Look before you leap
Page 49
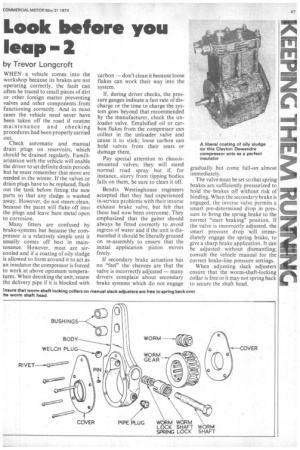
If you've noticed an error in this article please click here to report it so we can fix it.
by Trevor Longcroft
WHEN a vehicle comes into the workshop because its brakes are not operating correctly, the fault can often be traced to small pieces of dirt or other foreign matter preventing valves and other components from functioning correctly. And in most cases the vehicle need never have been taken off the road if routine maintenance and checking procedures had been properly carried out.
Check automatic and manual drain plugs on reservoirs, which should be drained regularly. Familiarization with the vehicle will enable the driver to set definite drain periods but he must remember that more are needed in the winter. If the valves or drain plugs have to be replaced, flush out the tank before fitting the new parts so that any sludge is washed away. However, do not steam clean, because the paint will flake off into the plugs and leave bare metal open to corrosion.
Many fitters are confused by brake-systems but because the compressor is a relatively simple unit it usually comes off best in maintenance. However, most are aircooled and if a coating of oily sludge is allowed to form around it to act as an insulator the compressor is forced to work at above optimum temperatures. When decoking the unit, renew the delivery pipe if it is blocked with carbon — don't clean it because loose flakes can work their way into the system.
If, during driver checks, the pressure gauges indicate a fast rate of discharge or the time to charge the system goes beyond that recommended by the manufacturer, check the unloader valve. Emulsified oil or carbon flakes from the compressor can collect in the unloader valve and cause it to stick; loose carbon can hold valves from their seats or damage them.
Pay special attention to chassismounted valves; they will stand normal road spray but if, for instance, slurry from tipping bodies falls on them, be sure to clean it off.
Bendix Westinghouse engineers accepted that they had experienced in-service problems with their inverse exhaust brake valve, but felt that these had now been overcome. They emphasized that the gaiter should always be fitted correctly to avoid ingress of water and if the unit is dismantled it should be liberally greased on re-assembly to ensure that the initial application piston moves freely.
If secondary brake actuation has no "feel" the chances are that the valve is incorrectly adjusted — many drivers complain about secondary brake systems which do not engage gradually but come full-on almost immediately.
The valve must be set so that spring brakes are sufficiently pressurized to hold the 'brakes off without risk of binding. When the secondary brake is engaged, the inverse valve permits a smart pre-determined drop in pressure to bring the spring brake to the correct "start braking" position. If the valve is incorrectly adjusted, the smart pressure drop will immediately engage the spring brake, to give a sharp brake application. It can be adjusted without dismantling; consult the vehicle manual for the correct brake-line pressure settings.
When adjusting slack adjusters ensure that the worm-shaft-locking collar is free or it may not spring back to secure the shaft head.