DEMOUNTABLE
Page 35
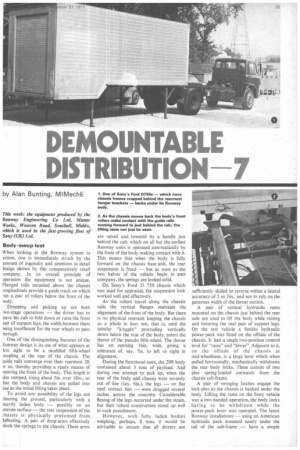
Page 36
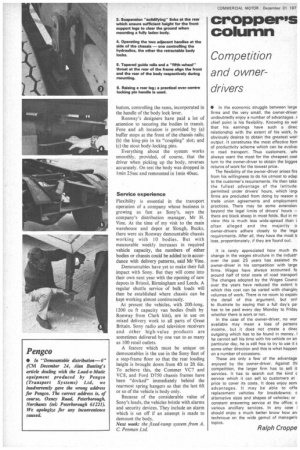
If you've noticed an error in this article please click here to report it so we can fix it.
DISTRIBUTION .7 by Alan Bunting, MIMechE
This week: the equipment produced by the Ronway Engineering Co Ltd, Manor Works, Western Road, Southall, Middx, which is used in the fast-growing fleet of Sony (UK) Ltd.
Body-swop test When looking at the Ronway system in lction, one is immediately struck by the mount of ingenuity and attention to detail iesign shown by this comparatively small ximpany. In its overall principle of veration the equipment is not unique. Flanged rails mounted above the chassis ongitudinals provide a guide track on which -un a pair of rollers below the front of the )ody.
Dropping and picking up are both .wo-stage operations — the driver has to cave his cab to fold down or raise the front )air of support legs, the width between them xing insufficient for the rear wheels to pass hrough.
One of the distinguishing features of the konway design is its use of what appears at irst sight to be a modified fifth-wheel :oupling at the rear or the chassis. The ;uide rails converge over their rearmost 2ft ir so, thereby providing a ready means of :entring the front of the body. This length is tlso ramped, rising about Sin, over 18in., so hat the body and chassis are pulled into me as the initial lifting takes place.
To avoid any possibility of the legs not :leafing the ground, particularly with a teavily laden body — possibly on an Eleven surface — the rear suspension of the :hassis is physically prevented from ieflecting. A pair of drop-arms effectively )lock the springs to the chassis. These arms are raised and lowered by a handle just behind the cab, which on all but the earliest Ronway units is operated automatically by the front of the body making contact with it. This means that when the body is fully forward on the chassis base-unit, the rear suspension is freed — but as soon as the two halves of the vehicle begin to part company, the springs are locked solid.
On Sony's Ford D 750 chassis which was used for appraisal, the suspension lock worked well and effectively.
As the rollers travel along the chassis rails the vertical flanges maintain the alignment of the front of the body. But there is no physical restraint keeping the chassis as a whole in line: not, that is. until the tubular "Ithigpin" protruding vertically down below the rear of the body, enters the throat of the pseudo fifth-wheel. The throat has an opening 16in. wide, giving a tolerance of, say, 7in. to left or right in alignment.
During the functional tests, the 20ft body contained about 3 tons of payload. And during one attempt to pick up, when the rear of the body and chassis were severely out of line (say, 6in.), the legs — on flat steel contact feet — were dragged several inches across the concrete. Considerable flexing of the legs occurred under the strain, but their robust construction stood up well to such punishment.
However, with fully laden bodies weighing, perhaps, 8 tons, it would be advisable to ensure that all drivers are sufficiently skilled to reverse within a lateral accuracy of 2 or 3in., and not to rely on the generous width of the throat section.
A pair of vertical hydraulic rams mounted on the chassis just behind the rear axle are used to lift the body while raising and lowering the rear pair of support legs. On the test vehicle a Smiths hydraulic power-pack was fitted on the offside of the chassis. It had a single two-position control level for "raise" and "lower". Adjacent to it, on the offside of the chassis at mid-wheelbase, is a large lever which when pulled horizontally, mechanically withdraws the rear body locks. These consist of two pins spring-loaded outwards from the chassis sub-frame.
A pair of swinging latches engage the lock-pins as the chassis is backed under the body. Lifting the rams on the Sony vehicle was a two-handed operation, the body locks having to be withdrawn while the power-pack lever was operated. The latest Ronway installations — using an American hydraulic pack mounted neatly under the tail of the sub-frame — have a simple button, controlling the rams, incorporated in the handle of the body lock lever.
Ronway's designers have paid a lot of attention to securing the bodies in transit. Fore and aft location is provided by (a) buffer stops at the front of the chassis rails; (b) the king-pin in its "coupling" slot; and (c) the stout body-locking pins.
Everything about the system works smoothly, provided, of course, that the driver when picking up the body, reverses accurately. On test the body was dropped in lmin 25sec and remounted in lmin 40sec.
Service experience Flexibility is essential in the transport operation of a company whose business is growing as fast as Sony's, says the company's distribution manager, Mr H. Vine. At the time of my visit to the main warehouse and depot at Slough. Bucks, there were six Ronway demountable chassis working with 10 bodies. But with measurable weekly increases in required vehicle capacity, the numbers of either bodies or chassis could be added to in accordance with delivery patterns, said Mr Vine.
Dernountables have yet to make their full impact with Sony. But they will come into their own next year with the opening of new depots in Bristol, Birmingham and Leeds. A regular shuttle service of bulk loads will then be established where chassis Can be
kept working almost continuously.
At present the vehicles, with 20ft-long, 1200 cu ft capacity van bodies (built by Ronway from Clark kits), are in use on mixed delivery work to all parts of Great Britain. Sony radio and television receivers and other high-value products are sometimes delivered by one van to as many as 100 retail outlets.
A feature which must be unique on demountables is the use in the Sony fleet of a step-frame floor so that the rear loading height is brought down from 4ft to 2ft 6in.
To achieve this, the Commer VC7 and VC8, and Ford D750 chassis frames have been "docked" immediately behind the rearmost spring hangers so that the last 6ft or so of the vehicle is body only.
Because of the considerable value of Sony's loads, the vehicles bristle with alarms and security devices. They include an alarm which is set off if an attempt is made to demount the body.
Next week: the fixed-ramp system from A.
C. Penman Ltd