LETTING PROFITS LEAK AWAY
Page 56
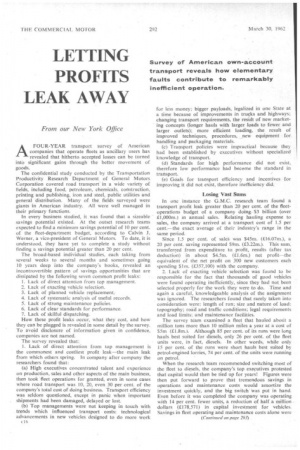
Page 61
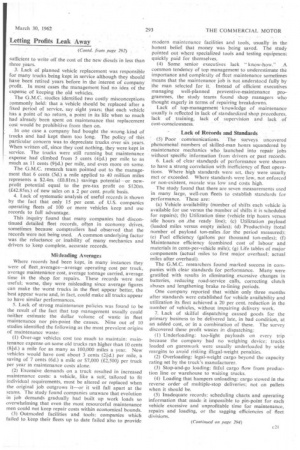
Page 62
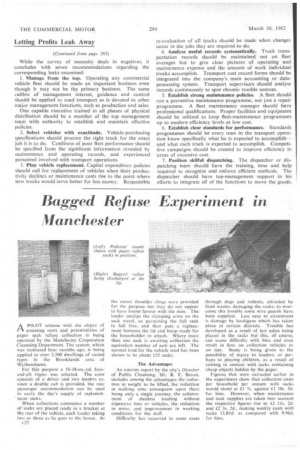
If you've noticed an error in this article please click here to report it so we can fix it.
Survey of American own-account transport reveals how elementary faults contribute to remarkably inefficient operation.
From our New York Office
AFOUR-YEAR transport survey of American companies that operate fleets as ancillary users has revealed that hitherto accepted losses can be turned into significant gains through the better movement of goods.
The confidential study conducted by the Transportation Productivity Research Department of General Motors Corporation covered road transportin a wide variety of fields, including food, petroleum, chemicals, construction, printing and publishing, iron and steel, public utilities and general distribution. Many of the fields surveyed were giants in American industry. All were well managed in their primary functions.
In every business studied, it was found that a sizeable savings potential existed. At the outset research teams expected to find a minimum savings potential of 10 per cent. of the fleet-department budget, according to Calvin J. Werner, a vice-president of General Motors. To date, it is understood, they have yet to complete a study without finding a savings potential greater than 20 per cent.
The broad-based individual studies, each taking from several weeks to seve:ral months and sometimes going 10 years deep into the company's books, revealed an incontrovertible pattern of savings opportunities that are dissipated by the following seven common profit leaks: 1. Lack of direct attention from top management.
2. Lack of exacting vehicle selection, 3. Lack of planned vehicle replacement.• 4. Lack of systematic analysis of useful records.
5. Lack of strong maintenance policies.
6. Lack of clear standards for performance.
7. Lack of skilful dispatching.
How these profit leaks occur, what they cost, and how they can be plugged is revealed in some detail by the survey. To avoid disclosure of information given in confidence, companies are not named.
The survey revealed that: 1. Lack of direct attention from top management is the commonest and costliest profit leak—the main leak from which others spring. In company after company the researchers found that: (a) High executives concentrated talent and experience on production, sales and other aspects of the main business, then took fleet operations for granted, even in some cases where road transport was 10, 20, even 30 per cent. of the company's total cost of doing business. Transport efficiency was seldom questioned, except in panic when important shipments had been damaged, delayed or lost.
(b) Top managements were not keeping in touch with trends which influenced transport costs: technological advancements in new vehicles designed to do more work
(-16
for less money; bigger payloads, legalized in one State at a time because of improvements in trucks and highways; changing transport requirements, the result of new marketing concepts (longer hauls with larger loads to fewer and larger outlets); more efficient loading, the result of improved techniques, procedures, new equipment for handling and packaging materials.
(c) Transport policies were impractical because they had been established by executives without specialized knowledge of transport.
(d) Standards for high performance did not exist, therefore low performance had become the standard in transport.
(e) Goals •for transport efficiency and incentives for improving it did not exist, therefore inefficiency did.
Lasing Vast Sums In one instance the G.M.C. research team found a transport profit leak greater than 20 per cent. of the fleetoperations budget of a company doing. $3 billion (over £1,000m.) in annual sales. Relating hauling expense to sales, the company arrived at a transport cost of 1.5 per cent. —the exact average of their industry's range in the same period.
Since 1.5 per cent. of sale S was $45m. (£16.07m.), a 20 per cent. saving represented $9m. (£3.22m.), This sum, transferred from expenditure to. profit, results (after tax deduction) in about $4.5m. (£1.6m.) net profit—the equivalent of the net profit on 300 new customers each spending $1 m. (£357,100) with the company.
• 2. Lack of exacting vehicle selection was found to be responsible for the fact that thousands of good vehicles were found operating inefficiently, since they had not been selected properly for the work they were to do. Time and again a careful, knowledgeable analysis of the assignment was ignored. The researchers found that rarely taken into consideration were: length of run; size and nature of load; topography; road and traffic conditions; legal requirements and load limits; and maintenance facilities.
The survey team examined a fleet that hauled about a million tons more than 10 million miles a year at a cost of $5m (£1.8m.). Although 85 per cent, of its runs were long hauls best suited for diesels, only 26 per cent. of the fleet units were, in fact, diesels. In other words, while only 15 per cent. of the runs were short hauls best suited by petrol-engined lorries, 74 per cent. of the units were running on petrol.
When the research team recommended switching most of the fleet to diesels, the company's top executives protested that capital would then be tied up for years! Figures were then put forward to prove that tremendous savings in operations and maintenance costs would amortize the investment quickly, and the big switch Was put in hand. Even before it was completed the company was operating with 14 per cent. fewer units, a reduction of half a million . dollars (£178,571) in capital investment for vehicles. Savings in fleet operating and maintenance costs alone were sufficient to write off the cost of the new diesels in less than three Years.
3. Lack of planned vehicle replacement was responsible for many trucks being kept in service although they should have been retired years before in the interest of company profit. In most cases the management had no idea of the expense of keeping the old vehicles.
The G.M.C. studies identified two costly misconceptions commonly held: that a vehicle should be replaced after a fixed period of service, say eight years; that each vehicle has a point of no return, a point in its life when so much had already been spent on maintenance that replacement cost would be prohibitive from then on.
In one case a company had bought the wrong. kind of trucks and had kept them too long. The policy of this particular concern was to depreciate trucks over six years. When written off, since they cost nothing, they were kept in service. The trucks were still running but maintenance expense had climbed from 5 cents (4fd.) per mile to as much as 11 cents (9ld.) per mile, and even more on some.
The G.M.C. research team pointed out to the management that 6 cents (5d.) a mile applied to 40 million miles represents a $2.4m. (£0.81m.) savings potential—or newprofit potential equal to the pre-tax profit on $120m. (£42.85m.) of new sales on a 2 per cent. profit basis.
4. Lack of systematic analysis of useful records is shown by the fact that only 15 per cent. of U.S. companies operating fleets of 100 or more vehicles keep and use records to full advantage.
This inquiry found that many companies had discontinued detailed fleet records, often in economy drives, sometimes because comptrollers had observed that the records were not being used. A common underlying factor was the reluctance or inability of many mechanics and drivers to keep complete, accurate records.
Misleading Averages
Where records had been kept, in many instances they were of fleet _averages—average operating cost per truck, average maintenance cost, average tonnage carried, average time in the shop for repairs. These records were not useful; worse, they were misleading since average figures can make the worst trucks in the fleet appear better, the best appear worse and, in fact, could make all trucks appear to have similar performances.
5. Lack of strong maintenance policies was found to be the result of the fact that top management usually could neither estimate the dollar volume of waste in fleet maintenance nor pin-point the causes. Nine out of 10 studies identified the following as the most prevalent origins of maintenance waste: (1) Over-age vehicles cost too much to maintain: maintenance expense on some old trucks ran higher than 10 cents (80.) a mile for as many as 100,000 miles a year. New vehicles would have cost about 3 cents (2-id.) per mile, a saving of 7 cents (6d.) a mile or $7,000 (£2,500) per truck per year in maintenance costs alone.
(2) Excessive demands on a truck resulted in increased maintenance costs: a vehicle, like a suit, tailored to fit individual requirements, must be altered or replaced when the original job outgrows it—or it will fall apart at the seams. The study found companies unaware that evolution in job demands gradually had built up work loads so overwhelming that even the most resourceful maintenance men could not keep repair costs within economical bounds.
(3) Outmoded facilities and tools: companies which failed to keep their fleets up to date failed also to provide modern maintenance facilities and tools, usually in the honest belief that money was being saved. The study pointed out where specialized tools and testing equipment quickly paid for themselves.
(4) Some senior executives lack know-how." A common tendency of top management to underestimate the importance and complexity of fleet maintenance sometimes means that the maintenance job is not understood fully by the man selected for it. Instead of efficient executives managing well-planned preventive-maintenance programmes, the study teams found shop managers who thought eagerly in terms of repairing breakdowns.
Lack of top-management • knowledge of maintenance usually is reflected in lack of standardized shop procedures, lack of training, lack of supervision and lack of cost-consciousness.
Lack of Records and Standards
(5) Poor communications. The surveys uncovered phenomenal numbers of skilled-man hours squandered by maintenance mechanics who launched into repair jobs without specific information from drivers or past records.
6. Lack of clear standards of performance were shown to have a strong correlation with inefficiency of fleet operations. Where high standards were set, they were usually met or exceeded. Where standards were low, not enforced or non-existent, morale was low and costs high.
The study found that there are seven measurements used in many large, well-run fleets to establish standards for performance. These are: (a) Vehicle availability (number of shifts each vehicle is available for use versus the number of shifts it is scheduled for repairs); (b) Utilization time (vehicle trip hours versus idle hours on ,the ready line); (c) Utilization payload (loaded miles versus empty miles); (d) Productivity (total number of payload ton-miles for the period measured); (e) Fuel efficiency (gallons per thousand ton-miles); (f) Maintenance efficiency (combined cost of labour and materials in cents-per-vehicle mile); (g) Life tables of major components (actual miles to first major overhaul; actual miles after overhaul).
The G.M.C. researchers found marked success in cornpanies with clear standards for performance. Many were gratified with results in eliminating excessive changes in batteries, reducing road-service calls, correcting clutch abuses and lengthening brake re-lining periods.
One company reported that within only three months after standards were established for vehicle availability and utilization its fleet achieved a 20 per cent. reduction in the number of vehicles, without impairing delivery work.
7. Lack of skilful dispatching caused goods for the primary business to be delivered late, in bad condition, at an added cost, or in a combination of these. The survey discovered these profit wastes in dispatching: (1) Underloading: too-light payloads on every trip because the company had no weighing device; trucks loaded on guesswork were usually underloaded by wide margins to avoid risking illegal-weight penalties.
(2) Overloading: legal-weight cargo beyond the capacity rating set by the truck's manufacturer.
(3) Stop-and-go loading: fitful cargo flow from production line or warehouse to waiting trucks.
(4) Loading that hampers unloading: cargo stowed in the reverse order of multiple-stop deliveries; not on pallets when it should be.
(5) Inadequate records: scheduling charts and operating information that made it impossible to pin-point for each vehicle excessive and unprofitable time for maintenance, repairs and loading, or the sagging efficiencies of fleet divisions. While the survey of necessity deals in negatives, it concludes with seven recommendations regarding the corresponding leaks examined: 1. Manage from the topOperating any commercial vehicle fleet should be made an important business even though it may not be the primary business. The same calibre of management interest, guidance and control should be applied to road transport as is devoted to other major management functions, such as production and sales.
One capable executive trained in all phases of physical distribution should be a member of the top management team with authority to establish and maintain effective policies.
2. Select vehicles' with exactitude. Vehicle-purchasing specifications should procure the right truck for the exact job it is to do. Costliness of poor fleet performance should be specified from the significant information revealed by maintenance and operating records, and experienced personnel involved with transport operations.
3. Plan vehicle replacement. Capital expenditure policies should can for replacement of vehicles when their productivity declines or maintenance costs rise to the point where new trucks would serve better for less money. Responsible re-evaluation of MI trucks should be made when changes occur in the jobs they are required to do.
4. Analyse useful records systematically. Truck transportation records should be maintained not on fleet averages but to give clear pictures of operating and maintenance expense and the amount of work individual trucks accomplish. Transport cost record forms should be integrated into the company's main accounting or dataprocessing system. Transport supervisors should analyse records continuously to spot chronic trouble sources.
5. Establish strong maintenance policies. A fleet should run a preventive maintenance programme, not just a repair programme. A fleet maintenance manager should have professional qualifications. Proper facilities and equipment should be utilized to keep fleet-maintenance programmes up to modern efficiency levels at low cost.
6. Establish clear standards for performance. Standards programmes should let every man in the transport operation know specifically what he is expected to accomplishand what each truck is expected to accomplish. Competitive campaigns should be created to improve efficiency in areas of excessive cost.
7. Position skilful dispatching. The dispatcher or dispatching team should have the training, time and help required to recognize and enforce efficient methods. The dispatcher should have top-management support in his efforts to integrate all of the functions to move the goods.