PROFILE
Page 43
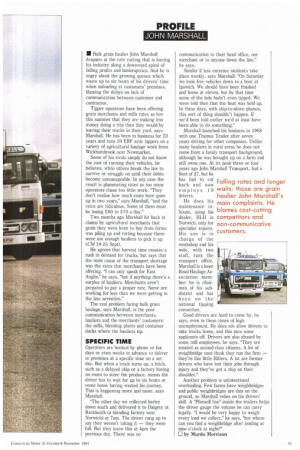
If you've noticed an error in this article please click here to report it so we can fix it.
JOHN MARSHALL
• Bulk grain haulier John Marshall despairs at the rate cutting that is forcing his industry along a downward spiral of falling profits and bankruptcies. And he is angry about the growing queues which waste up to six hours of his drivers' time when unloading at customers' premises, blaming the delays on lack of communication between customer and contractor.
Tipper operators have been offering grain merchants and mills rates so low this summer that they are making less money doing a trip than they would by leaving their trucks in their yard, says Marshall. He has been in business for 23 years and runs 20 ERF artic tippers on a variety of agricultural haulage work from Wickhambrook near Newmarket.
Some of his rivals simply do not know the cost of running their vehicles, he believes, while others break the law to survive or struggle on until their debts become unmanageable. In any case the result is plummeting rates as too many operators chase too little work. "They don't realise how much costs have gone up in two years," says Marshall, "and the rates are ridiculous. Some of them must be losing £60 to £70 a day."
Two months ago Marshall hit back at claims by agricultural merchants that grain they were keen to buy from farms was piling up and rotting because there were not enough hauliers to pick it up (CM 19-25 Sept).
He agrees that harvest time creates a rush in demand for trucks, but says that the main cause of the transport shortage was the rates that merchants have been offering. "I can only speak for East Anglia," he says, "but if anything there's a surplus of hauliers. Merchants aren't prepared to pay a proper rate. Some are working for less than we were getting in the late seventies."
The real problem facing bulk grain haulage, says Marshall, is the poor communication between merchants, hauliers and the merchants' customers: the mills, blending plants and container docks where the hauliers tip.
SPECIFIC TIME
Operators are booked by phone or fax days or even weeks in advance to deliver to premises at a specific time on a set day. But when a truck turns up, a hitch, such as a delayed ship or a factory having no room to store the produce, means the driver has to wait for up to six hours or come home having wasted his journey. This is happening more and more, says Marshall.
"The other day we collected barley down south and delivered it to Dalgety at Rackheath (a blending factory near Norwich) at 7am. The driver rung up to say they weren't taking it — they were full. But they knew this at 4pm the previous day. There was no communication to their head office, our merchant or to anyone down the line," he says.
Similar if less extreme incidents take place weekly, says Marshall: "On Saturday we took five vehicles down to a boat at Ipswich. We should have been finished and home at eleven, but by that time some of the lads hadn't even tipped. We were told then that the boat was held up. In these days, with ship-to-shore phones, this sort of thing shouldn't happen. If we'd been told earlier we'd at least have been able to do something."
Marshall launched his business in 1968 with one Thames Trader after seven years driving for other companies. Unlike many hauliers in rural areas he does not come from a family transport background, although he was brought up on a farm and still owns one. At its peak three or four years ago John Marshall Transport, had a fleet of 27, but he has had to cut back and now employs 19 drivers.
He does his maintenance inhouse, using his dealer, HLH in Norwich, only for specialist repairs. His son is in charge of the workshop and his wife, with two staff, runs the transport office. Marshall is a keen Road Haulage Association member: he is chairman of his subdistrict and has been on the national tipping committee.
Good drivers are hard to come by, he says, even in these times of high unemployment. He does not allow drivers to take trucks home, and this puts some applicants off. Drivers are also abused by some mill employees, he says. "They are treated as second-class citizens. A lot of weighbridge men think they run the firm — they're like little Hitlers. A lot are former drivers who have lost their jobs through injury and they've got a chip on their shoulder."
Falling rates and longer waits: those are grain haulier John Marshall's main complaints. He blames cost-cutting competitors and non-communicative customers.
/111/111t
Another problem is unintentional overloading. Few farms have weighbridges and public weighbridges are thin on the ground, so Marshall relies on his drivers' skill. A "Plimsoll line" inside the trailers helps the driver gauge the volume he can carry legally. "I would be very happy to weigh every load we collect," he says, "but where can you find a weighbridge after loading at nine o'clock at night?"
D by Murdo Morrison