Watch the Cooling System
Page 34
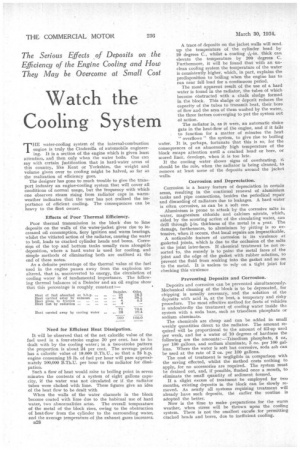
If you've noticed an error in this article please click here to report it so we can fix it.
The Serious Effects of Deposits on the Efficiency of the Engine Cooling and How They May be Overcome at Small Cost
THE water-cooling system of the internal-combustion engine is truly the Cinderella of automobile engineering. It is a section of the engine which is given least attention, and then only when the water boils. One can say with certain Tustification that in hard-water areas of this country, like Kent or Yorkshire, the weight and volume given over to cooling might be halved, so far as the realization of efficiency goes.
The designer has gone to much trouble to give the transpert industry an engine-cooling system that will cover all conditions of normal usage, but the frequency with which one observes steam rising from radiator caps in warmweather indicates that the user has not realized the importance of efficient cooling. The consequences can be heavy to the fleet owner.
Effects of Poor Thermal Efficiency.
Poor thermal transmission in the block due to lime deposits on the walls of the water-jacket gives rise to increased oil consumption, fiery ignition and warm bearings, whilst the vitiated action of the radiator, causing the water to boil, leads to cracked cylinder heads and bores. Corrosion of the top and bottom tanks usually runs alongside deposition, where a hard water is used for cooling, and simple methods of eliminating both are outlined at the end of these notes.
As a definite percentage of the thermal value of the fuel used in the engine passes away from the explosion unaltered, that is, unconverted to energy, the circulation of cooling water is of fundamental importance. The following thermal balances of a Daimler and an oil engine show that this percentage is roughly constant:
Need for Efficient Heat Dissipation.
It will be observed that of the net calorific value of the fuel used in a four-stroke engine 30 per cent, has to be dealt with by the cooling water ; in a two-stroke pattern the proportion is about 24 per cent. The average petrol has a calorific. value of 19,000 B.Th.U., so that a 25 h.p. engine consuming 18 lb. of fuel per hour will pass approxin:ately 100,000 B.Th.U. per hour to the radiator for dissipation.
Such a flow of heat would raise to boiling point in seven minutes the contents of a system of eight gallons capacity, if the water was not circulated or if the radiator tubes were choked with lime. These figures give an idea of the heat flow -to be dealt with
When the walls of the water channels in the block become coated with lime due to the habitual use of hard water, two abnormalities arise. The overall tempeiature of the metal of the block rises, owing to the obstruction of heat-flow from the cylinder to the surrounding water, and the average temperature-of the exhaust gases increases.
1128
A. trace of deposits on the jacket walls will send up the temperature of the cylinder head by 20 degrees C., whilst a coating eirin, thick can elevate the temperature by 200 degrees C. Furthermore, it will be found that with an unclean cooling system the temperature of the water is consistently higher, which, in part, explains the predisposition to boiling when the engine has to run near full load for a continuous period.
The most apparent result of the use of a hard water is found in the radiator, the tubes of which become obstructed with a chalk sludge formed in the block. This sludge or deposit reduces the capacity of the tubes to transmit heat, their, bore of flow and the area of them washed by the water, the three factors converging to put the system out of action.
The radiator is, as it were, an automatic sluice gate in the heat-flow of the engine, and if it fails to function for a matter of minutes the heat " overflows" the system, to give rise to boiling water. It is, perhaps, fortunate that this is so, for the consequences of an abnormally high temperature of the block escape attention until a cracked head' or bore, or scored liner, develops, when it is too late. If the cooling water shows signs of overheating, it should be the rule, when the radiator is being cleaned, to remove at least some of the deposits around the jacket walls.
Corrosion and Depreciation.
Corrosion is a heavy feature of depreciation in certain areas, resulting in the continual renewal of aluminium tanks and pipe connections, besides the periodical repair and discarding of radiators due to leakages. A hard water is often corrosive, as can be a soft one.
Aluminium is prone to attack by the corrosive salts in water, magnesium chloride and calcium nitrate, which, aided by the scouring action of the circulating water, can drill through t-in. thickness of the metal in a year. The damage, furthermore, to aluminium by pitting is so extensive, when it occurs, that local repairs are impracticable.
A noticeable feature of corrosion is its virulence at gasketed joints, which is due to the occlusion of the salts at the joint inter-faces. If chemical treatment be not resorted to, the remedy is to paint: the metal faces of the joint and the edge of the gasket with rubber solution, to prevent the fluid from soaking into the gasket and so on to the metal. It is useless to rely on a tight joint for checking this virulence
Preventing Deposits and Corrosion..
Deposits and corrosion can be prevented simultaneously. Mechanical cleaning of the block is to be deprecated,, for chipping is usually necessary, and the solution of the deposits with acid is, at the best, a temporary and risky procedure. The most effective method for fleets of vehicles is undoubtedly the treatment qf cooling water inside the system with a soda base, such as trisodium phosphate or sodium alumivate.
The chemicals are cheap and can be added in small weekly quantities direct to the radiator. The amount required will be proportional to the amount of fill-up used per week, and for a water of 10 degrees of hardness the following are the amounts:—Tiisodium phosphate, 5 oz. per 100 gallons, and sodium aluminate, 3 oz. per 100 gallons. Where the water is soft but corrosive, soda ash can be used at the rate of 2 oz. per 100 gallons.
The cost of treatment is negligible in comparison with the saving effected, whilst the method costs nothing to apply, for no accessories are required. The system must he drained out, and, if possible, flushed once a month, to eliminate the small quantity of sediment formed.
If a slight excess of treatment be employed for two months, existing deposits in the block can be slowly removed. As nearly all systems requiring treatment will already have such deposits, the earlier the routine is adopted the better. Now is the time tp make preparations for the warm weather, when stress will be thrown upon the cooling system. There is not the smallest excu9e for permitting cracked heads and bores, due to inefficient cooling.