More skill put in recon bodywork
Page 126
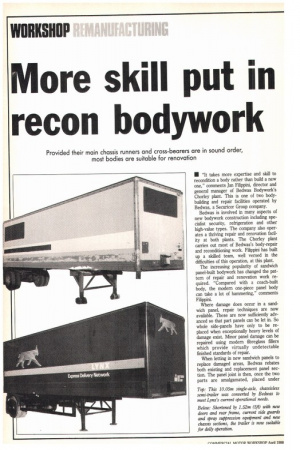
Page 127

If you've noticed an error in this article please click here to report it so we can fix it.
• "It takes more expertise and skill to recondition a body rather than build a new one," comments Jan Filippini, director and general manager of Bedwas Bodywork's Chorley plant. This is one of two bodybuilding and repair facilities operated by Bedwas, a Securicor Group company.
Bedwas is involved in many aspects of new bodywork construction including specialist security, refrigeration and other high-value types. The company also operates a thriving repair and renovation facility at both plants. The Chorley plant carries out most of Bedwas's body-repair and reconditioning work. Filippini has built up a skilled team, well versed in the difficulties of this operation, at this plant.
The increasing popularity of sandwich panel-built bodywork has changed the pattern of repair and renovation work required. "Compared with a coach-built body, the modern one-piece panel body can take a lot of hammering," comments Filippini.
Where damage does occur in a sandwich panel, repair techniques are now available. These are now sufficiently advanced so that part panels can be let in. So whole side-panels have only to be replaced when exceptionally heavy levels of damage exist. Minor panel damage can be repaired using modern fibreglass fillers which provide virtually undetectable finished standards of repair.
When letting in new sandwich panels to replace damaged areas, Bedwas rebates both existing and replacement panel section. The panel joint is then, once the two parts are amalgamated, placed under pressure which forces it flush. To finish the repair, the joint area is filled with chopped mat and resin-bonded to produce a smooth-finished repair.
According to Filippini, most bodies are suitable for renovation provided the main chassis runners and cross-bearers are in sound order. If the body sub-structure is in poor condition, however, or has to be extensively modified to fit a new chassis, then the economics of body refurbishment are considerably reduced.
With that proviso, Jan Filippini reckons that Bedwas will not find other aspects of body repair or renovation to be much of a problem. A reconditioned body, he points out, will also be better suited to today's operational environment than when it was originally built new.
When refurbishing doors, for instance, Bedwas normally will fit the latest type of bonded door-capping seal which much improves weather sealing at the rear end. Similarly the floor can be strengthened using the wear patterns caused in previous use as a guide. This results in a stronger floor unit which has the strength in exactly the right position to meet operators' loading patterns.
Curtain-sided bodywork can also be reconditioned to give higher strength levels than new. A common failure area with earlier types of curtain-sider is the top roof-corner sections cracking. Often this has been caused by the original bodybuilder making these sections too rigid. In reconditioning or rebuilding Bedwas can fit internal gussets which diffuse stresses from these areas.
As well as replacing door seals, older types of timber-framed doors used on many early refrigerated bodies can be replaced with the latest type of insulated sandwich panel closures. Again on refrigerated or insulated bodies, higher levels of waterproofing and hygiene can be achieved.
Bedwas has rebuilt many older reefer bodies with complete "tub" floors which extend the waterproof section up to 300mm (12 inches) high on the walls. This is achieved by forming a one-piece waterproof tray section in glassfibre covering the floor and lower parts of the body walls.
Roof panels take a considerable pounding and Bedwas normally replaces multipiece roof coverings with a one-piece panel at the reconditioning stage. The company offers a choice of one-piece alloy or translucent roof section. Where body sections are damaged, Bedwas can splice in part of the cant-rail or side-rave sections to suit.
Coach-built alloy bodies which have alloy-extruded-section rear framework can be made more durable at the time of a Bedwas rebuild.
This beefing up is achieved by putting in an all-steel-welded rear-frame structure. In service this provides far greater resistance to loading/unloading manoeuvres and minor docking damage. The inclusion of an all-steel rear end allows for fitment of a tail lift at the rebuild stage. Bedwas uses 4x2 rolled steel joists to carry the tail lift rather than 10-gauge sections.
Dependent on the level of work needed to recondition a body, Bedwas reckons that this operation results in a saving of 40% on new cost. It also provides an ideal opportunity to upgrade or modify the body to meet current operational requirements.
Typical of this operation is a major rebuild programme undertaken for the National Freight Consortium subsidiary, Lynx. Here existing 10.05m (33ft) chassisIess, single-axle semi-trailers have been converted for dolly operation. This involved cutting the overall length down to 8.53m (28ft) and moving the axle forwards.
A longitudinal chassis frame from the fifth-wheel rearwards has been put in to carry the running gear and landing legs. At the rear a new frame and doors have been fitted and the remainder of the bodywork refurbished. Side guards and antispray equipment have also been fitted giving Lynx single-axle trailers engineered to meet its current operational requirements for about a third of the cost of a new trailer.
Bedwas Bodywork Turbo 87