7-cu.-yd. Tipper Under 3 Tons
Page 43
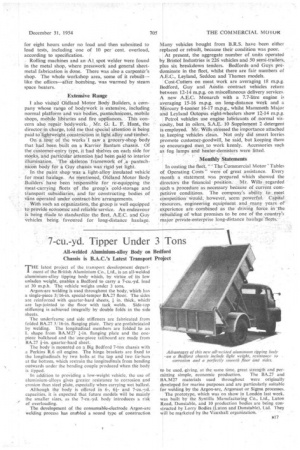
If you've noticed an error in this article please click here to report it so we can fix it.
All-welled Aluminium-alloy Body on Bedford Chassis is B.A.C.'s Latest Transport Project THE latest project of the transport development depart]. .rnent of the British Aluminium Co., Ltd., is an all-welded aluminium-alloy tipping body which, by virtue of its low unladen weight, enables a Bedford to carry a 7-cu.-yd. load at 30 m.p.h. The vehicle weighs under 3 tons.
Argon-arc welding is used throughout the body, which has a single-piece 3/16-in. special-temper BA.27 floor. The sides are reinforced with quarter-hard sheets, in. thick, which are lap-jointed to the floor with tack welds. Side-top stiffening is-achieved integrally by double folds in the side sheets.
The underframc and side stiffeners are fabricated from folded BA.27 3/16-in, flanging plate. They are prefabricated by welding. The longitudinal members are folded to an L shape from I3A.M27 1-in. flanging plate and the onepiece bulkhead and the 'one-piece tailboard are made from BA.27 1-in. .quarter-hard sheet.
The body is mounted on a Big Bedford 7-ton chassis with a Perkins R.6 oil engine. The hinge brackets are fixed to the longitudinals by two bolts at the top and two tie-bars at the bottom, which restrain the longitudinals from bending outwards under the bending couple produced when the body is tipped.
In addition to providing a low-weight vehicle, the use of aluminium-alloys gives greater resistance to corrosion and erosion than steel plate, especially when carrying wet ballast.
Although the body is offered in 6-, 612and 7-cu.-yd. capacities, it is expected that future models will be mainly the smaller sizes, as the 7-cu.-yd. body introduces a risk of overloading.
The development of the consumable-electrode Argon-arc welding process has enebled a sound type of construction
to be used, -giving, at the same time, great strength and per
mitting simple, economic production. The BA.27 and BA.M27 materials used throughout were originally developed for marine purposes and are particularly suitable for welding by the Argon-are, Argonaut or Sigma processes. The prototype, which was on show in LonclOri last week, was built by the Syntilla Manufacturing Co., Ltd., Luton Road, Dunstable, and 10 production bodies are being constructed by Lorry Bodies (Luton and Dunstable), Ltd. They
will be m4rketed by the Vauxhall organization.