THE
Page 38
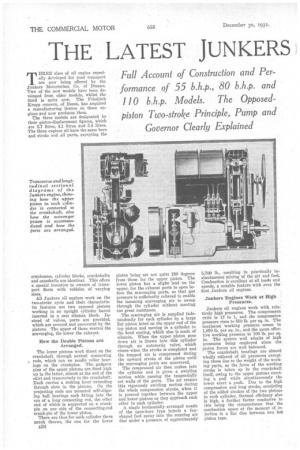
Page 39
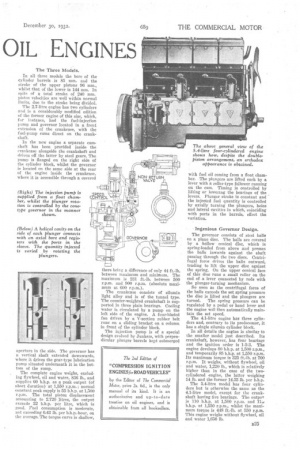
If you've noticed an error in this article please click here to report it so we can fix it.
LATEST jUNKERS THREE sizes of oil engine especially developed for road transport are now being offered by the Junkers Motorentrau Co. of Dessau. Two of the new models have been developed from older models, whilst the third is quite new. The Friedrich Krupp concern, of Essen, has acquired a manufacturing licence on these engines and now produces them.
The three models are designated by their piston-displacement figures, which are 2.7 litres, 4.1 litres and 5.4 litres. The three engines all have the same bore and stroke and all parts, excepting the crankcases, cylinder blocks, crankshafts and camshafts are identical. This offers a special incentive to owners of transport fleets with vehicles of varying sizes.
All Junkers oil engines work on the two-stroke cycle and their characteristic features are two opposed pistons working in an upright cylinder barrel inserted in a cast silumin block. Instead of valves, ports are provided, which are covered and uncovered by the pistons. The upper of these control the scavenging, the lower the exhaust.
How the Double Pistons are Arranged.
The lower pistons work direct on the crankshaft through normal connecting • rods, which run on needle roller bearings on the crankpins. The gudgeon pins of the upper pistons are fixed high up in the latter, almost at the end of the skirt and transversely to the crankshaft. Each carries a rocking lever extending through slots in the pistons. On the projecting ends are mounted self-aligning ball bearings each fitting into the eye of a long connecting rod, the other end of which is supported on a crankpin on one side of the connecting-rod crank-pin of the lower piston.
There are thus for each cylinder three crank throws, the one for the lower Es24 piston being set not quite 180 degrees from those for the upper piston. The lower piston has a slight lead on the upper, for the exhaust ports to open before the scavenging ports, so that gas pressure is sufficiently relieved to enable the incoming scavenging air to sweep through the cylinder without meeting too great resistance.
The scavenging air is supplied independently for each cylinder by a large flat piston fitted on the upper end of the top piston and moving in a cylinder in the head casting, which also is made of silumin. When the upper piston goes down air is drawn into this cylinder through an automatic valve; which closes when the stroke is completed and the trapped air is compressed during the upward stroke of the piston until the scavenging ports are uncovered.
The compressed air then rushes into the cylinder and is given a swirling motion while passing the tangentially set walls of the ports. The air retains this vigorously swirling motion during the whole compression stroke, when it is pressed together between the upper and lower pistons as they approach each other in each cylinder.
A single horizontally arranged nozzle of the open-bore type injects a fanshaped fuel spray into the rotating air disc under a pressure of approximately 5,700 lb., resulting in pfactically instantaneous mixing of the air and fuel. Combustion is excellent at all loads and speeds, a notable feature with even the first Junkers oil engines.
Junkers Engines Work at High Pressures.
Junkers oil engines work with relatively high pressures. The compression ratio is 17 to 1, and the compression pressure rises to 550 lb. per sq. in. The maximum working pressure comes to 1,0q0 lb. per sq. in., and the mean effective working pressure to 106 lb. per sq. in. The system well admits of high pressures being employed since the Piston forces are well balanced. The crankshaft bearings are almost wholly relieved of all pressures excepting those due to the weight of the working parts, as the force of the working stroke is taken up in the crankshaft itself, owing to the upper pistons exerting a pull while simultaneously the lower exert a push. Due to the high compression and long stroke, consisting of the added strokes of the two pistons in each cylinder, thermal efficiency also is high, a further factor conducive to this being the circumstance that the combustion space at the moment of injection is a flat disc between two hot piston tops. In all three models the bore of the cylinder barrels is 85 mm. and the stroke of the upper pistons 96 mm., whilst that of the lower is 144 mm. In spite of a total stroke of 240 mm. piston velocities are well within normal limits, due to the stroke being divided.
The 2.7-litre engine has two cylinders and is a considerably modified edition of the former engine of this size, which, for instance, had the fuel-injection pump and governor located in a front extension of the crankcase, with the fuel-pump cams direct on the crankshaft.
In the new engine a separate camshaft has been provided inside the crankcase alongside the crankshaft and driven off the latter by steel gears. The pump is flanged on the right side of the cylinder block, whilst the governor is located on the same side at the rear of the engine inside the crankcase, where it is accessible through a covered aperture in the side. The governor has a vertical shaft extended downwards, where it drives the gear-type lubrication pump situated underneath it in the bottom of the sump.
The complete engine weighs, excluding flywheel, oil and water, 836 lb., and supplies 60 b.h.p. as a peak output (of short duration) at 1,550 r.p.m.; normal constant peak supply is 55 b.h.p. at 1,500 r.p.m. The total piston displacement amounting to 2.720 litres, the output exceeds 22 b.h.p. per litre, which is good. Fuel consumption is moderate, not exceeding 0.43 lb. per b.h.p.-hour, on the average. The torque curve is shallow, there being a difference of only 44 ft.-lb. between maximum and minimum. The maximum is 231 ft.-lb. between 500 r.p.m. and 900 r.p.m. (absolute maximum at 600 r.p.m.).
The crankcase consists of silumin light alloy and is of the tunnel type. The counter-weighted crankshaft is supported in three plain bearings. Cooling water is circulated by a pump on the left side of the engine. A four-bladed fan driven by a V-section rubber belt runs on a sliding bracket on a column in front of the cylinder block.
The injection pump is of a special design evolved by Junkers, with perpendicular plunger barrels kept submerged
with fuel oil coming from a float chamber. The plungers are lifted each by a lever with a roller-type follower running on the cam. Timing is controlled by lifting or lowering the bearings of the levers. Plunger stroke is constant and the injected fuel quantity is controlled by axially turning the plungers, holes and lateral cavities in which, coinciding with ports in the barrels, effect the variation.
• Ingenious Governor Design.
The governor consists of steel balls on a plane disc. The balls are covered by a hollow conical disc, which is spring-loaded from above and presses the balls inwards against the shaft passing through the two discs. Centrifugal force drives the halls outward, tending to lift the upper disc against the spring. On the upper conical face of this disc runs a small roller on the end of a lever connected by rods with the plunger-turning mechanism. So soon as the centrifugal force of the balls exceeds the set spring pressure the disc is lifted and the plungers are turned. The spring pressure can be regulated by a pedal or hand lever and the engine will then automatically maintain the set speed.
The 4.1-litre engine has three cylinders and, contrary to its predecessor, it has a single silumin cylinder block.
In all details the engine is similar to the smaller model just described. Its crankshaft, however, has four bearings and the ignition order is 1-2-3. The engine develops 80 b.h.p. at 1,500 r.p.m., and temporarily 85 b.h.p. at 1,550 r.p.m. Its maximum torque is 325 ft.-lb. at 700 r.p.m. It weighs, without flywheel, oil and water, 1,220 lb., which is relatively higher than in the case of the twocylindered engine, the latter weighing 14 lb. and the former 14.35 lb. per b.h.p.
The 5.4-litre model has four cylinders but is otherwise the same as the 4.1-litre model, except for the crankshaft having five bearings. The output is 110 b.h.p. at 1,500 r.p.m. and 11.1 b.h.p. at 1,550 r.p.m., whilst the maximum torque is 448 ft.-lb. at 550 r.p.m. This engine weighs without flywheel, oil and water 1,650 lb.