WHAT PRICE MORE POWER?
Page 38
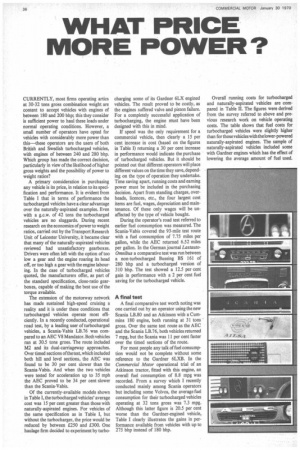
Page 39
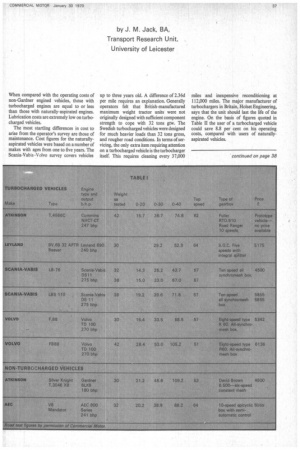
Page 40

If you've noticed an error in this article please click here to report it so we can fix it.
by J. M. Jack, BA, Transport Research Unit, University of Leicester
CURRENTLY, most firms operating artics at 30-32 tons gross combination weight are content to accept vehicles with engines of between 180 and 200 bhp; this they consider is sufficient power to haul these loads under normal operating conditions. However, a small number of operators have opted for vehicles with considerably more power than this—these operators are the users of both British and Swedish turbocharged vehicles, with engines of between 240 and 280 bhp. Which group has made the correct decision, particularly in view of the likelihood of higher gross weights and the possibility of power to weight ratios?
A primary consideration in purchasing any vehicle is its price, in relation to its specification and performance. It is evident from Table I that in terms of performance the turbocharged vehicles have a clear advantage over the naturally-aspirated examples. Even with a g.c.w. of 42 tons the turbocharged vehicles are no sluggards. During recent research on the economics of power to weight ratios, carried out by the Transport Research Unit of Leicester University, it became clear that many of the naturally-aspirated vehicles reviewed had unsatisfactory gearboxes. Drivers were often left with the option of too low a gear and the engine roaring its head off, or too high a gear with the engine labouring. In the case of turbocharged vehicles quoted, the manufacturers offer, as part of the standard specification, close-ratio gearboxes, capable of making the best use of the torque available.
The extension of the motorway network has made sustained high-speed cruising a reality and it is under these conditions that turbocharged vehicles operate most efficiently. In a recently conducted, operational road test, by a leading user of turbocharged vehicles, a Scania-Vabis LB.76 was compared to an AEC V8 Mandator. Both vehicles ran at 30.5 tons gross. The route included M2 and its dual-carriageway approaches. Over timed sections of the test, which included both hill and level sections, the AEC was found to be 30 per cent slower than the Scania-Vabis. And when the two vehicles were tested for acceleration up to 35 mph the AEC proved to be 34 per cent slower than the Scania-Vabis.
Of the currently-available models shown in Table I, the turbocharged vehicles' average cost was 15 per cent greater than those with naturally-aspirated engines. For vehicles of the same specification as in Table I, but without the turbocharger, the price would be reduced by between £250 and £300. One haulage firm decided to experiment by turbo
charging some of its Gardner 6LX engined vehicles. The result proved to be costly, as the engines suffered valve and piston failure. For a completely successful application of turbocharging, the engine must have been designed with this in mind.
If speed was the only requirement for a commercial vehicle, then clearly a 15 per cent increase in cost (based on the figures in Table I) returning a 30 per cent increase in performance would indicate the purchase of turbocharged vehicles. But it should be pointed out that different operators will place different values on the time they save, depending on the type of operation they undertake. Time saving apart, running costs and earning power must be included in the purchasing decision. Apart from standing charges, overheads, licences, etc., the four largest cost items are fuel, wages, depreciation and maintenance. Of these only wages will be unaffected by the type of vehicle bought.
During the operator's road test referred to earlier fuel consumption was measured. The Scania-Vabis covered the 93-mile test route with a fuel consumption of 7.75 miles per gallon, while the AEC returned 6.52 miles per gallon. In the German journal LastautoOmnibus a comparative test was run between a non-turbocharged Bussing BS 161 of 280 bhp and a turbocharged version of 310 bhp. The test showed a 12.5 per cent gain in performance with a 2 per cent fuel saving for the turbocharged vehicle.
A final test A final comparative test worth noting was one carried out by an operator using the new Scania LB.80 and an Atkinson with a Cummins 180 engine, both running at 31 tons gross. Over the same test route as the AEC and the Scania LB.76, both vehicles returned 7 mpg, but the Scania was 11 per cent faster over the timed sections of the route.
For most people any talk of fuel consumption would not be complete without some reference to the Gardner 6LXB. In the Commercial Motor operational trial of an Atkinson tractor, fitted with this engine, an overall fuel consumption of 8.8 mpg was recorded. From a survey which I recently conducted mainly among Scania operators but including some Volvos, the average fuel consumption for their turbocharged vehicles operating at 32 tons gross was 7.3 mpg. Although this latter figure is 20.5 per cent worse than the Gardner-engined vehicle, Table I clearly illustrates the gains in performance available from vehicles with up to 275 bhp instead of 180 bhp. Overall running costs for turbocharged and naturally-aspirated vehicles are compared in Table II. The figures were derived from the survey referred to above and previous research work on vehicle operating costs. The table shows that fuel costs for turbocharged vehicles were slightly higher than for those vehicles with the lower-powered naturally-aspirated engines. The sample of naturally-aspirated vehicles included some with Gardner engines which has the effect of lowering the average amount of fuel used. When compared with the operating costs of non-Gardner engined vehicles, those with turbocharged engines are equal to or less than those with naturally-aspirated engines. Lubrication costs are extremely low on turbocharged vehicles.
The most startling differences in cost to arise from the operator's survey are those of maintenance. Cost figures for the naturallyaspirated vehicles were based on a number of makes with ages from one to five years. The Scania-Vabis-Volvo survey covers vehicles
up to three years old. A difference of 2.36d per mile requires an explanation. Generally operators felt that British-manufactured maximum weight tractor units were not originally designed with sufficient component strength to cope with 32 tons gtw. The Swedish turbocharged vehicles were designed for much heavier loads than 32 tons gross, and rougher road conditions. In terms of servicing, the only extra item requiring attention on a turbocharged vehicle is the turbocharger itself. This requires cleaning every 37,000 miles and inexpensive reconditioning at 112,000 miles. The major manufacturer of turbochargers in Britain, Holset Engineering, says that the unit should last the life of the engine. On the basis of figures quoted in Table H the user of a turbocharged vehicle could save 8.8 per cent on his operating costs, compared with users of naturallyaspirated vehicles.
The Scottish Motor Show in November 1969 pointed the way for future power requirements. A majority of the 44-tongross vehicles on display were fitted with turbocharged engines giving 250 bhp or more. This raises the question of whether the advantages of turbocharged engines will in any way be able to offset the increase in running costs, resulting from such things as rises in wages, at the higher gross weights. The vehicles road tested in Table I, at 38 to 42 tons gross, returned an average fuel consumption of 6.17 mpg. This represents a 15.47 per cent fuel consumption increase over similar vehicles operating at 32 tons gross.
unng 1b tile oaa Researchoratory produced a report on "the effect of road and traffic conditions on fuel consumption", in which the RRL examined the changes in fuel consumption as a result of the addition of extra load to a vehicle. For a change in gross weight from 20 tons to 30 on an AEC Mandator with 179 bhp engine, there was a 21.8 per cent fuel consumption increase when the vehicle accelerated from rest to 35 mph. Based on the 38-42-ton vehicles tested in Table I, the change in fuel consumption for the same change in load and speed was 12.9 per cent. As loads become heavier it is evident that turbocharged vehicles are able to cope with extra weight without a prohibitive change in fuel consumption. Table III gives an indication of running costs for a turbocharged 42/44-ton vehicle; with 6 bhp/ ton. The figures were derived from the current operating costs of turbocharged vehicles as indicated in Table II. Tyre wear shows the largest cost increase. This is due to the increased loads and extra scrub on the tyres incurred by the use of 6 x 4 tractor units.
In researching for this work I was struck by the tremendous conservatism which pervades the operating industry in this country. Many operators were quite prepared to reject technical developments like turbocharging purely on the grounds that it was new and not enough was known about it. The principles of turbocharging have been known and used successfully for many years on large-capacity diesel engines. Now, this knowledge is being usefully applied to commercial vehicles. Extra power from turbocharging can be made to pay off in the form of higher speeds and reduced running costs.