Latest Practice in American Bus Design
Page 81
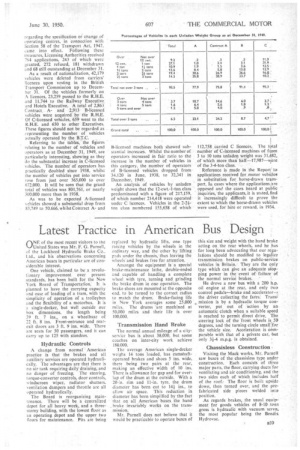
If you've noticed an error in this article please click here to report it so we can fix it.
(-NNE of the most recent visitors to Inc Is/United States was Mr. F. G. Parnell, of the Lockheed Hydraulic Brake Co., Ltd., and his observations concerning American buses in particular are of considerable interest.
One vehicle, claimed to be a revolutionary improvement over present standards, has been built for the New York Board of Transportation; It is planned to have the carrying capacity and ease of loading of a tram, with the simplicity of operation of a trolleybus and the flexibility of a motorbus. It is a single-decker, but well outside our box dimensions, the length being 39 ft. 7 ins., on a wheelbase of 22 ft. 8 ins. Front-entrance and rearexit doors are 3 ft. 9 ins. wide. There are seats for 50 passengers, and it can carry up to 125 with standees.
Hydraulic Controls
A change from normal American practice is that the brakes and all auxiliary services are operated hydraulically. The advantages are that there is no air tank requiring daily draining, and no danger of freezing. The steering, torque-converter controls, door controls, windscreen wiper, radiator shutters. ventilation dampers and throttle are all operated hydraulically.
The Board is reorganizing maintenance. There will be a centralized depot for all heavy work, and a threestorey building, with the lowest floor, as an operating depot and the upper two iloors for maintenance. Pits are being replaced by hydraulic lifts, one type raising vehicles by the wheels in the ordinary way, and the other by lifting pads under the chassis, thus leaving the wheels and brakes free for attention.
Amongst the equipment is a special brake-maintenance lathe, double-ended and capable of handling a complete wheel with tyre, turning and grinding the brake drum in one operation. The brake shoes are mounted at the opposite end, to be turned to the correct radius to match the drUm-. Brake-facing life in New York averages some 25,000 • miles. The drums are machined at 50,000 miles and their life is over 100.000.
Transmission Hand Brake
The normal annual mileage of a cityservice bus is about 38,000. but some coaches on inter-city work achieve 180,000.
The average American single-decker weighs 14 tons loaded, has camshaftoperated brakes and shoes 5 ins, wide, there being two pairs at the rear, making an effective width of 10 ins. There is allowance for gap and for overlap of the drum at the outside. With a 20-in. rim and 11-in. tyre, the, drum diameter has been cut to 14+ ins., to allow air space. This reduction in diameter has been simplified by the fact that on all American buses, the hand brake invariably works on the transmission.
Mr. Parnell does not believe that it would be practicable to operate buses of
this size and weight with the hand brake acting on the rear wheels, and he has for long been advocating that our regulations should be modified to legalize transmission brakes on public-serVice vehicles in Britain.They are the only type which can give an adequate stopping power in the event of. failure of the normal service brakes. '
He drove a new bus with a 200 h.p. oil engine at the rear, and only two control pedals-brake and, aceelerat or-1 the driver collecting the fares: TransL mission is by a hydraulic torque converter, put out of action by an automatic clutch when a suitable speed is reached to permit. direct drive. The steering lock of the front wheels is 50 degrees, and the turning circle smalrfor the vehicle size. Acceleration is COmparable with that of a private car, hut only 3i-4 m.p.g. is obtained.
Chassisless Construction,
Visiting the Mack works, Mr. Parnell saw buses of the chassisless type under construction. Each consists of three major parts, the floor, carrying ducts for ventilating and air conditioning, and the two sides each of which includes half of the roof.The floor is built upside down, then turned over, and the prefabricated side pieces welded into position.
As regards brakes, the usual equipment for goods vehicles of 8-10 tons gross is hydraulic with vacuum servo. the most popular being the Bend's Hyd rovac.