From the
Page 28
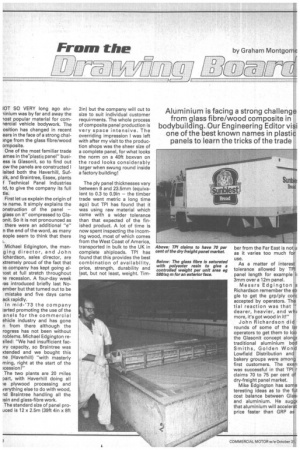
Page 29
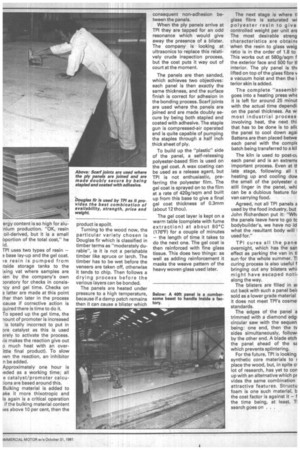
If you've noticed an error in this article please click here to report it so we can fix it.
by Graham Montgom€
7 z7 )al 0 ( C a F7( 0 "71 I
Aluminium is facing a strong challenge from glass fibre/wood composite in bodybuilding. Our Engineering Editor visi one of the best known names in plastic panels to learn the tricks of the trade
IOT SO VERY long ago alulinium was by far and away the lost popular material for cornlercial vehicle bodywork. The osition has changed in recent ears in the face of a strong chalmge from the glass fibre/wood omposite.
One of the most familiar trade ames in theplastic panel" busiess is Glasonit, so to find out ow the panels are constructed I isited both the Haverhill, Suf)1k, and Braintree, Essex, plants f Technical Panel Industries td, to give the company its full tle.
First let us explain the origin of le name. It simply explains the onstruction of the panel — glass on it" compressed to Glaonit. So it is not pronounced as there were an additional "e" n the end of the word, as many eople seem to think that there Michael Edgington, the manging director, and John ichardson, sales director, are xtremely proud of the fact that )e company has kept going allost at full stretch throughout le recession. A four-day week (as introduced briefly last Noember but that turned out to be mistake and five days came ack rapidly.
In mid-'7 3 the company tarted promoting the use of the anels for the commercial ehicle industry and has gone n from there although the rogress has not been without roblems. Michael Edgington re311ed: "We had insufficient fac)ry capacity, so Braintree was xtended and we bought this ne (Haverhill) "with masterly ming, right at the start of the )cession!"
The two plants are 20 miles Dart, with Haverhill doing all le plywood processing and verything else to do with wood, Id Braintree handling all the :sin and glass-fibre work.
The standard size of panel prouced is 12 x 2.5m (39ft 41n x 8ft 2in) but the company will cut to size to suit individual customer requirments. The whole process of composite panel production is very space intensive. The overriding impression I was left with after my visit to the production shops was the sheer size of a complete panel, for what looks the norm on a 40ft boxvan on the road looks considerably larger when swung round inside a factory building!
The ply panel thicknesses vary between 8 and 23.5mm (equivalent to 0.3 to 0.9in — the timber trade went metric a long time ago) but TPI has found that it was using raw material which came with a wider tolerance than that expected of the finished product. A lot of time is now spent inspecting the incoming wood, most of which comes from the West Coast of America, transported in bulk to the UK in complete shiploads. TPI has found that this provides the best combination of availability, price, strength, durability and last, but not least, weight. Tim ber from the Far East is not u as it varies too much for use.
As a matter of interest tolerance allowed by TPI panel length for example I! 3mm over a 12m panel.
Messrs Edgington a Richardson remember the str gle to get the grp/ply con( accepted by operators. The tial reaction was that " dearer, heavier, and wh more, it's got wood in it!"
John Richardson did rounds of some of the lar operators to get them to loo the Glasonit concept along: traditional aluminium bod Smiths, Golden Wond Lowfield Distribution and bakery groups were among first customers. The exen was successful in that TPI r claims 70 to 75 per cent of dry-freight panel market.
Mike Edgington has some teresting ideas as to the fut Cost balance between Glasr and aluminium. He sugg( that aluminium will accelerat price faster than GRP as ergy content is so high for alunium production. "OK, resin oil-derived, but it is a small °portion of the total cost," he id.
TPI uses two types of resin — a base lay-up and the gel coat. le resin is pumped from Aside storage tanks to the )(frig vat where samples are cen by the company's own aoratory for checks in consisicy and gel time. Checks on a latter are made at this point [her than later in the process cause if corrective action is quired there is time to do it.
To speed up the gel time, the iount of promoter is increased is totally incorrect to put in ore catalyst as this is used erely to activate the process. is makes the reaction give out o much heat with an overittle final product). To slow Iwn the reaction, an inhibitor n be added.
Approximately one hour is !eded as a working time; all e catalyst/promoter calcu:ions are based around this. • Bulking material is added to ake it more thixotropic and is again is a critical operation if the bulking material content aes above 10 per cent, then the product is spoilt.
Turning to the wood now, the particular variety chosen is Douglas fir which is classified in timber terms as "moderately durable", ie it is not a perishable timber like spruce or larch. The timber has to be wet before the veneers are taken off, otherwise it tends to chip. Then follows a drying process before the various layers can be bonded.
The panels are heated under pressure to a high temperature, because if a damp patch remains then it can cause a blister which
consequent non-adhesion between the panels.
When the ply panels arrive at TPI they are tapped for an odd resonance which would give away the presence of a blister. The company is looking at ultrasonics to replace this relatively crude inspection process, but the cost puts it way out of court at the moment.
The panels are then sanded, which achieves two objectives: each panel is then exactly the same thickness, and the surface finish is correct for adhesion in the bonding process. Scarf joints are used where the panels are joined and are made doubly secure by being both stapled and coated with adhesive. The staple gun is compressed-air operated and is quite capable of pumping the staples through a half inch thick sheet of ply.
To build up the "plastic" side of the panel, a self-releasing polyester-based film is used on the gel coat. A wax coating can be used as a release agent, but TPI is not enthusiastic, preferring the polyester film. The gel coat is sprayed on to the film at a rate of 420g/sqm and built up from this base to give a final gel coat thickness of 0.3mm (about 12 thou).
The gel coat layer is kept on a warm table (complete with fume extraction) at about 80°C (176°F) for a couple of minutes — the length of time it takes to do the next one. The gel coat is then reinforced with fine glass tissue. This does two things: as well as adding reinforcement it masks the weave pattern of the heavy woven glass used later.
The next stage is where tl glass fibre is saturated wi polyester resin to give controlled weight per unit are The most desirable streng characteristics are obtaine when the resin to glass weig ratio is in the order of 1.8 to This works out at 580g/sqm f the exterior face and 500 for tl interior. The ply panel is the lifted on top of the glass fibre v a vacuum hoist and then the i tenor skin is added.
The complete "assembl, goes into a heating press whe it is left for around 26 rninut with the actual time dependil on the panel thickness. As wi most industrial process, involving heat, the next IN, that has to be done is to allc the panel to cool down agai Battens are then placed betwe each panel with the comple batch being transferred to a kil
The kiln is used to post-ce each panel and is an extreme important process. Even at if late stage, following all t heating up and cooling clam the smell of the polyester c still linger in the panel, whi can be a dubious feature for van carrying food.
Agreed, not all TPI panels a used by the food industry, but John Richardson put it: "Wh, the panels leave here to go tc bodybuilder's, we have no id what the resultant body will I used for."
TPI cures all the pane overnight, which has the san effect as parking the van in tl sun-for the whole summer. TI curing process is also useful f bringing out any blisters whil might have escaped notii along the way.
The blisters are filled in ar cut back with such a panel beir sold as a lower grade material it does not meet TPI's cosme. standards.
The edges of the panel a trimmed with a diamond edgi circular saw with the sequen being: one end, then the tv sides simultaneously, follow] by the other end. A blade etch the panel ahead of the se which prevents splintering.
For the future, TPI is looking synthetic core materials to r place the wood, but, in spite 01 lot of research, has yet to con up with an alternative which pr vides the same combination attractive features. Structu foam is one such material, b the cost factor is against it — f the time being, at least. TI search goes on . . .