DEMOUNTABLE
Page 74
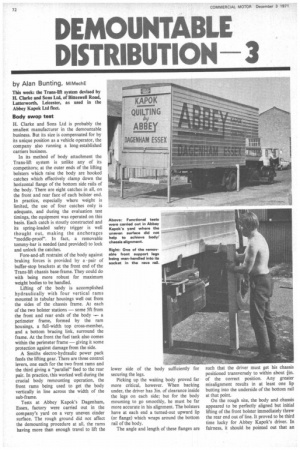
Page 75

If you've noticed an error in this article please click here to report it so we can fix it.
DISTRIBUTION-3 by Alan Bunting, MIMechE This week: the Trans-lift system devised by H. Clarke and Sons Ltd, of Bitteswell Road, Lutterworth, Leicester, as used in the Abbey Kapok Ltd fleet.
Body swop test
H. Clarke and Sons Ltd is probably the smallest manufacturer in the demountable business. But its size is compensated for by its unique position as a vehicle operator, the company also running a long-established carriers business.
In its method of body attachment the Trans-lift system is unlike any of its competitors; at the outer ends of the lifting bolsters which raise the body are hooked catches which effectively clamp down the horizontal flange of the bottom side rails of the body. There are eight catches in all, on the front and rear face of each bolster end. In practice, especially where weight is limited, the use of four catches only is adequate, and during the evaluation test timings, the equipment was operated on this basis. Each catch is stoutly constructed and its spring-loaded safety trigger is well thought out, making the anchorages "meddle-proof'. In fact, a removable tommy-bar is needed (and provided) to lock and unlock the catches.
Fore-and-aft restraint of the body against braking forces is provided by a pair of buffer-stop brackets at the front end of the Trans-lift chassis base-frame. They could do with being more robust for maximum weight bodies to be handled.
Lifting of the body is accomplished hydraulically with four vertical rams mounted in tubular housings well out from the sides of the chassis frame. At each of the two bolster stations — some 5ft from the front and rear ends of the body -a perimeter frame, formed by the ram housings, a full-width top cross-member, and a bottom bracing link, surround the frame. At the front the fuel tank also comes within the perimeter frame — giving it some protection against damage from the side.
A Smiths electro-hydraulic power pack feeds the lifting gear. There are three control levers, one each for the two front rams and the third giving a "parallel" feed to the rear pair. In practice, this worked well during the crucial body remounting operation, the front rams being used to get the body vertically in line across the width of the sub-frame.
Tests at Abbey Kapok's Dagenham, Essex, factory were carried out in the company's yard on a very uneven cinder surface. The rough ground did not affect the demounting procedure at all, the rams having more than enough travel to lift the lower side of the body sufficiently for securing the legs.
Picking up the waiting body proved far more critical, however. When backing under, the driver has 3in. of clearance inside the legs on each side; but for the body mounting to go smoothly, he must be far more accurate in his alignment. The bolsters have at each end a turned-out upward lip (or flange) which wraps around the bottom rail of the body.
The angle and length of these flanges are such that the driver must get his chassis positioned transversely to within about fin. of the correct position. Any greater misalignment results in at least one lip butting into the underside of the bottom rail at that point.
On the rough site, the body and chassis appeared to be perfectly aligned but initial lifting of the front bolster immediately threw the rear end out of line. It proved to be third time lucky for Abbey Kapok's driver. In fairness, it should be pointed out that an experienced driver picking up a Trans-lift body on level hard-standing should have no difficulty.
On the Clarke equipment, the rear legs are telescopic with locking pins for the raised and lowered positions. They are rather ingeniously incorporated in the combined underrun bumper and rear door frame. The front legs are removable. In use, they locate in square sockets in the floor structure. On the road each one is carried in a pair of saddle brackets on the side of the chassis. With the body lowered they cannot be removed by pilferers. The legs can be manhandled readily; a check showed the weight of one to be 421b.
The Abbey Kapok chassis on which our evaluation was made, was a Bedford KDLC5. With its Clarke base unit, its taxation weight was 3 tons 7cwt. The company's alloy fixed-bodied vans on the same chassis weigh about 3 tons 15cwt for taxation purposes. Clarke builds the bodywork as well as the demountable "hardware" for its equipment. The 1850 cu ft Luton body on the Bedford had a 21ft-long floor.
It was unfortunate from the point of view of achieving representative functional test results that for Abbey Kapok a full load — to the roof — weighs only 18cwt. A fully laden body was used but the times recorded must inevitably be judged bearing the low payload figure in mind. The body was parked, with the base vehicle ready to drive away, in just 4min. Once it had been established (as already described) that the body and chassis were adequately aligned, the remounting operation was achieved in 2min 50sec. Abbey's transport manager, Mr Mick Buck, reckons on an 8 to 9min minimum turnround time when necessary.
Service experience Abbey Kapok is involved in the delivery of finished Kapok and quilting as well as soft furnishing materials. It also collects raw material in the form of rolls of wadding, involving runs to a collection point at Carlisle and, from time to time, to Glasgow.
Before the Trans-lift equipment was acquired, when a loaded vehicle due back from, say, Carlisle late in the day was scheduled for another long haul the following day, two labourers had to wait until it arrived, to unload and reload. On such long hauls arrival timing is unpredictable, and it was found that much of the overtime wages bill could be attributed to waiting time.
Now a Trans-lift body can be loaded during the day ready for the next day's run. At present mixed loads of Kapok and quilting present a problem in that they are loaded at opposite ends of the factory, and the parked body is, of course. immobilized. But it is hoped to have a "slave" chassis for manoeuvring short distances, in due course.
Mr Buck's only complaint about the equipment: rainwater tends to collect in the rear support legs. He likes the simplicity of the system, however, and the readiness of Clarke to meet individual requirements.
Next week the Rol!along gantry from Rollalong Ltd