Definite trends in an indecisive year
Page 36
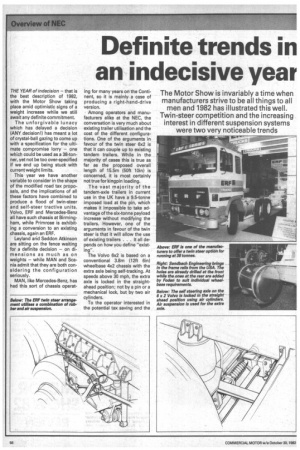
Page 37
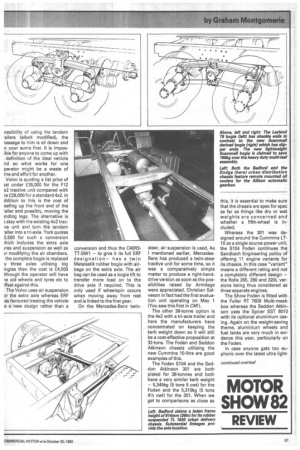
Page 38
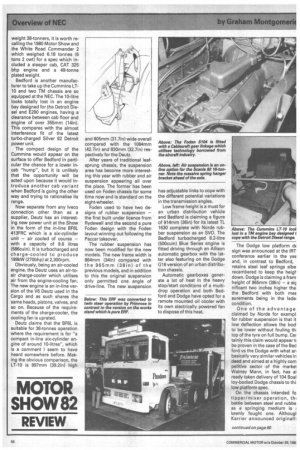
Page 40
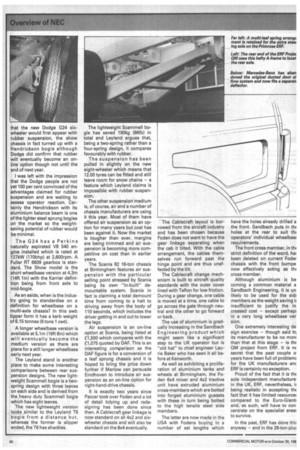
Page 41
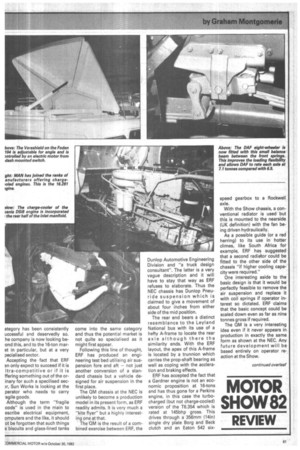
Page 42
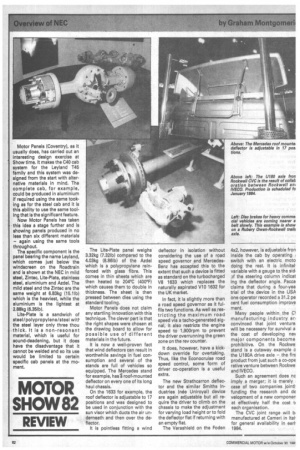
If you've noticed an error in this article please click here to report it so we can fix it.
THE YEAR of indecision — that is the best description of 1982, with the Motor Show taking place amid optimistic signs of a weight increase while we still await any definite commitment.
The unforgivable lunacy which has delayed a decision (ANY decision!) has meant a lot of crystal-ball gazing to come up with a specification for the ultimate compromise lorry — one which could be used as a 38-tonner, yet not be too over-specified if we end up being stuck with current weight limits.
This year we have another variable to consider in the shape of the modified road tax proposals, and the implications of all these factors have combined to produce a flood of twin-steer and self-steer tractive units. Volvo, ERF and Mercedes-Benz all have such chassis at Birmingham, while Primrose is exhibiting a conversion to an existing chassis, again an ERR Leyland arid Seddon Atkinson are sitting on the fence waiting for a definite decision — on dimensions as much as on weights — while MAN and Scania admit that they are both considering the configuration seriously.
MAN, like Mercedes-Benz, has had this sort of chassis operat ing for many years on the Continent, so it is mainly a case of producing a right-hand-drive version.
Among operators and manufacturers alike at the NEC, the conversation is very much about existing trailer utilisation and the cost of the different configurations. One of the arguments in favour of the twin steer 6x2 is that it can couple up to existing tandem trailers. While in the .. majority of cases this is true as far as the proposed overall length of 15.5m (50ft 10in) is concerned, it is most certainly not true for kingpin loading.
The vast majority of the tandem-axle trailers in current use in the UK have a 9.5-tonne imposed load at the pin, which makes it impossible to take advantage of the six-tonne payload increase without modifying the trailers. However, one of the arguments in favour of the twin steer is that it will allow the use
of existing trailers . . It all de,; pends on how you define "existing",
The Volvo 6x2 is based on a conventional 3.8m (12ft 6in) wheelbase 4x2 chassis with the extra axle being self-tracking. At speeds above 30 mph, the extra axle is locked in the straightahead position; not by a pin or a mechanical lock, but by two air cylinders.
To the operator interested in the potential tax saving and the ossibility of using his tandem 'tillers (albeit modified), the lessage to him is sit down and o your sums first. It is imposible for anyone to come up with definition of the ideal vehicle nd so what works for one perator might be a waste of me and effort for another.
Volvo is quoting a list price of ist under £35,000 for the F12 x2 tractive unit ccmpared with le £29,000 for a standard 4x2. In ddition to this is the cost of eefing up the front end of the .ailer and possibly, moving the mding legs. The alternative is ) stay with the existing 4x2 tracye unit and turn the tandem .ailer into a tri-axle. York quotes 2,500 for such a conversion fhich includes the extra axle tres and suspension as well as )r modifying the air chambers. the complete bogie is replaced y three axles utilising big ingles then the cost is £4,000 'though the operator will have le old wheels and tyres etc to ffset against this.
The Volvo uses air suspension Dr the extra axle whereas ERF as favoured treating the vehicle s a new design rather than a
conversion and thus the C40R3TT-SW1 — to give it its full ERF designation— has a twin Metalastik rubber bogie with airbags on the extra axle. The air bag can be used as a bogie lift to transfer more load on to the drive axle if required. This is only used if wheelspin occurs when moving away from rest and is linked to the first gear.
On the Mercedes-Benz twin steer, air suspension is used. As mentioned earlier, MercedesBenz has produced a twin-steer tractive unit for some time, so it was a comparatively simple matter to produce a right-handdrive version as soon as the possibilities raised by Armitage were appreciated. Christian Salveson in fact had the first evaluation unit operating on May 1 (You saw this first in CM!).
The other 38-tonne option is the 4x2 with a tri-axle trailer and here the manufacturers have concentrated on keeping the kerb weight down so it will still be a cost-effective proposition at 32-tons. The Foden and Seddon Atkinson chassis utilising the new Cummins 10-litre are good examples of this.
The Foden S104 and the Seddon Atkinson 301 are both plated for 38-tonnes and both have a very similar kerb weight 5,345kg (5 tons 5 cwt) for the Foden and the 5,310kg (5 tons 41/2 cwt) for the 301. When we get to comparisons as close as this, it is essential to make sure that the chassis are spec for spec as far as things like dry or wet weights are concerned and whether a fifth-wheel is included.
Whereas the 301 was designed around the Cummins LT10 as a single source power unit, the S104 Foden continues the Sandbach Engineering policy of offering 11 engine variants for its chassis. In this case "variant" means a different rating and not a completely different design — the Rolls 265, 290 and 320L versions being thus considered as three separate engines.
The Show Foden is fitted with the Fuller RT 7609 Multi-mesh box whereas the Seddon Atkinson uses the Spicer SST 8010 with its optional aluminium casing. Again on the weight-saving theme, aluminium wheels and fuel tanks are very much in evidence this year, particularly on the Foden.
In case anyone gets too euphoric over the latest ultra light weight 38-tonners, it is worth recalling the 1980 Motor Show and the White Road Commander 2 which weighed 6.18 tonnes (6 tons 2 cwt) for a spec which included a sleeper cab, CAT 325 bhp engine and a 49-tonne plated weight.
Bedford is another manufacturer to take up the Cummins LT10 and two TM chassis are so equipped at the NEC. The 10-litre looks totally lost in an engine bay designed for the Detroit Diesel and E290 engines, having a clearance between cab floor and engine of over 355mm (14in). This compares with the almost interference fit of the latest turbo-charged Silver 92 Detroit power unit.
The compact design of the Cummins would appear on the surface to offer Bedford in particular the chance for a lower incab "hump", but it is unlikely that the opportunity will be acted upon because it would introduce another cab variant when Bedford is going the other way and trying to rationalise its range.
Now separate from any Iveco connection other than as a supplier, Deutz has an interesting new power unit at the Show in the form of the in-line BF6L 413FRC which is a six-cylinder unit — air cooled of course — with a capacity of 9.6 litres (586cuin). It is turbocharged and charge-cooled to produce 199kW (270bhp) at 2,300rprn.
Obviously, being an air-cooled engine, the Deutz uses an air-toair charge-cooler which utilises air from the engine-cooling fan. The new engine is an in-line version of the V6 Deutz used in the Cargo and as such shares the same heads, pistons, valves, and so on. Because of the requirements of the charge-cooler, the cooling fan is uprated.
Deutz claims that the BF6L is suitable for 38-tonnes operation where the requirement is for "a compact in-line six-cylinder engine of around 10-litres", which is a comment I seem to have heard somewhere before. Making the obvious comparison, the LT-10 is 997mm (39.2in) high and 805mm (31.7in) wide overall compared with the 1084mm (42.7in) and 830mm (32.7in) respectively for the Deutz.
After years of traditional leafsprung chassis, the suspension area has become more interesting this year with rubber and air suspension appearing all over the place. The former has been used on Foden chassis for some time now and is standard on the eight-wheeler.
Foden used to have two designs of rubber suspension — the first built under licence from Rydewell and the second a pure Foden design with the Foden layout winning out following the Paccar takeover.
The rubber suspension has now been modified for the new models. The new frame width is 864mm (34in) compared with the 9 6 5mm (3 8in) of the previous models, and in addition to this the original suspension only permitted one angle of drive-line. The new suspension has adjustable links to cope with the different potential variations in the transmission angles.
Low frame height is a must for an urban distribution vehicle and Bedford is claiming a figure of 914mm (36in) for its latest TL 1630 complete with Norde rubber suspension as an SVO. The Bedford turbocharged 8.2-litre (500cuin) Blue Series engine is fitted driving through an Allison automatic gearbox with the latter also featuring on the Dodge G16 version of an urban distribu tion chassis.
Automatic gearboxes gener ate a lot of heat in the heavy stop/start conditions of a multidrop operation and both Bedford and Dodge have opted for a remote mounted oil cooler with its own electrically powered fan to dispose of this heat. The Dodge low platform dE sign was announced at the IRT conference earlier in the yea and, in contrast to Bedford, retains steel leaf springs albe recambered to keep the heigl down. Dodge is claiming a fram height of 965mm (38in) — a sig nificant two inches higher the' the Bedford with both mea surements being in the lade' condition.
One of the advantage
claimed by Norde for exampl, for rubber suspension is that it
low deflection allows the bod to be lower without fouling thi top of the tyre on full bump. Cer tainly this claim would appear ti be proven in the case of the Bed ford vs the Dodge with what an basically very similar vehicles in deed and aimed at a highly corn petitive sector of the market Watney Mann, in fact, has al ready taken delivery of 104 Boal loy-bodied Dodge chassis to thi. low platform spec.
On the chassis intended fo tipper/mixer operation, thi battle between steel and rubbe as a springing medium is keenly fought one. Althougl Karrier announced originalh that the new Dodge G24 sixwheeler would first appear with rubber suspension, the show chassis in fact turned up with a Hendrickson bogie although Dodge did confirm that rubber will eventually become an online option though not until the end of next year.
I was left with the impression that the Dodge people are not yet 100 per cent convinced of the advantages claimed for rubber suspension and are waiting to assess operator reaction. Certainly the Hendrickson with its aluminium balance beam is one of the lighter steel sprung bogies on the market so the weightsaving potential of rubber would be minimal.
The G24 has a Perkins naturally aspirated V8 540 engine installed which is rated at 127kW (170bhp) at 2,600rpm. A Fuller RT 6609 gearbox is standard. The Show model is the short wheelbase version at 4.3m 14ft lin) with the Karrier definition being from front axle to mid-bogie.
As an aside, when is the industry going to standardise on a definition for wheelbase on a multi-axle chassis? In this swb tipper form it has a kerb weight of 6.15 tonnes (6 tons 1 cwt).
A longer wheelbase version is available at 5.1m (16ft Bin) which will eventually become the medium version as there are plans for a still longer wheelbase early next year.
The Leyland stand is another place to make some interesting comparisons between rear suspension designs. The new lightweight Scammell bogie is a twospring design with three leaves on each side and is derived from the heavy duty Scammell bogie which has eight leaves.
The new lightweight version looks similar to the Leyland T6 bogie from a distance but, whereas the former is slipper ended, the T6 has shackles. The lightweight Scammell bogie has saved 190kg (861b) in total and Leyland argues that, being a two-spring rather than a four-spring design, it compares favourably with rubber.
The suspension has been pulled in slightly on the new eight-wheeler which means that 12.00 tyres can be fitted and still leave room for snow chains — a feature which Leyland claims is impossible with rubber suspension.
The other suspension medium is, of course, air and a number of chassis manufacturers are using it this year. Most of them have offered air suspension as an option for many years but cost has been against it. Now the market is tougher than ever, margins are being trimmed and air suspension is becoming more competitive on cost than in earlier years.
The Scania 82 16-ton chassis at Birmingham features air suspension with the particular selling point stressed by Scania being its own "in-built" demountable system. Scania in fact is claiming a total demount time from corning to a halt to driving away from the body of 110 seconds, which includes the driver getting in and out to lower the legs.
Air suspension is an on-line option at Scania, being listed at £1,500 which compares with the £1,075 quoted by DAF. This is an interesting comparison as the DAF figure is for a conversion of a leaf sprung chassis and it is hoped to bring the price down further if Marlow can persuade Eindhoven to introduce air suspension as an on-line option for right-hand-drive chassis.
It is exactly two years since Paccar took over Foden and a lot of detail tidying up and redesigning has been done since then. A Cablecraft gear linkage is now standard on all 4x2 and sixwheeler chassis and will also be standard on the 8x4 eventually. The Cablecraft layout is borrowed from the aircraft industry and has been chosen because Foden does not want tc have the gear linkage separating when the cab it tilted. With the cable arrangement, the cables themselves run forward past the hinge point and are thus unaffected by the tilt.
The Cablecraft change mechanism is built to aircraft quality standards with the outer cover lined with Teflon for low friction. During a gear change, one cable is moved at a time, one cable to go across the gate through neutral and the other to go forward or back.
The use of aluminium is gradually increasing in the Sandbach Engineering product which might seem like a significant step to the UK operator but is "old hat" to chief engineer Laurie Baker who has seen it all before at Kenworth.
As well as exhibiting a proliferation of aluminium tanks and wheels at Birmingham, the Foden 6x4 mixer and 4x2 tractive unit have extruded aluminium cross-members which are bolted into forged aluminium gussets with these in turn being bolted to the high tensile steel side members.
The latter are now made in the USA with Fodens buying in a number of set lengths which have the holes already drilled a the front. Sandbach puts in th( holes at the rear to suit th( operators' individual wheelbasi requirements.
The front cross member, in th( strict definition of the word, ha: been deleted on current Foder chassis with the front bumpe now effectively acting as th( cross member.
Although aluminium is be coming a common material a Sandbach Engineering, it is un likely to be used for the sid( members as the weight saving is insufficient to justify the in creased cost — except perhaps in a very long wheelbase ver sion.
One extremely interesting de sign exercise — though said b) its manufacturer to be no morc than that at this stage — is thE OM project from ERF. It is nc secret that the past couple o years have been full of problem: for the UK manufacturers anc ERF is certainly no exception.
Proud of the fact that it is thE sole independent manufacture' in the UK,. ERF, nevertheless, is being realistic in accepting thE fact that it has limited resources compared to the Euro-Giants and, as such, will have to con centrate on the specialist area: to survive. ategory has been consistently uccessful and deservedly so. he company is now looking beond this, and to the 16-ton maret in particular, but at a very pecialised sector.
Accepting the fact that ERF an only expect to succeed if it is We-competitive or if it is ffering something out of the orinary for such a specilised secN., Sun Works is looking at the perator who needs to carry .agile goods.
Although the term "fragile oods" is used in the main to escribe electrical equipment, omputers and the like, it should ot be forgotten that such things s biscuits and glass-lined tanks come into the same category and thus the potential market is not quite so specialised as it might first appear.
Following this line of thought, ERF has produced an engineering test bed utilising air suspension fore and aft — not just another conversion of a standard chassis but a vehicle designed for air suspension in the first place.
The QM chassis at the NEC is unlikely to become a production model in its present form, as ERF readily admits. It is very much a "kite flyer" but a highly interesting one at that.
The QM is the result of a combined exercise between ERF, the Dunlop Automotive Engineering Division and "a truck design consultant". The latter is a very vague description and it will have to stay that way as ERF refuses to elaborate. Thus the NEC chassis has Dunlop Pneuride suspension which is claimed to give a movement of about four inches from either side of the mid position.
The rear end bears a distinct resemblance to the Leyland National bus with its use of a hefty A-frame to locate the rear axle although there the similarity ends. With the ERF layout, the apex of this A-frame is located by a trunnion which carries the prop-shaft bearing as well as coping with the accleration and braking effects.
ERF has accepted the fact that a Gardner engine is not an economic proposition at 16-tons and has thus gone for a Perkins engine, in this case the turbocharged (but not charge-cooled) version of the T6.354 which is rated at 145bhp gross. This drives through a 356mm (14in) single dry plate Borg and Beck clutch and an Eaton 542 six speed gearbox to a Rockwell axle.
With the Show chassis, a conventional radiator is used but this is mounted to the nearside (UK definition) with the fan being driven hydraulically.
As a possible guide (or a red herring) to its use in hotter climes, like South Africa for example, ERF has suggested that a second radiator could be fitted to the other side of the chassis "if higher cooling capacity were required."
One interesting aside to the basic design is that it would be perfectly feasible to remove the air suspension and replace it with coil springs if operator interest so dictated. ERF claims that the basic concept could be scaled down even as far as nine tonnes gross if required.
The QM is a very interesting idea even if it never appears in production in exactly the same form as shown at the NEC. Any future development will be based entirely on operator reaction at the Show. Motor Panels (Coventry), as it usually does, has carried out an interesting design exercise at Show time. It makes the C40 cab system for the Leyland T45 family and this system was designed from the start with alternative materials in mind. The complete cab, for example, could be produced in aluminium if required using the same tooking as for the steel cab and it is this ability to use the same tooling that is the significant feature.
Now Motor Panels has taken this idea a stage further and is showing panels produced in no less than six different materials — again using the same tools throughout.
The specific component is the panel bearing the name Leyland, which comes just below the windscreen on the Roadtrain and is shown at the NEC in mild steel, Zintec, Lite-Plate, stainless steel, aluminium and Azdel. The mild steel and the Zintec are the same weight at 6.83kg (15.1Ib) which is the heaviest, while the aluminium is the lightest at 2.88kg (6.351b).
Lite-Plate is a sandwich of steel/polypropylene/steel with the steel layer only three thou thick. It is a non-resonant material, which is useful for sound-deadening, but it does have the disadvantage that it cannot be welded and so its use would be limited to certain specific cab panels at the moment. The Lite-Plate panel weighs 3.32kg (7.321b) compared to the 4.03kg (8.861b) of the Azdel which is a polypropylene reinforced with glass fibre. This comes in thin sheets which are then heated to 204°C (400°F) which causes them to double in thickness. The sheet is then pressed between dies using the standard tooling.
Motor Panels does not claim any startling innovation with this technique. The clever part is that the right shapes were chosen at the drawing board to allow for possible use of different materials in the future.
It is now a well-proven fact that wind deflectors can result in worthwhile savings in fuel consumption and several of the stands are full of vehicles so equipped. The Mercedes stand for example, hasi roof-mounted deflector on every one of its long haul chassis.
On the 1633 for example, the roof deflector is adjustable to 17 positions and was designed to be used in conjunction with the sun visor which ducts the air underneath and then over the deflector.
It is pointless fitting a wind deflector in isolation without considering the use of a road speed governor and MercedesBenz has accepted this to the extent that such a device is fitted as standard on the turbocharged V8 1633 which replaces the naturally aspirated V10 1632 for the UK market.
In fact, it is slightly more than a road speed governor as it fulfils two functions. As well as.restricting the maximum road speed via a tacho-generated signal, it also restricts the engine speed to 1,900rpm to prevent the driver overrunning the green zone on the rev counter.
It does, however, have a kickdown override for overtaking. Thus, like the Econocruise road speed control, some form of driver co-operation is a useful extra.
The new Strathcarron deflector and the similar Smiths Industries (née Uniroyal) device are again adjustable but all require the driver to climb on the chassis to make the adjustment for varying load height or to fold the deflector flat if returning with an empty flat.
The Varashield on the Foden
4x2, however, is adjustable fron inside the cab by operating switch with an electric moto doing the rest. It is infinite', variable with a gauge to the sidi ..)f the steering column indicat ing the deflector angle. Pacca claims that during a four-yea trial of the device in the USA one operator recorded a 31.2 pa cent fuel consumption improve ment.
Many people within the C‘ manufacturing industry an convinced that joint venture. will be necessary for survival a the cost of developing nev major components become prohibitive. On the Rockwel stand is a cutaway example o the U180A drive axle — the firs product from just such a co-ope rative venture between Rockwel and IVECO.
Such an agreement does no imply a merger; it is merely case of two companies joint funding the research and de velopment of a new componen at effectively half the cost ti each organisation.
The CVC joint range will bi manufactured at Cameri in 'tali for general availability in earl, 1984.