BUIL1 )NE-PIECE IN PLASTICS
Page 38
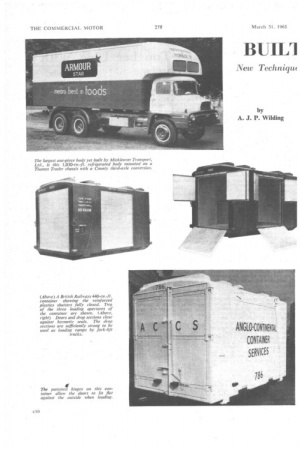
Page 39
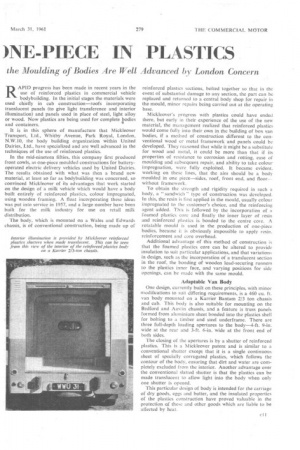
Page 40
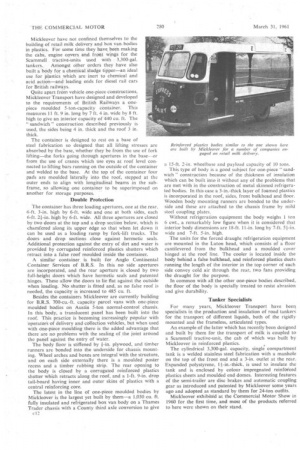
If you've noticed an error in this article please click here to report it so we can fix it.
New Techniqut
the Moulding of Bodies Are Well Advanced by London Concern RAPID progress has been made in recent years in the use of reinforced plastics in commercial vehicle bodybuilding. In the initial stages the materials were used chiefly in cab construction—roofs incorporating translucent panels (to give light transference and interior illumination) and panels used in place of steel, light alloy or wood. Now plastics are being used for complete bodies and containers.
It is in this sphere of manufacture that Mickleover Transport, Ltd., Whitby Avenue, Park Royal, London, N.W.10, the body building organization within United Dairies, ,Ltd., have specialized and are well advanced in the techniques of the use of reinforced plastics.
In the mid-nineteen fifties, this company first produced front cowls, as one-piece moulded constructions for batteryoperated electric delivery vehicles used by United Dairies. The results obtained with what was then a brand new material, at least so far as bodybuilding was concerned, so convinced Mickleover of its advantages that work started on the design of a milk vehicle which would have a body built entirely of reinforced plastics, colour impregnated, using wooden framing. A float incorporating these ideas was put into service in 1957, and a large number have been built for the milk industry for use on retail milk distribution.
The body, which is mounted on a Wales and Edwards chassis, is of conventional construction, being made up of
reinforced plastics sections, bolted together so that in the event of substantial damage to any section, the part can be replaced and returned to a central body shop for repairin the mould, minor repairs being carried out at the operating base.
Mickleover's progress with plastics could have ended there, but early in their experience of the use of the new material, the management realized that reinforced plastics would come fully into their own in the building of box van bodies, if a method of construction different to the conventional wood or metal framework and panels could be developed. They reasoned that while it might be a substitute for wood and metal, it could be more than that if its properties of resistance to corrosion and rotting, ease of moulding and subsequent repair, and ability to take colour impregnation, were fully exploited. It became evident. working on these lines, that the aim should be a body moulded in one piece—sides, roof, front end, and floor-without framework.
To obtain the strength and rigidity required in such a body, a " sandwich " type of construction was developed. In this, the resin is first applied in the mould, usually colour impregnated to the customer's choice, and the reinforcing agent added. This is followed by the incorporation of a foamed plastics core and finally the inner layer of resin and reinforced plastics is. bonded to the centre core. A rotatable mould is used in the production of one-piece bodies, because it is obviously impossible to apply resin. reinforcement and core overhead.
Additional advantage of this method of construction is that the foamed plastics core can be altered to provide insulation to suit particular applications, and that variations in design, such as the incorporation of a translucent section in the roof, the bonding of wooden load-securing runners to the plastics inner face, and varying positions for side openings, can be made with the same mould.
Adaptable Van Body
One design, currently built on these principles, with minor modifications to suit differing requirements, is a 460 cu. ft. van body mounted on a Karrier Bantam 2/3 ton chassis and cab. This body is also suitable for mounting on the Bedford and Austin chassis, and a feature is truss panels formed from aluminium sheet bonded into the plastics shell for bolting to a timber and steel underframe. There are three full-depth loading apertures to the body-4-ft. 9-in: wide at the rear and 3-ft. 6-in, wide at the front end of both sides.
The closing of the apertures is by a shutter of reinforced plastics. This is a Mickleover patent and is similar to a conventional shutter except that it is a single continuous sheet of specially corrugated plastics, which follows the contour of the body, ensuring that dirt and water are completely excluded from the interior. Another advantage over the conventional slatted shutter is that the plastics can be made translucent to allow light into the body when only one shutter is opened.
This particular design of body is intended for the carriage of dry goods, eggs and butter, and the insulated properties of the plastics construction have proved valuable in the protection of these and other goods which are liable to be affected by heat.
Mickleover have not confined themselves to the building of retail milk delivery and box van bodies in plastics. For some time they have, been making the cabs, engine covers and front wings for the Seammell tractive-units used with 3,300-gal. tankers. Amongst Other orders they have also built a`body for a chemical sludge tipper—an ideal use for plastics which are inert to chemical and acid action—and-leading ends for diesel rail cars for British railways. Quite apart from vehicle one-piece constructions, Mickleover Transport have designed and developed to the requirements of British Railways a onepiece moulded 5-ton-capacity container. This measures 11 ft. 9 in. long by 7 ft. 4 in. wide by 8 ft. high to give an interior capacity of 440 Cu. ft. The " sandwich " construction described previously is used, the sides being 4 in. thick and the roof 3 in. thick.
The container is designed to rest on a base of steel fabrication so designed that all lifting stresses are absorbed by the base, whether they be from the use of fork lifting—the forks going through apertures in the base—or from the use of cranes which Use eyes at roof level connected to lifting bars running on the outside of the container arid welded to the base. At the top of the container four pads are moulded laterally into the roof, stepped at the outer ends to align with longitudinal beams in the subframe, so allowing one container to be superimposed on another for storage purposes.
Double Protection
The container has three loading apertures, one at the rear, 6-ft. 3-in, high by 6-ft. wide and one at both sides, each 6-ft. 24--in, high by 6-ft. wide. All three apertures are closed by two doors at the top and a drop section below, which is chamfered along its upper edge so that when let down it can be used as a loading ramp by fork-lift trucks. The doors and drop sections close against hermetic seals. Additional protection against the entry of dirt and water is provided by corrugated reinforced plastics shutters which retract into a false roof moulded inSide the container.
A similar container is built for Anglo Continental Container Services of B.R.S. In this no side apertures are incorporated, and the rear aperture is. closed by two full-height doors which have hermetic seals and patented hinges. These allow the doors to lie flat against the outside when loading. No shutter is fitted and, as no false roof is needed, the capacity is increased to 485 cu. ft.
Besides the containers Mickleover. are currently building for B.R.S. 700-cu.-ft. capacity parcel vans with one-piece moulded bodies on Austin 5-ton normal-control chassis. In this body, a translucent panel has been built into the roof. This practice is becoming increasingly popular with operators of delivery and collection vehicles, but when used with One-piece moulding there is the added advantage that there are no problems with the sealing of the joint around the panel against the entry of water.
The body floor is stiffened by fin, plywood, and timber runners are bonded into the underside for chassis mounting. Wheel arches and boxes are integral with the structure, and on each side externally there is a moulded poster recess and a timber rubbing strip. The rear opening to the body is closed by a corrugated reinforced plastics shutter which retracts along the roof, and a I-ft. 9-in, drop tail-board having inner and outer skins of plastics with a central reinforcing core.
The latest in the line of one-piece moulded bodies by Mickleover is the largest yet built by them—a 1,030 Cu. ft. fully insulated and refrigerated box van body on a Thames Trader chassis with a County third axle conversion to give
cl 2
a 15-ft. 2-in, wheelbase and payload capacity of 10 tons. This type of body is a good subject for one-piece " sandwich " construction because of the thickness of insulation which can be built into it without any of the problems that are met with in the construction of metal skinned refrigerated bodies. In this case a 3-in.-thick layer of foamed plastics is incorporated in the roof, sides, front bulkhead and floor. Wooden body mounting runners are bonded to the underside and these are attached to the chassis frame by mild steel coupling plates.
Without refrigeration equipment the body weighs 1 ton 6 cwt., a remarkably low figure when it is considered that interior body dimensions are 18-ft. 11-in, long by 7-ft. 51-in. wide and 7-ft. 5-in. high.
The units for the forced draught refrigeration equipment are mounted in the Luton head, which consists of a floor cantilevered from the bulkhead and a moulded cover hinged at the roof line. The cooler is located inside the body behind a false bulkhead, and reinforced plastics ducts running the length of the interior in the top corner of each side convey cold air through the rear, two fans providing the draught for the purpose.
In common with all the other one-piece bodies described, the floor of the body is specially treated to resist abrasion and give durability, Tanker Specialists
For many years, Mickleover Transport have been specialists in the production and insulation of road tankers for the transport of different liquids, both of the rigidly mounted and the frameless, articulated types.
An example of the latter which has recently been designed and built by them for the transport of milk is coupled to Scammell tractive-unit, the cab of which was built by Mickleover in reinforced plastics.
The cylindrical 3,300-gal. capacity, single compartment tank is a welded stainless steel fabrication with a manhole on the top of the front end and a 3-in, outlet at the rear. Expanded polystyrene, 14--in.-thick, is used to insulate the tank and is enclosed by colour impregnated reinfofced plastics sheets and moulded end domes. Interesting features of the semi-trailer are disc brakes and automatic coupling gear as introduced and patented by Mickleover some years ago and adopted as standard by them for 24-ton outfits.
Mickleover exhibited at the Commercial Motor Show in 1960 for the first time, and most of the products referred to here were shown on their stand.