ERODYNAMIC DVANTAGES Aerodynamics are more usually associated with jet aircraft
Page 48
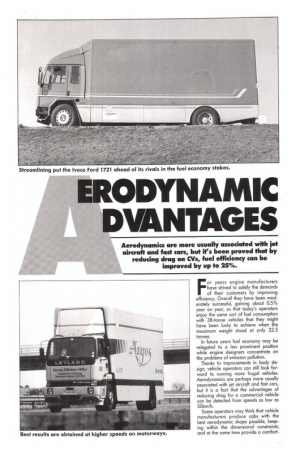
Page 49
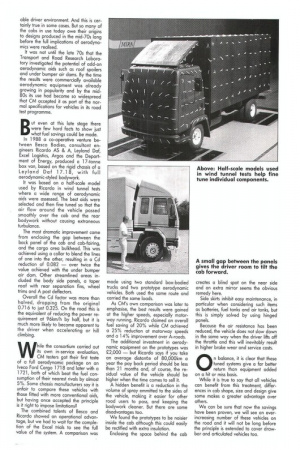
If you've noticed an error in this article please click here to report it so we can fix it.
and fast cars, but it's been proved that by reducing drag on CVs, fuel efficiency can be improved by up to 25%.
For years engine manufacturers have strived to satisfy the demands of their customers by improving efficiency. Overall they have been moderately successful, gaining about 0.5% year on year, so that today's operators enjoy the same sort of fuel consumption with 38-tonne vehicles that they might have been lucky to achieve when the maximum weight stood at only 32.5 tonnes.
In future years fuel economy may be relegated to a less prominent position while engine designers concentrate on the problems of emission pollution.
Thanks to improvements in body design, vehicle operators can still look forward to running more frugal vehicles. Aerodynamics are perhaps more usually associated with jet aircraft and fast cars, but it is a fact that the advantages of reducing drag for a commercial vehicle can be detected from speeds as low as 50km/h.
Some operators may think that vehicle manufacturers produce cabs with the best aerodynamic shape possible, keeping within the dimensional constraints, and at the same time provide a comfort able driver environment. And this is certainly true in some cases. But so many of the cabs in use today owe their origins to designs produced in the mid-70s long before the full implications of aerodynamics were realised.
It was not until the late 70s that the Transport and Road Research Laboratory investigated the potential of add-on aerodynamic aids such as roof spoilers and under bumper air dams. By the time the results were commercially available aerodynamic equipment was already growing in popularity and by the mid80s its use had become so widespread that CM accepted it as part of the normal specifications for vehicles in its road test programme.
But even at this late stage there were few hard facts to show just what fuel savings could be made. In 1 988 a co-operative venture between Besco Bodies, consultant engineers Ricardo AS & A, Leyland Daf, Excel Logistics, Argos and the Department of Energy, produced a 17-tonne box van, based on the rigid chassis of a Leyland Daf 17.18, with full aerodynamic-styled bodywork.
It was based on a half-scale model used by Ricardo in wind tunnel tests where a wide range of aerodynamic aids were assessed. The best aids were selected and then fine tuned so that the air flow around the vehicle passed smoothly over the cab and the rear bodywork without causing extraneous turbulance.
The most dramatic improvement came from enclosing the gap between the back panel of the cab and cab-fairing, and the cargo area bulkhead. This was achieved using a collar to blend the lines of one into the other, resulting in a Cd reduction of 0.082 — over twice the value achieved with the under bumper air dam. Other streamlined areas included the body side panels, a taper roof with rear separation fins, wheel trims and A post deflectors.
Overall the Cd factor was more than halved, dropping from the original 0.716 to just 0.325. On the road this is the equivalent of reducing the power requirement at 96km/h by half, but it is much more likely to become apparent to the driver when accelerating or hill climbing.
While the consortium carried out its own in-service evaluation, CM testers got their first taste of a full aerodynamic package on an Iveco Ford Cargo 1 71 8 and later with a 1721, both of which beat the fuel consumption of their nearest rivals by almost 5%. Some chassis manufacturers say it is unfair to compare these vehicles with those fitted with more conventional aids, but having once accepted the principle is it right to impose limitations?
The combined talents of Besco and Ricardo showed an operational advantage, but we had to wait for the completion of the Excel trials to see the full value of the system. A comparison was made using two standard box-bodied trucks and two prototype aerodynamic vehicles. Both used the same route and carried the same loads.
As CM's own comparison was later to emphasise, the best results were gained at the higher speeds, especially motorway running. Ricardo claimed an overall fuel saving of 20% while CM achieved a 25% reduction at motorway speeds and a 14% improvement over A-roads.
The additional investment in aerodynamic equipment on the prototypes was -£2,000 — but Ricardo says if you take an average distant° of 80,000km a year the pay back period should be less than 21 months and, of course, the residual value of the vehicle should be higher when the time comes to sell it.
A hidden benefit is a reduction in the volume of spray emmitted to the sides of the vehicle, making it easier for other road users to pass, and keeping the bodywork cleaner. But there are some disadvantages too.
We found the prototypes to be noisier inside the cab although this could easily be rectified with extra insulation.
Enclosing the space behind the cab creates a blind spot on the near side and an extra mirror seems the obvious remedy here.
Side skirts inhibit easy maintenance, in particular when considering such items as batteries, fuel tanks and air tanks, but this is simply solved by using hinged panels.
Because the air resistance has been reduced, the vehicle does not slow down in the same way when the driver lifts off the throttle and this will inevitably result in higher brake wear and service costs.
n balance, it is clear that these tuned systems give a far better return than equipment added on a hit or miss basis.
While it is true to say that all vehicles can benefit from this treatment, differences in cab shape, size and design give some makes a greater advantage over others.
We can be sure that now the savings have been proven, we will see an everincreasing number of these vehicles on the road and it will not be long before the principle is extended to cover drawbar and articulated vehicles too.