviously important to the engine designer a the past, building a develoi reserve into the engin( translated into weight. now uses computer moc very extensively in this a put in the extra metal only it is needed. As Mr LocatE plained: "We are redisca the diesel engine thanks tc ern techniques."
The truck diesel engine I ways been conservatively in terms of brake mean et pressure — the operating tions are of necessity cor ably different to those passenger car — but Mr Lc is of the opinion that this h ually changing. A typical figure for a current prod engine is in the region of (145psi) but, as Mr Locatt plained: "In terms of nev% developments, 14bar (20C not unfamiliar to us."
As with the chassi velopment department, 'a deal of use is made of car modelling techniques. The cost involved in today's r means that it is impossi build an engine, only to de in the test cells while the ideas are sorted out fro bad. Now physical testing used to validate what ha: modelled on the computer Laboratory testing is likely to replace comp vehicle testing out on thE way, but there is no doul lab work can still make a contribution to the final pr For one thing, laboratory 1 is totally independent ( weather, Iveco, in common with other major vehicle menu ers, measures the actual encountered on both r highway running and or and transfers the test data workshop where elect' draulic rams can simula bumps on a 24-hour basis.
The programme is arr so that the excitation is rc and not on a regular basis methods can be used to late large bumps in the ri well as for vibration, tesi such components as si fuel tank mountings, and box brackets.
Although indoor testing nates the weather variati does not eliminate the si — Iveco estimates that t testing programme is E lent to about 500,000km (3 miles) of normal road use.
Not surprisingly, Ivecc computers a great deal a is very evident in the Turi neering centre. For ex mathematical models r a are calculated to include Jtiffness of the suspension h effectively means that the )uter can throw out the ob; rejects and carry out an rsis of the remaining ideas rive at the solutions most ly of turning into normal Na re.
mentioned earlier, compuudies will never replace acroad testing but they can nate a lot of the preliminary )nsive) leg work.
re Turin complex also es the chassis and driveline lg areas. Iveco utilises a neat method of simulating interior of a vehicle by Is of various sets of interig flywheels. These are ited along the same axis moved when required by aulic rams with the final enment being by large diame)ins. Thus, various gross ]hts of vehicle can be fed for.
ile I was there, the Iveco 1opment engineers were ig a disc brake assembly for y trucks using a twin disc p with staggered calipers mproved heat dissipation. -nocouples in the calipers he pads measured the point leratures which could then ;mbined to form a temperadistribution "map" of the e assembly.
co can also call upon the Jrces of the Fiat Research -e at Orbassano. This is one where the name should be "and not "Iveco" as it is the irch function for the whole jroup including the car and u ltu ra I divisions.
cording to Dr Angelo Rossi bassano: "We sell research. just to Fiat but also to the ide world including, for Iple, the US Department of le centre employs 700 le and has an annual bud$30m — as it is very much ternational service, the bud; not calculated in lire.
e main aim of the Orbgascentre is long and mediumresearch — it does not get ved in "trouble shooting." vay of definition, research aimed at producing a car le 1990s would be consida medium-term project.
bassano gets involved in a ber of research fields inng vehicles, power trains, Jrials and, in particular, an which is developing rar, production techniques. category includes such ; as robotics, new pressing liques and the use of lasers. 3ers are used extensively by .esearch centre particularly
in engine development. For example, the laser doppler anemometer has proved a useful tool which can measure the air movement in the cylinder of a running engine to provide a temperature and pressure map of the combustion process. This can then be compared with computer-developed mathematical models.
Orbassano is heavily involved in materials testing as mentioned earlier. Silicon nitride, for example, is now being tried for the pre-combustion chamber of indirect injection diesel engines. It is half the cost of the Inconel alloy usually employed. The same silicon product is also being used for the piston crowns Of the Sofim engine.
Dr Rossi is certainly very proud of the Orbassano work into continuous laser welding in preference to spot welding. Similar techniques are also being used to apply the Stellite facing to exhaust valves. The Stellite is applied in powder form and melted onto the valve using a laser, a technique which is very economical with expensive materials. This method is already in use in the USA with General Motors and will soon be used in production by Fiat.
Another laser manufacturing technique which is soon to go into the production factories of the Fiat group is cylinder hardening. Currently a laser is being used on prototype Sofim engines to harden the parent bore to a depth of about 0.5mm (20 thou). The laser beam is reflected onto the bore surface by means of a small mirror. Using the parent bore without liners gives a better heat path through the engine according to Dr Rossi.
As with many of the Orbassano facilities, the laser equipment can be hired by other people on a hourly basis. The rate equates to between £150 and £200 depending upon the particular job with the work being carried out by the Fiat personnel.
Other uses for the laser being developed at Orbassano include welding of axle beams without the need for extra material, for example welding rods and also etching of parts. With the laser a part number can be added even on a red hot forging and with no effect on the heat treatment.
About one hour from Turin is the test track at La Mandria, which includes testing facilities for passenger cars as well as commercial vehicles. Typical of the modern multifunctional proving ground, La Mandria incorporates tarmac roads, various cambers and gradients, mountain tracks, bad roads, pave and all the other conditions likely to be encountered by vehicles throughout the world.
One particularly vicious piece of track is designed to twist the whole frame of the vehicle as it drives over it. Known by the testers as the "Big Boobs" section (an approximate translation from the Italian!) it incorporates humps some 500mm (19.71n) high alternating with troughs of a similar dimension.
As all but the shortest wheelbase vehicles have one wheel Up and one down at the same time this gives a total amplitude around one metre which imparts a very severe torsional load into the frame.
Even though this section can only be tackled at a low speed it still shakes up the drivers to the extent that one hour at any one time is the most they can tolerate.
Similar driving constraints apply to the pave section. I drove along this area in a 109.14 at 35km/h (22mph) and five minutes was enough!
One part of La Mandria is flat and smooth, however, and this is the tarmac section used for general handling and tyre testing. It can be flooded from underneath for adhesion tests and also from above to simulate rain when testing for leaks in the cab.