From
Page 20
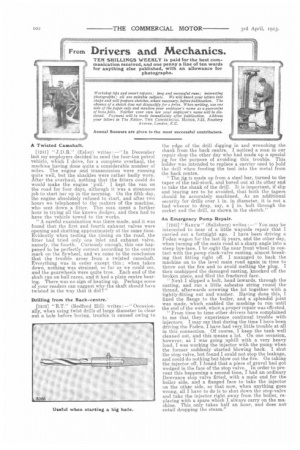
Page 21
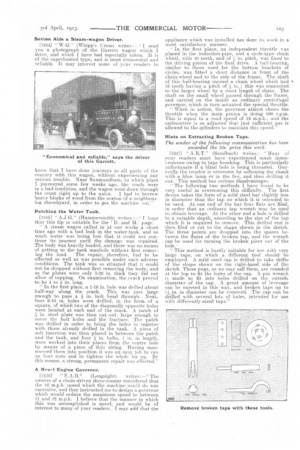
If you've noticed an error in this article please click here to report it so we can fix it.
Drivers and Mechanics.
TEN SHILLINGS WEEKLY is paid for the best com munication received, and one penny a line of ten words for anything else published, with an allowance for
photographs.
_ Workshop tips and smart rePairs; long and successful runs; interesting photographs; all are suitable subjects. We will knock your letters into shape and will prepare sketches, where necessary, before Oublication. The absence of a sketch does not disqualify for a Prize. When writing, use one side of the paper only and mention your employer's name as a guarantee of bona fides. Neither your own nor your employer's name will be disclosed. Payment will be made immediately after publication. Address your letters to The Editor, THE COMMERCIAL MOTOR, 7-15, Rosebery Avenue, London, E.C.
Annual Bonuses are given to the most SLICCe501.11 contributors.
A Twisted Camshaft, [1241] " J.D.R." (Esher) writes :—" In December last my employers decided to send the four-ton petrol vehicle, which I drive, for a complete overhaul, the machine having done quite a considerable number of miles. The engine and transmission were running quite well, but the shackles were rather badly worn. After the overhaul, nothing that the fitters could do would make the engine 'pull.' I kept the van on the road for four days, although it was a strenuous job to start her up in the morning. On the fifth day, the engine absolutely refused to start, and after two hours we telephoned to the makers of the machine, who sent down a fitter. This man spent a further hour in trying all the known dodges, and then had to have the vehicle towed to the works.
"A careful examination was there made, and it was found that the first and fourth exhaust valves were opening and shutting approximately at the same time. Evidently when testing the timing on the road, the fitter had tried only one inlet and exhaust valve, namely, the fourth. Curiously enough, this one happened to be perfectly correct according to the centre mark on the flywheel, and we came to the conclusion that the trouble arose from a twisted camshaft. Everything was in order except this ; when taken down, nothing was strained, BO far as we could see, and the gearwheels were quite true. Each end of the shaft ran on ball-races, and it had a plain centre bearing. There was no sign of heating up. Perhaps some of your readers can suggest why, the shaft should have twisted in the way that it did ? '
Drilling from the Back-centre.
[1212-.1 " R.T." (Bedford Hill) writes :—" Occasionally, when using twist drills of large diameter to clear out a hole before boring, trouble is caused owing to
the edge of the drill digging in and wrenching the shank from the back centre. I noticed a man in our repair shop the other day who had made up a special jig for the purpose of avoiding this trouble. This holder was intended to replace a carrier used to hold the drill when feeding the tool into the metal from the back centre.
"The jig is made up from a steel bar, turned to the taper of the tail-stock, and bored out at its other end to take the shank of the drill. It is important, if slip and tearing are to be avoided, that both the tapers should be accurately machined. As an additional security for drills over 1 in. in diameter, it is not a bad wheeze to drop, say, a a in. bolt through the socket and the drill, as shown in the sketch."
An Emergency Pump Repair.
[1243] " SARUM " (Salisbury) writes :—" You may be interested to hear of a little wayside repair that I carried out a fortnight ago. I have been driving a Foden wagon for the last 31years, and the other day, when turning off the main road at a sharp angle into a steep bye-lane, I brlught the near front wheel in contact with the pump clack-valve casting, almost breaking that fitting right off. I managed to back the machine on to the level main road again. in time to throw out the fire and to avoid melting the plug. I then unshipped the damaged casting, knocked off the broken piece, and filed the fractured face. "Next I slipped a bolt, head inwards, through the casting, and ran a little asbestos string round th& thread, afterwards screwing the lot together with a tightly-fitting nut and washer. Having done this, I fixed the flange to the boiler, and a splendid joint was made, which enabled the machine to run until the end of the week, when a proper repair was effected. "From time to time other drivers have complained to me that they experience continual trouble with, injectors. I may say that during the time I have been driving the Foden, I have had very little trouble at all in this connection. Of course, I keep the tank well cleaned out, and this means a lot. On one occasion, however, as I was going uphill with a very heavy load, I was working the injector with the pump when. the former suddenly started blowing back. I shut the stop valve, but found I could not stop the leakage, and could do nothing but blow out the fire. On taking the injector off. I found that a piece of gravel had got wedged in the face of the stop valve. In order to prevent this happening a second time, t had an ordinary Dewrance stop valve fitted, with a male end for theboiler side, and a flanged face to take the injector on the other side, so that now, when anything goes wrong, all I have to do is to shut down the stop-valve and take the injector right away from the boiler, replacing with a spare which I always carry on the machine. This only takes half an hour, and does notentail dropping the steam."
Sexton Aids a Steam-wagon Driver.
[12441 " W.G." (Whipp's Cross) writes : • 1 send you a photograph of the Garrett wagon which I drive, and which I have had especially taken. It is of the superheated type, and is most economical and reliable. It may interest some of your readers to
know that I have done journeys to all parts of the country with this wagon, without experiencing any serious trouble. Near Saxmundham, to which place 1 journeyed some few weeks ago, the roads were in a bad condition, and the wagon went down through the crust right up to the axles. I had to borrow heavy blocks of wood from the sexton of aneighbouring churchyard, in order to get the machine out."
Patching the Water Tank.
[12451 "A.J.G." (Hammersmith) writes---"! hope that this tip is suitable for the D. and M. page. " A steam wagon called in at our works a short time ago with a, bad leak in the water-tank. and so much water was being lost that it could not continue its journey until the damage was repaired. The body was heavily loaded, and there was no means of getting to the tank manhole without first remov
ing the load. The repair, therefore, had to be effected as well as was possible under such adverse conditions. The tank was so situated that. it could not be dropped without first removing the body, and as the plates were only 3-32 in, thick they did not allow of tapping. On examination, the crack proved to be 4 to 5 in. long.
"In the first place, a 1-16 in. hole was drilled about half-way along the crack. This was just large
enough to pass a in. bolt head through. Next, four 9-16 in. holes were drilled, in the form of a square, of which two of the diagonally opposite holes were located at each end of the crack. A patch of ; in. steel plate was then cut out, large enough to cover the bolt holes and the fracture. The patch was drilled in order to bring the holes in register with those already drilled in the tank. A piece of soft insertion was then placed in between the patch and the tank, and four in. bolts, 1 in. in length, were worked into their places from the centre hole by means of a piece of thin string. Having manoeuvred them into position it was an easy job to run on four nuts and to tighten the whole lot up. By this means, a strong, permanent repair was effected."
A NovP1 Engine Governor.
[12161 (Longsight) writes :—" The owners of a chain-driven three-tonner considered that the 16 m.p.h. speed which the machine could do was excessive, and they instructed me to design a governor which would reduce the maximum speed to between 11 and 12 m.p.h. I believe that the manner in which this was accomplished is novel, and would be of interest to many of your readers. I may add that the appliance which was installed has done its work in a most satisfactory manner.
" In the first place, an independent throttle was placed in the induction-pipe, and a cycle-type chain wheel, with 40 teeth, and of in. pitch, was fixed to the driving pinion of the final drive. A ball-hearing, similar to those used for the bottom brackets of cycles, was fitted a short distance in front of the chain-wheel and to the side of the frame. The shaft of this ball-bearing carried a chain wheel which had 16 teeth having a pitch of -.1; in.; this was connected to the larger wheel by a short length of chain. The shaft on the small wheel passed through the frame, and carried on the inside an ordinary centrifugal governor, which in turn actuated the special throttle.
" When in action, the governor almost closes the throttle when the main pinion is doing 500 r.p.m. This is equal to a road speed of 12 m.p.h., and the carburetter is so adjusted that just sufficient gas is allowed to the cylinders to maintain this speed."
Hints on Extracting Broken Taps.
The sender of the following communication has been awarded the Ws. prize this week.
11247] " A.R.T." (Sandbach) writes: Many of
your readers must have experienced much inconvenience owing to taps breaking. This is particularly unfortunate if a blind hole is being threaded. Generally the trouble is overcome by softening the shank with a blow lamp or in the fire., and then drilling it ant. This method has serious theadyantages. The following two methods I have found to be very useful in overcoming this difficulty. The first device takes the form of a mild steel bar slightly less in diameter than the tap on which it is intended to be used. At one end of the bar four flats are filed, in order that an ordinary tap wrench may be used to obtain leverage. At the other end a hole is drilled to a suitable depth, according to the size of the tap which it is required to remove. This drilled end is then filed or cut to the shape shown in the sketch. The three points are dropped into the spaces between the flutes of the broken tap, and the wrench can he used for turning the broken piece out of the
" This method is hardly suitable for use %Ali very large taps, on which a different tool should be employed. A mild steel cap is drilled to Lake drifts of the shape shown on the right-hand side of the sketch. These pegs, as we may call them, are rounded at the top to fit the holes of the cap. A pin wrench is made to fit into holes drilled on the outside diameter of the cap. A great amount of leverage can be exerted in this way, and broken taps up to in. in diameter can be removed. The cap can be drilled with several lots of holes, intended for use with differently-sized taps."