• REFRIGERATED TRANSPORT: HOW • COULD ASSIST THE OPERATORS
Page 50
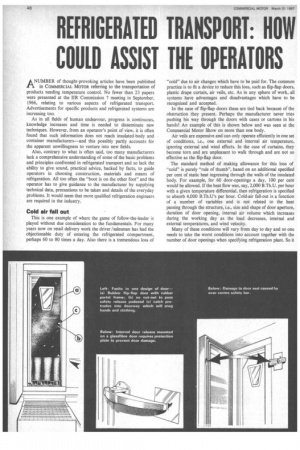
Page 51
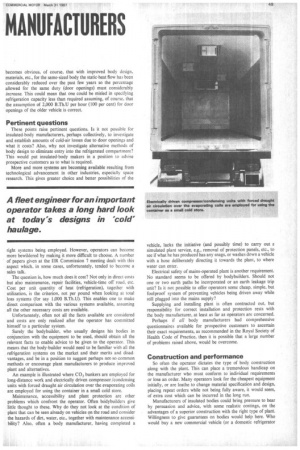
Page 52
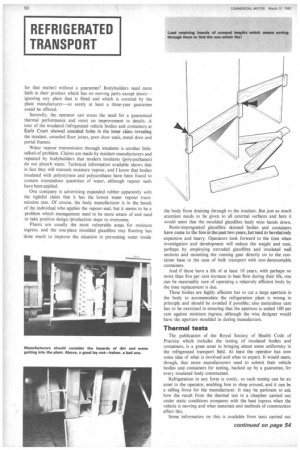
Page 56
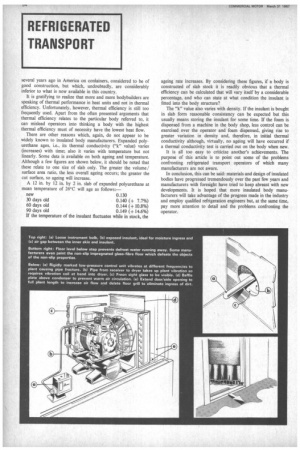
If you've noticed an error in this article please click here to report it so we can fix it.
ANUMBER of thought-provoking articles have been published in COMMERCIAL MOTOR referring to the transportation of products needing temperature control. No fewer than 23 papers were presented at the HR Commission 7 meeting in September, 1966, relating to various aspects of refrigerated transport. Advertisements for specific products and refrigerated systems are increasing too.
As in all fields of human endeavour; progress is continuous, knowledge increases and time is needed to disseminate new techniques. However, from an operator's point of view, it is often found that such information does not reach insulated-body and container manufacturers—and this possibly partly accounts for the apparent unwillingness to venture into new fields.
Also, contrary to what is often said, too many manufacturers lack a comprehensive understanding of some of the basic problems and principles confronted in refrigerated transport and so lack the ability to give sound, practical advice, backed by facts, to guide operators in choosing construction, materials and means of refrigeration. All too often the "boot is on the other foot" and the operator has to give guidance to the manufacturer by supplying technical data, precautions to be taken and details of the everyday problems. It would seem that more qualified refrigeration engineers are required in the industry.
Cold air fall out
This is one example of where the game of follow-the-leader is played without due consideration to the fundamentals. For many years now on retail delivery work the driver /salesman has had the objectionable duty of entering the refrigerated compartment, perhaps 60 to 80 times a day. Also there is a tremendous loss of
"cold" due to air changes which have to be paid for. The common practice is to fit a device to reduce this loss, such as flip-flap doors, plastic drape curtain, air veils, etc. As in any sphere of work, all systems have advantages and disadvantages which have to be recognized and accepted.
In the case of flip-flap doors these are tied back because of the obstruction they present. Perhaps the manufacturer never tries pushing his way through the doors with cases or cartons in his hands! An example of this is shown below and was seen at the Commercial Motor Show on more than one body.
Air veils are expensive and can only operate efficiently in one set of conditions, i.e., one external and internal air temperature, ignoring external and wind effects. In the case of curtains, they become torn and are unpleasant to walk through and are not so effective as the flip-flap door.
The standard method of making allowance for this loss of "cold" is purely "rule of thumb", based on an additional specified per cent of static heat ingressing through the walls of the insulated body. For example, for 60 door-openings a day, 100 per cent would be allowed. If the heat flow was, say, 2,000 B.Th.U. per hour with a given temperature differential, then refrigeration is specified to absorb 4,000 B.Th.U's per hour. Cold-air fall-out is a function of a number of variables and is not related to the heat passing through the structure, i.e., size and shape of door aperture, duration of door opening, internal air volume which increases during the working day as the load decreases, internal and external temperatures, and wind velocity.
Many of these conditions will vary from day to day and so one needs to take the worst conditions into account together with the number of door openings when specifying refrigeration plant. So it
becomes obvious, of course, that with improved body design, materials, etc., for the same-sized body the static-heat flow has been considerably reduced over the past few years so the percentage allowed for the same duty (door openings) must considerably increase. This could mean that one could be misled in specifying refrigeration capacity less than required assuming, of course, that the assumption of 2,000 B.Th.0 per hour (100 per cent) for door openings of the older vehicle is correct.
Pertinent questions
These points raise pertinent questions. Is it not possible for insulated-body manufacturers, perhaps collectively, to investigate and establish amounts of cold-air losses due to door openings and what it costs? Also, why not investigate alternative methods of body design to eliminate entry into the refrigerated compartment? This would put insulated-body makers in a position to advise prospective customers as to what is required.
More and more systems are becoming available resulting from technological advancement in other industries, especially space research. This gives greater choice and better possibilities of the right systems being employed. However, operators can become more bewildered by making it more difficult to choose. A number of papers given at the IIR Commission 7 meeting dealt with this aspect which, in some cases, unfortunately, tended to become a sales talk.
The question is, how much does it cost? Not only in direct costs but also maintenance, repair facilities, vehicle-time off road, etc. Cost per unit quantity of heat (refrigeration), together with utilization, is the criterion, not per pound when looking at total loss systems (for say 1,000 B.Th.U). This enables one to make direct comparison with the various systems available, assuming all the other necessary costs are available.
Unfortunately, often not all the facts available are considered and costs are only realized after the operator has committed himself to a particular system.
Surely the bodybuilder, who usually designs his bodies in conjunction with the equipment to be used, should obtain all the relevant facts to enable advice to be given to the operator. This means that the body-builder would need to be familiar with all the refrigeration systems on the market and their merits and disadvantages, and be in a position to suggest perhaps not-so-common methods or encourage plant manufacturers to produce improved plant and alternatives.
An example is illustrated where CO2 bunkers are employed for long-distance work and electrically driven compressor /condensing units with forced draught air circulation over the evaporating coils are employed for using the container in a small cold store,
Maintenance, accessibility and plant protection are other problems which confront the operator. Often bOdybuilders give little thought to these. Why do they not look at the condition of plant that can be seen already on vehicles on the road and consider the hazards of dirt, water, etc., together with maintenance accessibility? Also, often a body manufacturer, having completed a vehicle, lacks the initiative (and possibly time) to carry out a simulated plant service, e.g., removal of protection panels, etc., to see if what he has produced has any snags, or washes down a vehicle with a hose deliberately directing it towards the plant, to where water can enter.
Electrical safety of mains-operated plant is another requirement. No standard seems to be offered by bodybuilders. Should not one or two earth paths be incorporated or an earth leakage trip unit? Is it not possible to offer operators some cheap, simple, but foolproof system of preventing vehicles being driven away while still plugged into the mains supply?
Supplying and installing plant is often contracted out, but responsibility for correct installation and protection rests with the body manufacturer, at least as far as operators are concerned.
Perhaps if all body manufacturers had comprehensive questionnaires available for prospective customers to ascertain their exact requirements, as recommended in the Royal Society of Health Code of Practice, then it is possible that a large number of problems raised above, would be overcome.
Construction and performance
So often the operator dictates the type of body construction along with the plant. This can place a tremendous handicap on the manufacturer who must conform to individual requirements or lose an order. Many operators look for the cheapest equipment initially, or are loathe to change material specification and design, placing repeat orders while not being fully aware, it would seem, of extra cost which can be incurred in the long run.
Manufacturers of insulated bodies could bring pressure to bear by persuasion and advice, with some realistic costings, on the advantages of a superior construction with the right type of plant. Willingness to give guarantees on bodies would help here. Who would buy a new commercial vehicle (or a domestic refrigerator for that matter) without a guarantee? Bodybuilders need more faith in their product which has no moving parts except doors ignoring any plant that is fitted and which is covered by the plant manufacturer—so surely at least a three-year guarantee could be offered.
Secondly, the operator can stress the need for a guaranteed thermal performance and insist on improvement in details. A tour of the insulated /refrigerated vehicle bodies and containers at Earls Court showed unsealed holes in the inner skins revealing the insulant, unsealed floor joints, poor door seals, metal door and portal frames.
Water vapour transmission through insulants is another littletalked-of problem. Claims are made by insulant manufacturers and repeated by bodybuilders that modern insulants (polyurethanes) do not absorb water. Technical information available shows that in fact they will transmit moisture vapour, and I know that bodies insulated with polystyrene and polyurethane have been found to contain tremendous quantities of water, although vapour seals have been applied.
One company is advertising expanded rubber apparently with the rightful claim that it has the lowest water vapour transmission rate. Of course, the body manufacturer is in the hands of the individual who applies the vapour-seal, but it seems to be a problem which management need to be more aware of and need to take positive design /production steps to overcome.
Floors are usually, the most vulnerable areas for moisture ingress, and the one-piece moulded glassfibre tray flooring has done much to improve the situation in preventing water inside the body from draining through to the insulant. But just as much attention needs to be given to all external surfaces and here it would seem that the moulded glassfibre body wins hands down.
Resin-impregnated glassfibre skinned bodies and containers have come to the fore in the past two years, but tend to be relatively expensive and heavy. Operators look forward to the time when investigation and development will reduce the weight and cost, perhaps by employing extruded glassfibre and insulated wall sections and mounting the running gear directly on to the container base in the case of bulk transport with non-demountable containers.
And if these have a life of at least 10 years, with perhaps no more than five per cent increase in heat flow during their life, one can be reasonably sure of operating a relatively efficient body by the time replacement is due.
These bodies are highly efficient but to cut a large aperture in the body to accommodate the refrigeration plant is wrong in principle and should be avoided if possible; also meticulous care has to be exercised in ensuring that the aperture is sealed 100 per cent against moisture ingress, although the wise designer would have the aperture moulded in during manufacture.
Thermal tests
The publication of the Royal Society of Health Code of Practice which includes the testing of insulated bodies and containers, is a great asset in bringing about some uniformity in the refrigerated transport field. At least the operator has now some idea of what is involved and what to expect. It would seem, though, that more manufacturers need to submit their vehicle bodies and containers for testing, backed up by a guarantee, for every insulated body constructed.
Refrigeration in any form is costly, so such testing can be an asset to the operator, enabling him to shop around, and it can be a selling force for the manufacturer. It may be pertinent to ask how the result from the thermal test in a chamber carried out under static conditions compares with the heat ingress when the vehicle is moving and what materials and methods of construction affect this.
Some information on this is available from tests carried out several years ago in America on containers, considered to be of good construction, but which, undoubtedly, are considerably inferior to what is now available in this country.
It is gratifying to realize that more and more bodybuilders are speaking of thermal performance in heat units and not in thermal efficiency. Unfortunately, however, thermal efficiency is still too frequently used. Apart from the often presented arguments that thermal efficiency relates to the particular body referred to, it can mislead operators into thinking a body with the highest thermal efficiency must of necessity have the lowest heat flow.
There are other reasons which, again, do not appear to be widely known to insulated body manufacturers. Expanded polyurethane ages, i.e., its thermal conductivity ("k" value) varies (increases) with time; also it varies with temperature but not linearly. Some data is available on both ageing and temperature. Although a few figures are shown below, it should be noted that these relate to one size of slab only. The greater the volume/ surface area ratio, the less overall ageing occurs; the greater the cut surface, so ageing will increase.
A 12 in. by 12 in. by 2 in. slab of expanded polyurethane at mean temperature of 26°C will age as follows:—
new 0.130 30 days old 0.140 (+ 7.7%) 60 days old 0.144 (-F 10.8%) 90 days old 0.149 (-I14.6%) If the temperature of the insulant fluctuates while in stock, the ageing rate increases. By considering these figures, if a body is constructed of slab stock it is readily obvious that a thermal efficiency can be calculated that will vary itself by a considerable percentage, and who can state at what condition the insulant is fitted into the body structure?
The "k" value also varies with density. If the insulant is bought in slab form reasonable consistency can be expected but this usually means storing the insulant for some time. If the foam is dispensed from a machine in the body shop, less control can be exercised over the operator and foam dispensed, giving rise to greater variation in density and, therefore, in initial thermal conductivity although, virtually, no ageing will have occurred if a thermal conductivity test is carried out on the body when new.
It is all too easy to criticize another's achievements. The purpose of this article is to point out some of the problems confronting refrigerated transport operators of which many manufacturers are not aware.
In conclusion, this can be said: materials and design of insulated bodies have progressed tremendously over the past few years and manufacturers with foresight have tried to keep abreast with new developments. It is hoped that more insulated body manufacturers will take advantage of the progress made in the industry and employ qualified refrigeration engineers but, at the same time, pay more attention to detail and the problems confronting the operator.