to 01 1 1n ita incs by Paul Brockington
Page 30
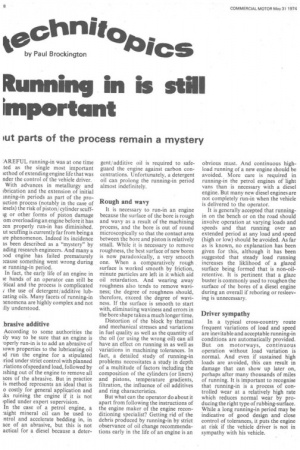
If you've noticed an error in this article please click here to report it so we can fix it.
Running in is still important
,ut parts of the process remain a mystery AREFUL running-in was at one time ted as the single most important iethod of extending engine life that was nder the control of the vehicle driver. With advances in metallurgy and tbrication and the extension of initial inning-in periods as part of the prouction process (notably in the case of iesels) the risk of piston/cylinder scuffig or other forms of piston damage om overloading an engine before it has .T.en properly run-in has diminished. ut scuffing is currently far from being a tre phenomenon. Indeed its incidence as been described as a "mystery" by ading research engineers. And many a )od engine has failed prematurely cause something went wrong during ie running-in period.
In fact, the early life of an engine in Le hands of an operator can still be itical and the process is complicated the use of detergent/ additive tubeating oils. Many facets of running-in ienomena are highly complex and not .11y understood.
.brasive additive
According to some authorities the fly way to be sure that an engine is pperly run-in is to add an abrasive of town properties to the lubricating oil id run the engine for a stipulated :riod under strict control with planned nations of speed and load, followed by ishing out of the engine to remove all ices of the abrasive. But in practice is method represents an ideal that is o costly for general application and iks ruining the engine if it is not 'plied under expert supervision.
In the case of a petrol engine, a aight mineral oil can be used to ntrol and accelerate bedding in, in ace of an abrasive, but this is not actical for a diesel because a deter gent/ additive oil is required to safeguard the engine against carbon concentrations. Unfortunately, a detergent oil can prolong the running-in period almost indefinitely.
Rough and wavy
It is necessary to run-in an engine because the surface of the bore is rough and wavy as a result of the machining process, and the bore is out of round microscopically so that the contact area between the bore and piston is relatively small. While it is necessary to remove roughness, the best surface of new bores is now paradoxically, a very smooth one. When a comparatively rough surface is worked smooth by friction, minute particles are left in it which aid oil retardation. And wearing away roughness also tends to remove waviness; the degree of roughness should, therefore, exceed the degree of waviness. If the surface is smooth to start with, eliminating waviness and errors in the bore shape takes a much longer time.
Distortion of the block by thermal and mechanical stresses and variations in fuel quality as well as the quantity of the oil (or using the wrong oil) can all have an effect on running in as well as variations in machining tolerances. In fact, a detailed study of running-in problems necessitates a study in depth of a multitude of factors including the composition of the cylinders (or liners) and pistons, temperature gradients, filtration, the influence of oil additives and ring characteristics.
But what can the operator do about it apart from following the instructions of the engine maker of the engine reconditioning specialist? Getting rid of the debris produced by running-in by strict observance of oil change recommendations early in the life of an engine is an obvious must. And continuous highload running of a new engine should be avoided. More care is required in running-in the petrol engines of light vans than is necessary with a diesel engine. But many new diesel engines are not completely run-in when the vehicle is delivered to the operator.
It is generally accepted that runningin on the bench or on the road should involve operation at varying loads and speeds and that running over an extended period at any load and speed (high or low) should be avoided. As far as is known, no explanation has been given for this, although it has been suggested that steady load running increases the liklihood of a glazed surface being formed that is non-oilretentive. It is pertinent that a glaze buster is commonly used to roughen the surface of the bores of a diesel engine during an overall if reboring or resleeving is unnecessary.
Driver sympathy
In a typical cross-country route frequent variations of load and speed are inevitable and acceptable running-in conditions are automatically provided. But on motorways, continuous operation without load variation is normal. And even if sustained high loads are avoided, this can result in damage that can show up later on, perhaps after many thousands of miles of running. It is important to recognise that running-in is a process of controlled wear at a relatively high rate which reduces normal wear by producing the right type of rubbing-surface. While a long running-in period may be indicative of good design and close control of tolerances, it puts the engine at risk if the vehicle driver is not in sympathy with his vehicle.