Motorway Sub-contracting Ca
Page 46
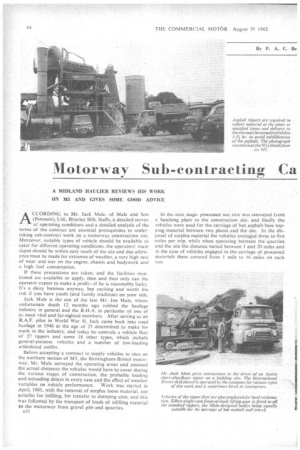
Page 47
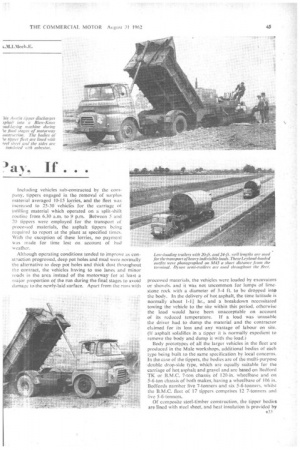
Page 48
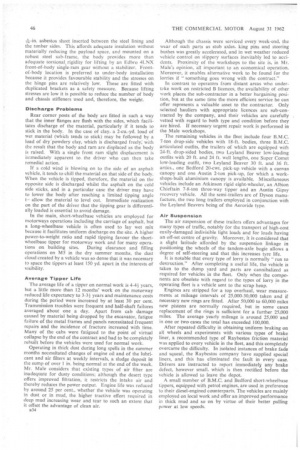
If you've noticed an error in this article please click here to report it so we can fix it.
If • •
A MIDLAND HAULIER REVIEWS HIS _WORK ON M5 AND GIVES SOME GOOD ADVICE ACCORDING to Mr. Jack Male, of Male and Son (Pensnett), Ltd., Brierley Hill, Staffs, a detailed survey of operating conditions and .a detailed analysis of the terms of the contract are essential prerequisites to undertaking .sub-contract work on a Motorway construction site. Moreover, suitable types of vehicle should be available to cater for different operating conditions, the operators' main depot should be within easy reach of the site and due allowance must be made for extremes of weather, a very high rate of wealand tear on the engine, chassis and bodywork and a high fuel consumption.
If these precautions are taken, and the facilities mentioned are available or apply, then and then only can the operator expect to make a profit—if he is reasonably lucky. It's a dicey business anyway, but exciting and worth the risk if you have youth (and family tradition) on your side.
Jack Male is the son of the late Mr. Joe Male, whose unfortunate death 12 months ago robbed the haulage industry in general and the R.H.A. in particular of one of its most vital and far-sighted members. After serving as an R.A.F. pilot in World War 11. Jack came back into road haulage in 1946 at the age of 23 determined to make his mark in the industry, and today he controls a vehicle fleet of 27 tippers and some 18 other types, which include general-purpose vehicles and a number of low-loading articulated outfits.
Before accepting a contract to supply vehicles to sites on the northern section of M5, the Birmingham-Bristol motorway. Mr. Male surveyed the operating areas and assessed the actual distances the vehicles would have to cover during the various stages of construction, the probable loading and unloading delays in every case and the effect of weather variables on vehicle performance. Work was started in April, 1961, with the removal of surplus loose material, not suitable for infilling, for transfer to dumping sites, and this 'as followed by the transport of loads of infilling material to the motorway from gravel pits and quarries. 1)32 In the next stage. processed wet mix was conveyed from a batching plant to the construction site, and finally the vehicles were used for the carriage of hot asphalt-base topping material between two plants and the site. In the disposal of surplus material the vehicles averaged three to five miles per trip, whita when operating between the quarries. and the site the distance varied between 1 and 20 miles and in the case of vehicles engaged in. the carriage of processed materials these covered from 1 mile to 16 miles on each run,
Including vehicles sub-contracted by the company, tippers engaged in the removal Of surplus material averaged 10-15 lorries, and the fleet was increased to 25-30. vehieres for: the carriage of infilling material which operated on a split-shift routine from 6,30 a.m. to 9 p.m. Between 5 and 20 tippers were employed. for the transport of processed materials, the asphalt tippers being required to report at the plant at specified times. With the exception of these lorries, no payment was made for time lost on account of bad. weather.
Although operating conditions tended to improve as construction progressed, deep pot holes and mud were normally the alternative to deep pot holes and thick dust throughout the contract, the vehicles having to use lanes and minor roads in the area instead of the motorway for at least a major proportion of the run during the final stages to avoid damage to the newly-laid surface. Apart from the runs with processed materials, the vehicles were loaded by excavators or shovels, and it was not uncommon for lumps of limestone rock with a diameter of 3-4 ft. to be dropped into the body. In the delivery of hot asphalt, the time latitude is normally about 1-11 hr., and a breakdown necessitated towing the vehicle to the site within this period, otherwise the load would have been unacceptable on account of its reduced temperature. if a load was unusable the driver had to dump the material and the contractor claimed for its loss and any wastage of labour on site. (If asphalt solidifies in a tipper it is normally expedient to remove the body and dump it with the load.) Body prototypes of all the larger vehicles in the fleet are
produced in the Male workshops, additional bodies of each type being built to the same specification by local concerns. In the case of the tippers, the bodies are of the mufti-purpose double drop-side type, which are equally suitable for the carriage of iio asphalt and gravel and are based on Iledford TK or B.M.C. 7-ton chassis Of 120-in, wheelbase and on 5-6-ton chassis of both makes, having a wheelbase of 106 in. Bedfords number five 7-tonners and six 5.-6-tonners, whilst the B.M.C. fleet of 17 tippers comprises 12 7-tonners and
five 5-6-tormers.
Of composite steel-timber construction, the tipper bodies are lined with steel sheet, and heat insulation is provided by
asbestos sheet inserted between the steel lining and the timber sides. This affords adequate insulation without materially reducing the payload space, and mounted on a robust steel sub-frame, the body provides more than adequate torsional, rigidity for lifting by an Edbro 4LNX front-of-body single-ram gear without a stabilizer. Frontof-body location is preferred to under-body installation because it provides favourable stability and the stresses on the hinge pins are relatively low. These are fitted with duplicated brackets as a safety measure. Because lifting stresses are low it is possible to reduce the number of body and chassis stiffeners used and, therefore, the weight.
Discharge Problems Rear corner posts of the body are fitted in such a way that the inner flanges are flush with the sides, which facilitates discharge of the material, particularly if it tends to stick in the body. In the case of clay, a 2-cu.-yd. load of wet material (which tends to stick) may be followed by a load of dry 'powdery clay, which is discharged freely; with the result that the body and ram are displaced as the body is raised. With a single front ram slight displacement is immediately apparent to. the driver who can then take remedial action.
If a cold wind is blowing on to the side of an asphalt vehicle, it tends to chill the material on that side of the body. When the vehicle is tipped, therefore, the material on the opposite side is discharged whilst the asphalt on the cold side sticks, and in a particular case the driver may have to lower the body after reaching a limited tipping angle t,, allow the material to level out. Immediate realization on the part of the driver that the tipping gear is differentially loaded is essential to avoid damage.
In the main, short-wheelbase vehicles are employed for motorways operations including the carriage of asphalt, but a long-wheelbase vehicle is often used to lay wet mix because it facilitates uniform discharge on the site. A higher power-to-weight ratio and rapid tipping favour the shortwheelbase tipper for motorway work and for many opera tions on building sites. During clearance and filling operations on M5 in the dry summer months, the dust cloud created by a vehicle was so dense that it was necessary to space the tippers at least 150 yd. apart in the interests of visibility.
Average Tipper Life The average life of a tipper on normal work is 4-41 years, but a little more than 12 months' work on the motorway reduced life expectancy to 3-31 years and maintenance costs during the period were increased by at least 30 per cent. Transmission troubles were frequent and half-shaft failures averaged about one a day. Apart from cab damage caused by material being dropped by the excavator, fatigue failure of the metal frames and panels necessitated frequent repairs and the incidence of fracture increased with time. Many of the cabs were fatigued to the point of virtual collapse by the end of the contract and had to be completely rebuilt before the vehicles were used for normal work.
Operating in thick dust during long spells in the summer months necessitated changes of engine oil and of the lubricant and air filters at weekly intervals, a sludge deposit in the sump of over 1 in. being normal at the end of the week. Mr. Male considers that existing types of air filter are inadequate for dusty conditions; although the desert type offers improved filtration, it restricts the intake air and thereby reduces the power output. Engine life was reduced by around 25 per cent., whether the vehicle was operating in dust or in mud, the higher tractive effort required in deep mud increasing wear and tear to such an extent that it offset the advantage of clean air.
a34 Although the chassis were serviced every week-end, the wear of such parts as stub axles, king pins and steering bushes was greatly accelerated, and in wet weather reduced vehicle control on slippery surfaces inevitably led to accidents. Proximity of the workshops to the site is, in Mr. Male's opinion, all important to an economical operation. Moreover, it enables alternative work to be found for the lorries if " something goes wrong with the contract."
In contrast to operators from distant areas who undertake work on restricted B licences, the availability of other work places the sub-contractor in a better bargaining position, but at the same time the more efficient service he can offer represents a valuable asset to the contractor. Only selected hauliers with appropriate licences are sub-contracted by the company, and their vehicles are carefully vetted with regar'cl to both type and condition before they are hired. If necessary urgent repair work is performed in the Male workshops.
The remaining vehicles in the fleet include four B.M.C. 7-ton drop-side vehicles with 18-ft. bodies, three B.M.C. articulated outfits, the trailers of which are equipped with 24-ft. drop-sided bodies, two Leyland Beaver low-loading outfits with 20 ft. and 24 ft. well lengths, one Super Comet low-loading outfit, two Leyland Beaver 30 ft. and 36 ft. attics,, one Bedford 20-cwt. pick-up vehicle with a canvas canopy and one Austin 2-ton pick-up, for which a workshops-built aluminium canopy is available. Miscellaneous vehicles include an Atkinson rigid eight-wheeler, an Albion Chieftain 7-8-ton three-way tipper and an Austin Gipsy recovery vehicle. All the semi-trailers are of Dyson manufacture, the two long trailers employed in conjunction with the Leyland Beavers being of the Aeroride type.
Air Suspension The air suspension of these trailers offers advantages for many types of traffic, notably for the transport of high-cost easily-damaged indivisible light loads and for loads having an off-set centre of gravity. Moreover, it is considered that a slight latitude afforded by the suspension linkage in positioning the wheels of the tandem-axle bogie allows a degree of self-steering and that this increases tyre life.
It is notable that every type of lorry is normally "run to destruction." After completing a useful life, the vehicle is taken to the dump yard and parts are cannibalized as required for vehicles in the fleet. Only when the components are obsolete with regard to the types of lorry in the operating fleet is a vehicle sent to the scrap heap. • Engines are stripped for a top overhaul, wear measurements at mileage intervals of 25,000-30,000 taken and if necessary new rings are fitted. After 50,000 to 60,000 miles new pistons are normally required, but in some cases replacement of the rings is sufficient for a further 25,000 miles. The average yearly mileage is around 25,000 and in one or two cases the total has exceeded 100,000.
After repeated difficulty in obtaining uniform braking on all wheels and experiments with various types of brake liner, a recommended type of Raybestos friction material was applied to every vehicle in the fleet, and this completely overcame the difficulty. In isolated instances of brake fade and squeal, the Raybestos company have supplied special liners, and this has eliminated the fault in every case. Drivers are instructed to report immediately any brake defect, however small, which is then rectified before the vehicle is allowed to leave the depot.
A small number of B.M.C. and Bedford short-wheelbase tippers, equipped with petrol engines, are used in preference to their diesel-engined counterparts. The vehicles are mainly employed on local work and offer an improved performance in thick mud and so on by virtue of their better pulling power at low speeds.