Keep bolt holes tight
Page 35
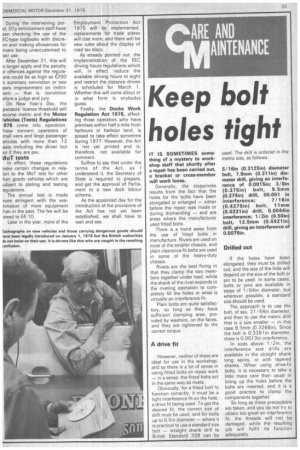
If you've noticed an error in this article please click here to report it so we can fix it.
IT IS SOMETIMES something of a mystery to workshop staff that shortly after a repair has been carried out, a bracket or cross-member will work loose.
Generally, the sloppiness results from the fact that the holes for the bolts have been elongated or enlarged — either before the repair was made or during dismantling — and are areas where the manufacturer used fitted bolts.
There is a trend away from the use of fitted bolts in manufacture. Rivets are used on most of the smaller chassis, and plain clearance-fit bolts are used in some of the heavy-duty chassis.
Rivets are the best fixing in that they clamp the two members together under load, while the shank of the rivet expands in the riveting operation to completely fill the holes in what is virtually an interference fit.
Plain bolts are quite satisfactory, so long as they have sufficient clamping area, provided by washers, on the faces, and they are tightened to the correct torque.
A drive fit
However, neither of these are ideal for use in the workshop, and so there is a lot of sense in using fitted bolts on repair work — in a sense, the fitted bolts act in the same way as rivets.
Obviously, for a fitted bolt to function correctly, it must be a light interference fit on the hole, a drive fit being used. To get the desired fit, the correct size of drill must be used, and for bolts up to 0.5in diameter — where it is practical to use a standard size bolt — straight shank drill to British Standard 328 can be If the holes have been elongated, they must be drilled out, and the size of the hole will depend on the size of the bolt or pin to be used. In some cases, bolts or pins are available in steps of 1/641n diameter, but wherever possible, a standard size should be used.
The approach is to use the bolt, of say, 21/64in diameter, and then to use the metric drill that is a size smaller — in this case 8.3mm (0.3268in). Since the bolt is 0.3281in diameter, there is 0.0013in interference.
In sizes above 1/2in, the interference size drills are available in the straight shank long series, or with tapered shanks. When using drive-fit bolts, it is necessary to take a little more care than usual in lining up the holes before the bolts are inserted, and it is a good practice to clamp the components together.
So long as these precautions are taken, and you do not try to obtain too great an interference fit, the threads will not be damaged, while the resulting job will fulfil its function adequately.