Road Test of Forc 1)750 Tipper
Page 82
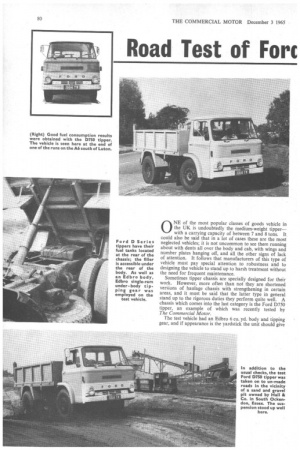
Page 83
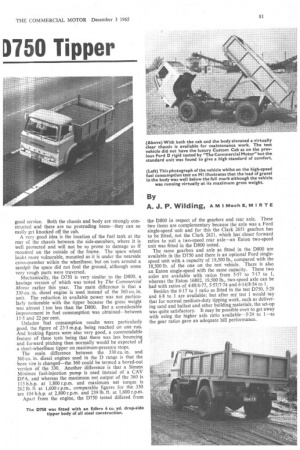
Page 84
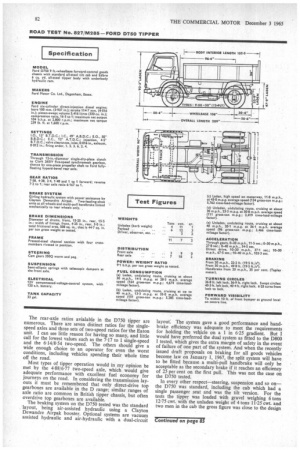
Page 87
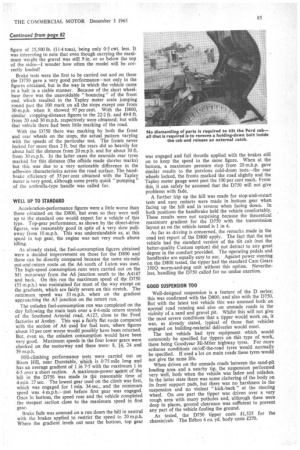
If you've noticed an error in this article please click here to report it so we can fix it.
By
A. J. P. Wilding, AMIIViechE,MIRTE 0 NE of the most popular classes of goods vehicle in the UK is undoubtedly the medium-weight tipper— with a carrying capacity of between 7 and 8 tons. It could also be said that in a lot of cases these are the most neglected vehicles; it is not uncommon to see them running about with dents all over the body and cab, with wings and number plates hanging off, and all the other signs of lack of attention. It follows that manufacturers of this type of vehicle must pay special attention to robustness and to designing the vehicle to stand up to harsh treatment without the need for frequent maintenance.
Sometimes tipper chassis are specially designed for their work. However, more often than not they are shortened versions of haulage chassis with strengthening in certain areas, and it must be said that the latter type in general stand up to the rigorous duties they perform quite well. A chassis which comes into the last category is the Ford D750 tipper, an example of which was recently tested by The Commercial Motor.
The test vehicle had an Edbro 6 cu. yd. body and tipping gear, and if appearance is the yardstick the unit should give good service. Both the chassis and body are strongly constructed and there are no protruding items—they can so easily get knocked off the cab.
A very good idea is the location of the fuel tank at the rear of the chassis between the side-members, where it is well protected and will not be so prone to damage as if mounted on the outside of the frame. The spare wheel looks more vulnerable, mounted as it is under the nearside cross-member within the wheelbase; but on tests around a sandpit the spare did not foul the ground, although some very rough parts were traversed.
Mechanically, the D750 is very similar to the D800, a haulage version of which was tested by The Commercial Motor earlier this year. The main difference is that a 330 Cu. in. diesel engine is used instead of the 360 cu. in. unit. The reduction in available power was not particularly noticeable with the tipper because the gross weight was almost 1 ton less than the D800. But a considerable improvement in fuel consumption was obtained—between 11.5 and 22 per cent.
Unladen fuel consumption results were particularly good, the figure of 23.3 m.p.g. being reached on one run. And braking figures were also very good, a commendable feature of these tests being that there was less bouncing and forward pitching than normally would be expected of a short-wheelbase tipper on maximum-pressure stops.
The main difference between the 330 Cu. in. and 360 cu. in, diesel engines used in the D range is that the bore size is changed—the 360 could be termed a bored-out version of the 330. Another difference is that a Simms Minimec fuel-injection pump is used instead of a CAV DPA, and whereas the maximum net output of the 360 is 113 b.h.p. at 1,800 r.p.m. and maximum net torque is 262 lb. ft at 1,600 r.p.m., comparable figures for the 330 are 104 b.h.p. at 2,800 r.p.m. and 239 lb. ft. at 1,600 r.p.m.
Apart from the engine, the D750 tested differed from the D800 in respect of the gearbox and rear axle. These two items are complementary because the axle was a Ford single-speed unit and for this the Clark 2651 gearbox has to be fitted, not the Clark 2621, which has closer forward ratios to suit a two-speed rear axle—an Eaton two-speed unit was fitted in the D800 tested.
The same gearbox and axle as fitted in the D800 are available in the D750 and there is an optional Ford singlespeed unit with a capacity of 19,500 lb., compared with the 18,500 lb. of the one on the test vehicle. There is also an Eaton single-speed with the same capacity. These two axles are available with ratios from 5.57 to 7.17 to 1, whereas the Eaton 16802, 19,500 lb., two-speed axle can be had with ratios of 4.88/6-77, 5.570-74 and 644/8.54 to 1.
Besides the 617 to 1 ratio as fitted in the test D750, 5-29 and 6.8 to 1 are available; but after my test I would say that for normal medium-duty tipping work, such as delivering sand and ballast and other building materials, the set-up was quite satisfactory. It may be possible even to get away with using the higher axle ratio available-5.29 to 1—as the gear ratios gave an adequate hill performance. The rear-axle ratios avialable in the D750 tipper are numerous. There are seven distinct ratios for the singlespeed axles and three sets of two-speed ratios for the Eaton unit. I can see little reason for having so many, and little call for the lowest values such as the 7-17 to 1 single-speed and the 614/8-54 two-speed. The others should give a wide enough choice to an operator for even the worst conditions, including vehicles spending their whole time off the road.
Most types of tipper operation would in my opinion be met by the 4-88/6-77 two-speed axle, which would give adequate performance with excellent fuel economy for journeys on the road. In considering the transmission layouts it must be remembered that only direct-drive top gearboxes are available in the D range; similar ranges of axle ratio are common in British tipper chassis, but often overdrive top gearboxes are available.
The braking system on the D750 tested was the standard layout, being air-assisted hydraulic using a Clayton Dewandre Airpak booster. Optional systems are vacuum assisted hydraulic and air-hydraulic with a dual-circuit layout: The system gave a good performance and handbrake efficiency was adequate to meet the requirements for holding the vehicle on a 1 in 6-25 gradient. But I would have preferred the dual system as fitted to the D800 I tested, which gives the extra margin of safety in the event of failure of one part of the system. And when the recently issued draft proposals on braking for all goods vehicles become law on January 1, 1967, the split system will have to be fitted because a multi-pull handbrake will only be acceptable as the secondary brake if it reaches an efficiency of 25 per cent on the first pull. This was not the case on the D750 tested.
In every other respect—steering, suspension and so on— the D750 was standard, including the cab which had a single passenger seat and was the tilt version. For the tests the tipper was loaded with gravel weighing 6 tons 12-75 cwt. with the unladen weight of 4 tons 11-25 cwt. and two men in the cab the gross figure was close to the design figure of 25,500 lb. (11-4 tons), being only 0.5 cwt. less. It was interesting to note that even though carrying the maximum weight the gravel was still 9 in. or so below the top of the sides—I wonder how often the model will be correctly loaded!
Brake tests were the first to be carried out and on these the D750 gave a very good performance—not only in the figures obtained, but in the way in which the vehicle came to a halt in a stable manner. Because of the short wheelbase there was the unavoidable " bouncing " of the front end, which resulted in the Tapley meter scale jumping round past the 100 mark on all the stops except one from 30 m.p.h. when it showed 97 per cent. With the D800, similar stopping-distance figures to the 22-2 ft. and 49-8 ft. from 20 and 30 m.p.h. respectively were obtained; but with that vehicle there had been little marking of the road.
With the D750 there was marking by both the front and rear wheels on the stops, the actual pattern varying with the speeds of the particular test. The fronts never locked for more than 2 ft. but the rears did so heavily for about half the distance from 20 m.p.h. and for about 30 ft. from 30 m.p.h. In the latter cases the nearside rear tyres marked for this distance (the offside made shorter marks) but this was due to a very noticeable difference in the adhesion characteristics across the road surface. The handbrake efficiency of 35 per cent obtained with the Tapley meter is very good, although some pretty quick " pumping " of the umbrella-type handle was called for.
WELL UP TO STANDARD
Acceleration-performance figures were a little worse than those obtained on the D800, but even so they were well up to the standard one would expect for a vehicle of this type. Top-gear performance, as shown by the direct-drive figures, was reasonably good in spite of a very slow pullaway from 10 m.p.h. This was understandable as, at this speed in. top gear, the engine was not very much above idling.
As already stated, the fuel-consumption figures obtained were a decided improvement on those for the D800 and these can be directly compared because the same six-mile out-and-return route on the A6 south of Luton was used. The high-speed consumption runs were carried out on the Ml motorway from the A6 junction south to the A4147 and back. On this run the maximum speed of the D750 (53 m.p.h.) was maintained for most of the way except on the gradients, which are fairly severe on this stretch. The minimum speed was 33 m.p.h. when on the gradient approaching the AS junction on the return run.
The unladen fuel-consumption run was completed on the day following the main tests over a 6-4-mile return stretch of the Southend Arterial road, A127, close to the Ford factories at Aveley. This was a fairly flat route compared with the section of A6 used for fuel tests, where figures about 10 per cent worse would possibly have been returned. But, even so, the unladen consumption would have been very good. Maximum speeds in the four lower gears were checked on the motorway and these were: 8, 14, 24 and 39 m.p.h.
Hill-climbing performance tests were carried out on Bison Hill, near Dunstable, Which is 0-75 mile long and has an average gradient of 1 in 7.5 with the maximum 1 in 6.5 over a short section. A maximum-power aaseent of the hill in the D750 was made in the reasonable time of 4 min. 27 sec. The lowest gear used on the climb was first, which was engaged for 1 min. 34 sec., and the minimum speed was 4 m.p.h.—just before first gear was engaged. Once in bottom, the speed rose and the vehicle completed the steepest section close to the maximum speed in first gear.
Brake fade was assessed on a run down the hill in neutral with the brakes applied to restrict the speed to 20 m.p.h. Where the gradient levels out near the bottom, top gear was engaged and full throttle applied with the brakes still on to keep the speed to the same figure. When at the bottom, a maximum pressure stop from 20 m.h.p. gave similar results to the previous cold-drum tests—the rear wheels locked, the fronts marked the road slightly and the Tapley meter gauge went past the 100 per cent mark. From this, it can safely be assumed that the D750 will not give problems with fade.
A further trip up the hill was made for stop-and-restart tests and easy restarts were made in bottom gear when facing up the hill and in reverse when facing down. In both positions the handbrake held the vehicle comfortably. These results were not surprising because the theoretical maximum gradient for the D750 with the transmission layout as on the vehicle tested is 1 in 4.
As far as driving is concerned, the remarks made in the road test report of the D800 apply. The fact that the test vehicle had the standard version of the tilt cab (not the better-quality Custom option) did not detract to any great degree in the comfort provided. The operating pedals and handbrake are equally easy to use. Against power steering on the D800 tested, the tipper had the standard Cam Gears 350Q worm-and-peg unit without this option. Nevertheless, handling the D750 called for no undue exertion.
GOOD SUSPENSION TOO
Well-designed suspension is a feature of the D series; this was confirmed with the D800, and also with the D750. But with the latest test vehicle this was assessed both on normal road running and also on unmade roads in the vicinity of a sand and gravel pit. Whilst this will not give the most severe conditions that a tipper would work on, it was, as already stated, typical of those that vehicles engaged on building-material deliveries would meet.
The test vehicle had tyre equipment which would commonly be specified for tippers on this type of work, these being Goodyear Hi-Miler highway tyres. For more arduous conditions on/off-the-road tyres would normally be specified. If used a lot on main roads these tyreswould not give the same life.
When driven on the unmade roads between the sand-pit loading area and a nearby tip, the suspension performed very well, both when the vehicle was laden and unladen. In the latter state there was some clattering of the body on its front support pads, but there was no harshness in the suspension and no violent " kick-back " at the steering wheel. On one part the tipper was driven over a very rough area with many potholes and, although these were deep in places, ground clearance was sufficient to prevent any part of the vehicle fouling the ground.
As tested, the D750 tipper costs f1,325 for the chassis/cab. The Edbro 6 cu. yd. body costs £270.