ZF IN THE FOREFRONT
Page 33
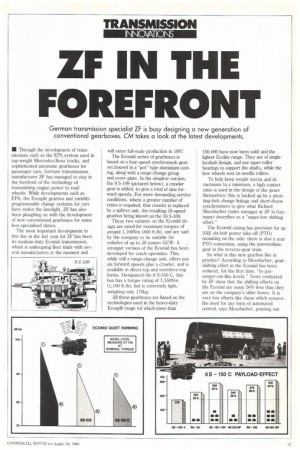
If you've noticed an error in this article please click here to report it so we can fix it.
German transmission specialist ZF is busy designing a new generation of conventional gearboxes. CM takes a look at the latest developments.
IN Through the development of transmissions such as the EPS system used in top-weight Mercedes-Benz trucks, and sophisticated automatic gearboxes for passenger cars, German transmissions manufacturer ZF has managed to stay in the forefront of the technology of transmitting engine power to road wheels. While developments such as EPS, the Ecosplit gearbox and variablyprogrammable change systems for cars have stolen the limelight, 'LP' has also been ploughing on with the development of new conventional gearboxes for some less-specialised duties.
The most important development in this line in the last year for ZF has been its medium-duty Ecomid transmission, which is undergoing fleet trials with several manufacturers at the moment and will enter full-scale production in 1987.
The Ecomid series of gearboxes is based on a four-speed synchromesh gearset housed in a "pot" type aluminium casting, along with a range-change group and cover plate. In the simplest version, the 9 S-109 (pictured below), a crawler gear is added, to give a total of nine forward speeds. For more demanding service conditions, where a greater number of ratios is required, that crawler is replaced by a splitter unit, the resulting 16-speed gearbox being known as the 16 S-109.
These two variants on the Ecomid design are rated for maximum torques of around 1,100Nm (800 ft.lb), and are said by the company to be suitable for vehicles of up to 38 tonnes GCW. A stronger version of the Ecomid has been . developed for coach operation. This, while still a range-change unit, offers just six forward speeds plus a crawler, and is available in direct-top and overdrive-top forms. Designated the 6 S-150 C, this box has a torque rating of 1,550Nm (1,100 ft.lb), but is extremely light, weighing only 170kg.
All these gearboxes are based on the technologies used in the heavy-duty Ecosplit range (of which more than 150,000 have now been sold) and the lighter Ecolite range. They are of singlelayshaft design, and use taper-roller bearings to support the shafts, while the free wheels rest on needle rollers.
To help keep weight inertia and dimensions to a minimum, a high contact ratio is used in the design of the gears themselves: this is backed up by a pivotting-fork change linkage and short-throw synchronisers to give what Richard Mossbacher (sales manager at ZF in Germany) describes as a "super-low shifting effort."
The Ecomid casing has provision for an SAE six-bolt power take-off (PTO) mounting on the side: there is also a rear PTO connection, using the intermediate gear in the reverse-gear train.
So what is this new gearbox like in practice? According to Mossbacher, gearshifting effort in the Ecomid has been reduced, for the first time, "to passenger-car-like levels." Tests conducted by ZF show that the shifting efforts on the Ecomid are some 50% less than they are on the company's older boxes. It is very low efforts like these which remove , the need for any form of automated control, says Mossbacher, pointing out