EATCI SPLITTER
Page 34
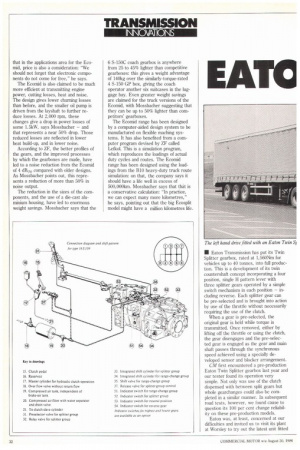
Page 35
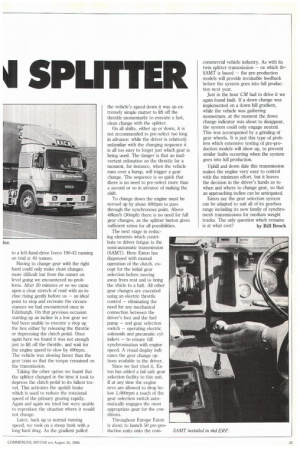
If you've noticed an error in this article please click here to report it so we can fix it.
that in the applications area for the Ecomid, price is also a consideration: "We should not forget that electronic components do not come for free," he says.
The Ecomid is also claimed to be much more efficient-at transmitting engine power, cutting losses, heat and noise. The design gives lower churning losses than before, and the smaller oil pump is driven from the layshaft to further reduce losses. At 2,000 rpm, these changes give a drop in power losses of some 1.5kW, says Mossbacher — and that represents a near 50% drop. Those reduced losses are reflected in lower heat build-up, and in lower noise.
According to ZF, the better profiles of the gears, and the improved processes by which the gearboxes are made, have led to a noise reduction from the Ecomid of 4 dB(A) compared with older designs. As Mossbacher points out, this represents a reduction of more than 50% in noise output.
The reduction in the sizes of the components, and the use of a die-cast aluminium housing, have led to enormous weight savings. Mossbacher says that the 6 S-150C coach gearbox is anywhere from 25 to 45% lighter than competitive gearboxes: this gives a weight advantage of 140kg over the similarly-torque-rated 4 S-150 GP box, giving the coach operator another six suitcases in the luggage bay. Even greater weight savings are claimed for the truck versions of the Ecomid, with Mossbacher suggesting that they can be up to 50% lighter than competitors' gearboxes.
The Ecomid range has been designed by a computer-aided design system to be manufactured on flexible maching systems. It has also benefited from a computer program devised by ZF called Lefkol. This is a simulation program, which reproduces the loadings of actual duty cycles and routes. The Ecomid range has been designed using the loadings from the B10 heavy-duty truck route simulation: on that, the company says it should have a life well in excess of 500,000km. Mossbacher says that that is a conservative calculation: "In practice, we can expect many more kilometres," he says, pointing out that the big Ecosplit model might have a million kilometres life. • Eaton Transmission has put its Twin Splitter gearbox, rated at 1,560Nm for vehicles up to 40 tonnes, into full production. This is a development of its twin countershaft concept incorporating a four position, single H pattern lever with three splitter gears operated by a simple switch mechanism in each position — including reverse. Each splitter gear can be pre-selected and is brought into action by use of the throttle without necessarily requiring the use of the clutch.
When a gear is pre-selected, the original gear is held while torque is transmitted. Once removed, either by lifting off the throttle or using the clutch, the gear disengages and the pre-selected gear is engaged as the gear and main shaft passes through the synchronous speed achieved using a specially developed sensor and blocker arrangement.
CM first encountered a pre-production Eaton Twin Splitter gearbox last year and our tester found its operation very simple. Not only was use of the clutch dispensed with between split gears but whole gearchanges could also be completed in a similar manner. In subsequent road tests, however, we found cause to question its 100 per cent change reliability on these pre-production models.
Eaton was, at least, concerned at our difficulties and invited us to visit its plant at Worsley to try out the latest unit fitted to a left-hand-drive lveco 190-42 running on trial at 40 tonnes.
Having to change gear with the right hand could only make clean changes more difficult but from the outset on level going we encountered no problems. After 20 minutes or so we came upon a clear stretch of road with an incline rising gently before us — an ideal point to stop and recreate the circumstances we had encountered once in Edinburgh. On that previous occasion starting up an incline in a low gear we had been unable to execute a step up the box either by releasing the throttle or depressing the clutch pedal. Once again here we found it was not enough just to lift off the throttle, and wait for the engine speed to slow by 400rpm. The vehicle was slowing faster than the gear train so that the torque remained on the transmission.
'raking the other option we found that the splitter changed in the time it took to .depress the clutch pedal to its fullest travel. This activates the upshift brake which is used to reduce the rotational speed of the primary gearing rapidly. Again and again we tried but were unable to reproduce the situation where it would not change.
Later, back up to normal running speed, we took on a steep bank with a long hard drag. As the gradient pulled the vehicle's speed down it was an extremely simple matter to lift off the throttle momentarily to execute a fast, clean change with the splitter.
On all shifts, either up or down, it is not recommended to pre-select too long in advance: while the driver is relatively unfamiliar with the changing sequence it is all too easy to forget just which gear is being used. The danger is that an inadvertent relaxation on the throttle for a moment, for instance, when the vehicle runs over a bump, will trigger a gear change. The sequence is so quick that there is no need to pre-select more than a second or so in advance of making the shift.
To change down the engine must be revved up by about 400rpm to pass through the synchronous point. Above 48kmih (30mph) there is no need for full gear changes, as the splitter button gives sufficient ratios for all possibilities.
The next stage in reducing elements which contribute to driver fatigue is the semi-automatic transmission (SAMT). Here Eaton has dispensed with manual operation of the clutch, except for the initial gear selection before moving away from rest and to bring the vhicle to a halt. All other gear changes are executed using an electric throttle control — eliminating the need for any mechanical connection between the driver's foot and the fuel pump — and gear selection switch — operating electric solenoids and pneumatic cylinders — to ensure full synchronisation with engine speed. A visual display indicates the gear change options available to the driver.
Since we last tried it, Eaton has added a fail safe gear selection facility to this unit. If at any time the engine revs are allowed to drop below 1,000rpm a touch of the gear selection switch automatically engages the most appropriate gear for the conditions.
Throughout Europe Eaton is about to launch 50 pre-production units onto the corn commercial vehicle industry. As with its twin splitter transmission — on which th" SA1VIT is based — the pre-production models will provide invaluable feedback before the system goes into full production next year.
Just in the hour CM had to drive it we again found fault. If a down change was implemented on a down hill gradient, while the vehicle was gathering momentum, at the moment the down change indicator was about to disappear, the system could only engage neutral. This was accompanied by a grinding of gear wheels. It is just this type of problem which extensive testing of pre-production models will show up, to prevent similar faults occurring when the system goes into full production.
Uphill and down dale this transmission makes the engine very easy to control with the minimum effort, but it leaves the decision in the driver's hands as to when and where to change gear, so that an approaching incline can be anticipated.
Eaton say the gear selection system can be adapted to suit all of its gearbox range including its new family of synchromesh transmissions for medium weight trucks. The only question which remains is at what cost? by Bill Brock