Controlled-temperature haulage is changing fast as technical advances have made
Page 38
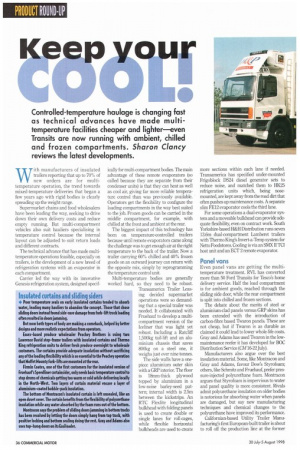
Page 39
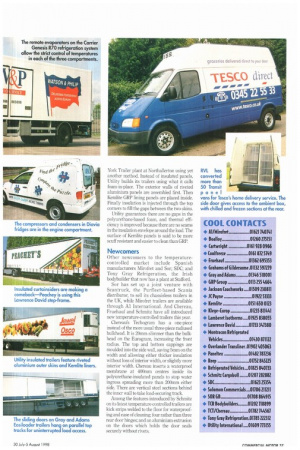
If you've noticed an error in this article please click here to report it so we can fix it.
multitemperature facilities cheaper and lighter—even Transits are now running with ambient, chilled and frozen compartments. Sharon Clancy reviews the latest developments.
With manufacturers of insulated trailers reporting that up to 70% of new orders are for multitemperature operation, the trend towards mixed-temperature deliveries that began a few years ago with rigid bodies is clearly spreading up the weight range.
Supermarket chains and food wholesalers have been leading the way, seeking to drive down their own delivery costs and reduce empty running. But multi-compartment vehicles also suit hauliers specialising in temperature control because the internal layout can be adjusted to suit return loads and different contracts.
The technical advance that has made multitemperature operations feasible, especially on trailers, is the development of a new breed of refrigeration systems with an evaporator in each compartment.
Carrier led the way with its innovative Genesis refrigeration system, designed specif
ically for multi-compartment bodies. The main advantage of these remote evaporators (so called because they are separate from their condenser units) is that they can heat as well as cool air, giving far more reliable temperature control than was previously available. Operators get the flexibility to configure the loading compartments in the way best suited to the job. Frozen goods can be carried in the middle compartment, for example, with chilled at the front and ambient at the rear.
The biggest impact of this technology has been on temperature-controlled trailers because until remote evaporators came along the challenge was to get enough air at the right temperature to the back of the trailer. Now a trailer carrying 60% chilled and 40% frozen goods on an outward journey can return with the opposite mix, simply by reprogramming the temperature control unit.
Multi-temperature bodies are generally worked hard, so they need to be robust. Transamerica Trailer Leasing decided supermarket operations were so demanding that a special trailer was needed. It collaborated with Fruehauf to develop a multicompartment version of the Iceliner that was light yet robust. Including a Rateliff 1,500kg tail-lift and an aluminium chassis that saves 800kg on a steel one, it weighs just over nine tonnes.
The side walls have a onepiece aluminium outer skin with a GRP interior. The floor is 18mm-thick plywood topped by aluminium in a low-noise barley-seed pattern; internal width is 2.5m between the kickstrips. An RTC Flexlite longitudinal bulkhead with folding panels is used to create double or single lanes for roll-cages, while flexible horizontal bulkheads are used to create
more sections within each lane if needed. Transamerica has specified under-mounted Frigoblock DS24 diesel generator sets to reduce noise, and matched them to HK.25 refrigeration units which, being nosemounted, are kept away from the road dirt that often pushes up maintenance casts. A separate slim FE12 evaporator cools the third lane.
For some operations a dual-evaporator system and a moveable bulkhead can provide adequate flexibility, even on contract work. South Yorkshire-based H&H Distribution runs seven 13.6m dual-compartment Lamberet trailers with Thermo King's Invert-a-Temp system for Netto Foodstores. Cooling is via an SMX H ICI host unit and an ECT 2 remote evaporator.
Panel vans
Even panel vans are getting the multitemperature treatment. RVL has converted more than 50 Ford Transits for Tesco's home delivery service. Half the load compartment is for ambient goods, reached through the sliding side door, while the rear compartment is split into chilled and frozen sections.
The debate about the merits of steel or aluminium-clad panels versus GRP skins has been extended with the introduction of carbon-fibre based Twaron panels. These are not cheap, but if Twaron is as durable as claimed it could lead to lower whole-life costs. Gray and Adams has used Twaron in the lowmaintenance reefer it has developed for BOG Distribution Service (CM16-22 July).
Manufacturers also argue over the best insulation material. Some, like Montracon and Gray and Adams, favour Dow's Styrofoam; others, like Schmitz and Fruehauf, prefer pressure-injected polyurethane foam. Montracon argues that Styrofoam is impervious to water and panel quality is more consistent. Rivals admit polyurethane insulation on older bodies is notorious for absorbing water when panels are damaged, but say new manufacturing techniques and chemical changes to the polyurethane have improved its performance.
Californian-based Utility Trailer Manufacturing's first European-built trailer is about to roll off the production line at the former York Trailer plant at Northallerton using yet another method. Instead of insulated panels, Utility builds its trailers using what it calls foam-in-place. The exterior walls of riveted aluminium panels are assembled first. Then Kemlite GRP lining panels are placed inside. Finally insulation is injected through the top corners to fill the gaps between the two skins.
Utility guarantees there are no gaps in the polyurethane-based foam, and thermal efficiency is improved because there are no seams in the insulation envelope around the load. The surface of Kemlite panels is said to be more scuff resistant and easier to clean than GRP.
Newcomers
Other newcomers to the temperaturecontrolled market include Spanish manufacturers Mirofret and Sor; SDC; and Tony Gray Refrigeration, the Irish bodybuilder that now has a plant at Stafford.
Sor has set up a joint venture with Scantruck, the Purfleet-based Scania distributor, to sell its chassisless trailers in the UK, while Mirofret trailers are available through Al International. And Chereau, Fruehauf and Schmitz have all introduced new temperature-controlled trailers this year.
Chereau's Techogram has a one-piece instead of the more usual three-piece radiused bulkhead. It is 20mm slimmer than the bulkhead on the Eurogram, increasing the front radius. The top and bottom cappings are moulded into the side wall, saving 5mm on the width and allowing either thicker insulation without loss of interior width, or slightly more interior width. Chereau inserts a waterproof membrane at 400mm centres inside its polyurethane-insulated panels to stop water ingress spreading more than 200mm either side. There are vertical steel sections behind the inner wall to take load-securing track.
Among the features introduced by Schmitz on its latest temperature-controlled trailers are kick strips welded to the floor for waterproofing and ease of cleaning; four rather than three rear door hinges; and an aluminium extrusion on the doors which holds the door seals securely without rivets.