TAKE A PRE-VIEW OF MORF -COMMERCIAL PRODUCTION
Page 46
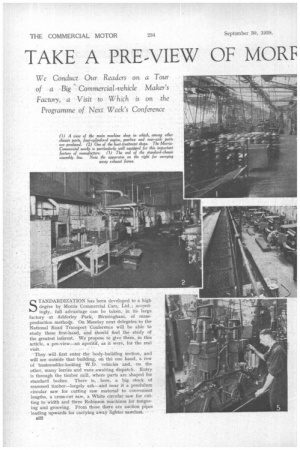
Page 47
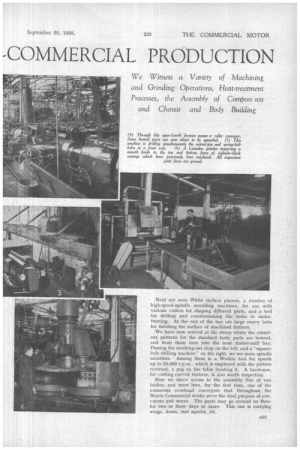
Page 48
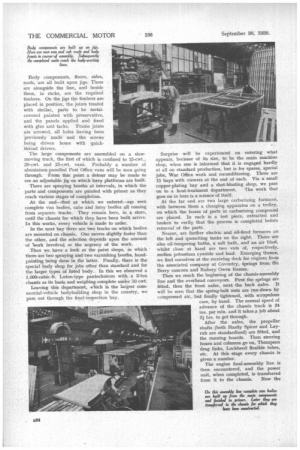
Page 49
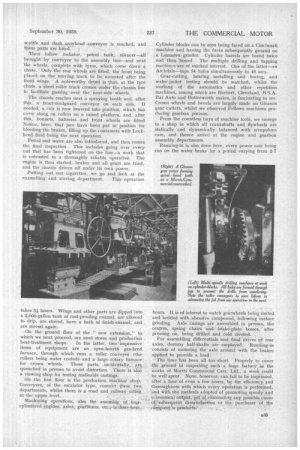
If you've noticed an error in this article please click here to report it so we can fix it.
STANDARDIZATION has been developed to a high degree by Morris Commercial Cars, Ltd.; accordingly, full advantage can be taken, in its large factory at Adderley Park, Birmingham, of massproduction methods. On Monday next delegates to the National Road Transport Conference will be able to study these first-hand, and should find the study of the greatest interest. We propose to give them, in this article, a pre-view—an aperitif, as it were, for the real
visit. .
--They. will first enter the body-building section, and will see outside 'that building, on the one hand, a row of businesslike-looking W.D. vehicles and, on the other, many lorries and vans awaiting dispatch. Entry is through the timber mill, where parts are shaped for standard bodies. There is, , here, a big stock of seasoned timber—largely ash—and near it a pendulum circular saw for cutting raw material to convenient lengths, a cross-cut saw, a White circular saw for cutting to width and three Robinson machines for tongueing and grooving. From these there are suction pipes leading upwards for carrying away lighter sawdust.
B32 Next are seen White surface planers, a number oi high-speed-spindle moulding machines, for use with various cutters for shaping different parts, and a tool for drilling and countersinking the holes in underframing. At the end of the bay are large emery bobs for finishing the surface of machined timbers.
We have now arrived at the stores where the numer• ous patterns for the standard body parts are housed, and from them turn into the next timber-mill bay. Passing the marking-out shop on the left, and a "squarehole drilling machine" on the right, we see more spindle moulders. Among these is a Watkin tool for speeds up to 24,000 r.p.m., which is employed with the pattern reversed, a peg on the table locating it. A band-saw, for cutting curved timbers, is also worth inspection.
Now we move across to the assembly line of van badies, and meet here, forthe first time, one of the numerous overhead conveyors that throughout the Morris Commercial works serve the dual purpose of conveyors and stores. The parts may go around on these for two or three days or more. This one is carryfng wings, doors, seat squabs, etc.
Body components, floors, sides, roofs, are all built upon jigs. These are alongside the line, and beside them, in racks, are the required timbers. On the jigs the timbers are placed in position, the joints treated with shellac, parts to be metalcovered painted with preservative, and the panels applied and fixed with glue arid tacks. Frame joints are screwed, all holes having been previously made and the screws .being driven home with quickthread drivers.
The large components are assembled on a slowmoving track, the first of which is confined to 15-cwt., 20-cwt. and 25-cwt. vans. Probably a number of aluminium-Panelled Post Office vans will be seen going through. From this point a detour may be made to see an adjustable jig on which lorry platforms are built. There are spraying booths at intervals, in which the parts and components are painted with primer as they reach various stages of completion.
At the end—that at which we entered—are seen complete van bodies, cabs and lorry bodies all coming from separate tracks. They remain here, in a store, until the chassis for which they have been built arrive. In this works, every vehicle is made to order.
In the next bay there are two tracks on which bodies are mounted on chassis. One moves slightly faster than the other, and the selection depends upon the amount of Work involved or the urgency of the work.
Then we have a look at the paint shops, in which there are two spraying and two varnishing booths, handpainting being done in the latter. Finally, there is the special body shop for jobs other than standard and for the larger types of listed body.. In this we observed a 1,000-cubic-ft. Luton-type pantechnicon with a 3-ton chassis as its basis and weighing complete under 50 cwt.
Leaving this department, which is the largest commercial-vehicle bodybuilding shop in the country, we pass out through the final-inspection bay. Surprise will be experienced on entering what appears, because of its size, to be the main machine shop, when one is informed that it is engaged hardly at all on standard production, but is for spares, special jobs, War Office work and reconditioning. There are 15 bays with viewers at the end of each. Via a small copper-plating bay and a shot-blasting shop, we pass on to a heat-treatment department. The work that goes on in here is a science of itself. At the far end are two large carburizing furnaces, with between them a charging apparatus on a trolley, on which the boxes of parts in carburizing compound are placed. In each is a test piece, extracted and broken to verify that the process is completed before removal of the parts.
Nearer, are further electric and oil-fired furnaces on the left and quenching tanks on the right. There are also oil-tempering baths, a salt bath, and an air blast, whilst close at hand are two vats of, respectively, molten potassium cyanide and lead. Emerging thence, we find ourselves at the receiving deck for engines from the associated company at Coventry, prings frOrn the Berry concern and Rubery Owen frames.
Then we reach the beginning of the chassis-assembly line and the overhead conveyors. First the springs are fitted, then the front axles, next the back axles_ It will be seen that the spring-bolt nuts are run-down by compressed air, but finally tightened, with scrupulous care, by hand. The normal speed of advance of the chassis track is 24 ins, per min. and it takes A job about 3i hrs. to get through.
After the axles, the propeller shafts (both Hardy Spicer and Layrub are standardized) are fitted, and the running boards. Then steering boxes and columns go on, Thompson drag links, Lockheed flexible tubes, etc. At this stage every chassis is given a number.
The engine final-assembly line is then encountered, and the power unit, when completed, is transferred from it to the chassis. Now the scuttle and dash overhead conveyor is reached, and these parts are fitted.
Then follow radiator, petrol tank, silencer—all brought by conveyor to the assembly line—and next the wheels, complete with tyres, which come down a chute. Only the rear wheels are fitted, the front being placed on the moving, track to be mounted after the front wings. A noteworthy detail is that, at the tyre chute, a shrift roller track crosses under the chassis line to facilitate passing over the• near-side wheels.
The chassis reaches. next a spraying booth and, after this, a front-mudguard conveyor on each side. If needed, a cab is now lowered into position, which has come along. on rollers on a raised platform, and, after this, bonnets, batteries and front wheels are fitted Notice; here, that jarshave been put in position for bleeding the brakes, filling up the containers with Lockheed fluid being the next operation.
Petrol and water are also introduced, and then comes the final inspection. This includes going over .every nut that has been tightened on the line—a work that is entrusted to a thoroughly reliable operative. The engine is then started, brakes and all gears are tried, and the chassis driven off under its own power.
Putting out our cigarettes, we go and look at the enamelling and stoving department. This operation takes 51 hours. Wings and other parts are dipped into a 2,000-gallon tank of rust-proofing enamel, are allowed to drip, are stoved, have a bath of finish-enamel, and are staved again.
On the ground floor of the " new extension," to which we next proceed, are steel stores and production heat-treatment shops. In the latter, two impressive items of equipment are an open-hearth gas-fired furnace, through which runs a roller conveyor (the rollers being water cooled) and a large rotary furnace for crown wheels. These parts, . incidentally, are quenched in presses to avoid distortion. There is also a viewing shop for testing malleable castings.
On the first floor is the production machine shop. Conveyors, of the escalator type, connect these two departments, whilst there is a road and railway siding at.the upper. level.
Machining operations, also the assembly of fourcylindered engines',' axles, geariltates, etc.,. is done -here.
Cylinder blocks can be seen being faced on a Cincinnati machine and having the faces subsequently ground on a Lumsdeu grinder. Cylinder barrels are bored twice and then 'honed. The multiple drilling and tapping machines are of marked interest. One of the latter—an Archdale—taps 54 holes simultaneously in 45 secs.
Gear-cutting, bearing metalling and boring, and water-jacket testing should be watched, whilst the working of the automatics and other repetition machines, among which are Herbert, Cleveland, B.S.A. Bar Auto and Butterworth makes, is fascinating to see. Crown wheels and bevels are largely made on Gleason gear cutters, whilst we observed Fellows machines producing gearbox pinions.
From the countless bays of machine tools, we emerge to a shop in which all crankshafts and flywheels are statically and dynamically balanced with scrupulous care, and thence arrive at the engine and gearbox assembly departments.
Running-in is also done here, every power unit being run on the water brake for a period varying from 2-7 hours. It is of interest to watch gearwheels being mated and bedded with abrasive compound, 'following surface grinding. Axle casings are assembled in presses, the cerktres, spring chairs and brake-plate bosses, after pressing on, being drilled and cold riveted.
For assembling differentials and final drives of rear axles, dummy half-shafts are employed. Running-in consists of motoring the axle around with the brakes applied to provide a load.
The time has been all too short. Properly to cover the ground in inspecting such a huge factory, as the works of Morris Commercial Cars, Ltd., a Week could be well spent. None, however, can fail to be impressed, after a tour of even a few hours, by the efficiency and thoroughness with which every operation is performed, and with the methods adopted of promoting speedy and onomical output, 'yet oteliminatirrg any possible cause of. subsemient dissaAisfaZtion to the purchaser of the
comparly,:si products: • _