How Australia Makes Producer Charcoal
Page 28
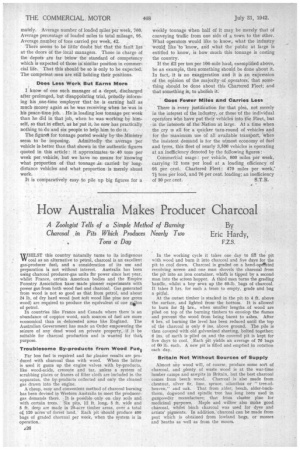
If you've noticed an error in this article please click here to report it so we can fix it.
WHILST this country naturally turns to its indigenous coal as an alternative to petrol, charcoal is an excellent gas-producer fuel; and a consideration of its use and preparation is not without interest. Australia has been using charcoal producer-gas units for power since last year, whilst France, certain American bodies and the Empire Forestry Association have made pioneer experiments with power gas from both wood fuel and charcoal. Gas generated from wood is not so good as that from petrol, and about 24 lb. of dry hard wood (not Soft wood like pine nor green wood) are reqnired to produce the equivalent of one gilon of .petrol.
In countries like France and Canada where there is an abundance of coppice wood, such sources of fuel are more economical than in deforested areas like England. The Australian Government has made an Order empowering the seizure of any dead wood on private property; if it be suitable for charcoal production and is wanted for that purpose.
Troublesome By-products from Wood Fuel Far less fuel is required and far ,cleaner results are pro" duced with charcoal than with wood. When the latter is used it gums up the engine valves with by-products, like wood-acids, creosote and tar, ,unless a .system of scrubbing plates or frames of filter cloth are included in the apparatus, the by-products collected and only the cleaned gas drawn into the engine.
A cheap, easy and convenient Method of charcoal burning has been devised in Western AuStralia to meet the producergas demands there. It is poasible only on clay soils and with certain trees. Six pits, 12 ft. long,5 ft. wide and 5 ft. deep are made in 20-acre timber areas, over a total of 120 atres-of forest land. Each pit should produce 400 bags of graded charcoal per week, when the system is in operation. In the working cycle it takes one day to fill the pit with wood and burn it into charcoal and five days for the pit to cool down. Charcoal is graded on a hand-opted revolving screen and one man shovels the charcoal from the pit into an iron container, which is tipped by a second man into the screen hopper. A third man turns the grading handle, whilst a boy sews up the 60-1b. bags of charcoal. It takes 3 hrs. for such a team to empty, grade and bag a pitful.
At the outset timber is stacked in the pit to 4 ft. above the surface, and lighted fromthe bottom. It ii allowed to burn for 21 hrs., when smaller lengths of wood are piled on top of the burning timbers -to envelop the flames and prevent the wood from being burnt to ashes. After 6 hrs. of burning the level has been reduced until the top of the charcoal is only 6 ins, above ground. The pile is then covered with old galvanized sheeting, bolted together; 6 ins, of earth is piled on and the covered pit is kept for five days to cool. Each pit yields an average of 70 bags of 80 lb. each. A new pit is filled and emptied in rotation each day.
Britain Not Without Sources of Supply Almost any wood will, of course, produce some sort of charcoal, and plenty of waste wood is at the war-time lumber camps and sawpits in Britain, but the best charcoal comes from beech wood. Charcoal is also made from chestnut, silver fir, lime, spruce, ailanthus or " tree-ofheaven," and oak. That from alder, beech, alder-buckthorn, dogwood and spindle tree has long been used in gunpowder manufacture; that from cluster pine for medicinal purposes. Maple and willow also make good charcoal, whilst birch charcoal was used for dyes and artists' pigments. In addition, charcoal can be made from peat which is obtained from lowland bogs, or mosses and heaths as well as from the moors.