TAPERED SAFETY
Page 39
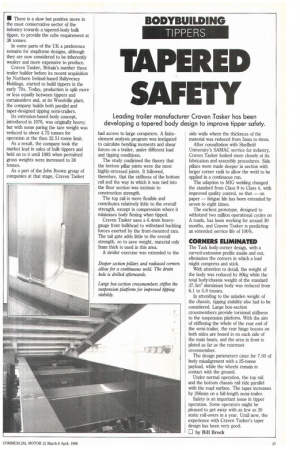
If you've noticed an error in this article please click here to report it so we can fix it.
• There is a slow but positive move in the most conservative sector of the industry towards a tapered-body bulk tipper, to provide the cube requirement at 38 tonnes.
In some parts of the UK a preference remains for stepframe designs, although they are now considered to be inherently weaker and more expensive to produce.
Craven Tasker, Britain's number three trailer builder before its recent acquisition by Northern Ireland-based Ballyvesey Holdings, started to build tippers in the early '70s. Today, production is split more or less equally between tippers and curtainsiders and, at its Woodville plant, the company builds both parallel and taper-designed tipping semi-trailers.
Its extrusion-based body concept, introduced in 1978, was originally heavy; but with some paring the tare weight was reduced to about 4.75 tonnes for operation at the then 32.51-tonne limit.
As a result, the company took the market lead in sales of bulk tippers and held on to it until 1983 when permitted gross weights were increased to 38 tonnes.
As a part of the John Brown group of companies at that stage, Craven Tasker had access to large computers. A finiteelement analysis program was instigated to calculate bending moments and shear forces on a trailer, under different load and tipping conditions.
The study confirmed the theory that the bottom pillar joints were the most highly-stressed joints. It followed, therefore, that the stiffness of the bottom rail and the way in which it was tied into the floor section was intrinsic to construction strength.
The top rail is more flexible and contributes relatively little to the overall strength, except in compression where it minimises body flexing when tipped.
Craven Tasker uses a 6.4mm heavygauge front bulkhead to withstand buckling forces exerted by the front-mounted ram. The tail gate adds little to the overall strength, so to save weight, material only 5mm thick is used in this area.
A similar exercise was extended to the Deeper section pillars and radiused corners allow for a continuous weld. The drain hole is drilled afterwards. side walls where the thickness of the material was reduced from 5mm to 4mrn.
After consultation with Sheffield University's SAMAC service for industry, Craven Tasker looked more closely at its fabrication and assembly procedures. Side pillars were made deeper in section with larger corner radii to allow the weld to be applied in a continuous run.
The adaption to MIG welding changed the standard from Class 9 to Class 4, with improved quality control, so that — on paper — fatigue life has been extended by seven to eight times.
The earliest prototype, designed to withstand two million operational cycles on A roads, has been working for around 30 months, and Craven Tasker is predicting an extended service life of 100%.
CORNERS ELIMINATED
The Task body-corner design, with a curved-extrusion profile inside and out, eliminates the corners in which a load might compress and stick.
With attention to detail, the weight of the body was reduced by 80kg while the total body/chassis weight of the standard 37.5m3 aluminium body was reduced from 6.1 to 5.8 tonnes.
In attending to the unladen weight of the chassis, tipping stability also had to be considered. Large box-section crossmembers provide torsional stiffness to the suspension platform. With the aim of stiffening the whole of the rear end of the semi-trailer, the rear hinge bosses on both sides are boxed in on each side of the main beam, and the area in front is plated as far as the rearmost crossmember.
The design parameters cater for 7.50 of body misalignment with a 25-tonne payload, while the wheels remain in contact with the ground.
Under normal operation, the top rail and the bottom chassis rail ride parallel with the road surface. The taper increases by 356mm on a full-length semi-trailer.
Safety is an important issue in tipper operation. Some operators might be pleased to get away with as few as 20 static roll-overs in a year. Until now, the experience with Craven Tasker's taper design has been very good.
O by Bill Brock