Retrostyled and Reuolutionary
Page 42
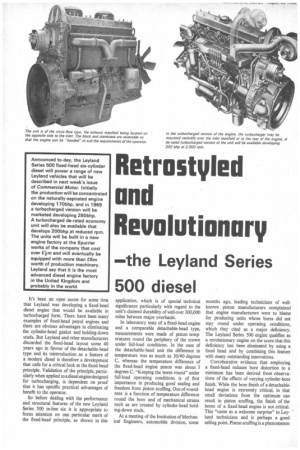
Page 43
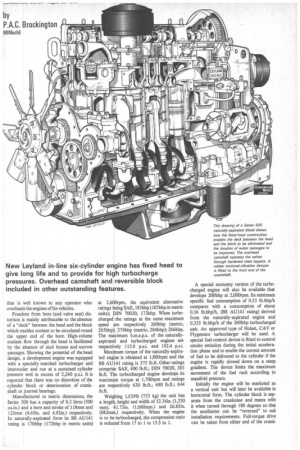
Page 44
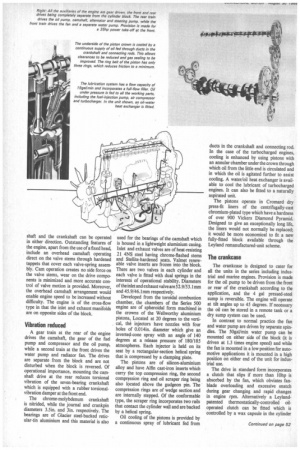
Page 54
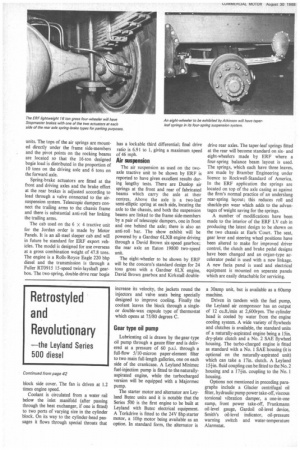
If you've noticed an error in this article please click here to report it so we can fix it.
—the Leyland Series 500 diesel
New Leyland in-line six-cylinder engine has fixed head to give long life and to provide for high turbocharge pressures. Overhead camshaft and reversible block included in other outstanding features.
Announced to-day, the Leyland Series 500 fixed-head six-cylinder diesel will power a range of new Leyland vehicles that will be described in next week's issue of Commercial Motor. initially the production will be concentrated on the naturally-aspirated engine developing 170bhp, and in 1969 a turbocharged version will be marketed developing 260bhp. A turbocharged de-rated economy unit will also be available that develops 200bhp at reduced rpm. The units will be built in a new engine factory at the Spurrier works of the company that cost over firn and will eventually be equipped with more than E6m worth of production machinery. Leyland say that it is the most advanced diesel engine factory in the United Kingdom and probably in the world.
It's been an open secret for some time that Leyland was developing a fixed-head diesel engine that would be available in turbocharged form. There have been many examples of fixed-head petrol engines and there are obvious advantages in eliminating the cylinder-head gasket and holding-down studs. But Leyland and other manufacturers discarded the fixed-head layout some 40 years ago in favour of the detachable-head type and its reintroduction as a feature of a modern diesel is therefore a development that calls for a critical look at the fixed-head principle. Validation of the principle, particularly when applied to a diesel engine designed for turbocharging, is dependent on proof that it has specific practical advantages of benefit to the operator.
So before dealing with the performance and structural features of the new Leyland Series 500 in-line six it is appropriate to focus attention on one particular merit of the fixed-head principle, as shown in this application, which is of special technical significance particularly with regard to the unit's claimed durability of well over 300.000 miles between major overhauls.
In laboratory tests of a fixed-head engine and a comparable detachable-head type, measurements were made of piston temperatures round the periphery of the crown under full-load conditions. In the case of the detachable-head unit the difference in temperature was as much as 30/40 degrees C, whereas the temperature difference of the fixed-head engine piston was about 3 degrees C. -Keeping the bores roundunder full-load operating conditions is of first importance in producing good sealing and freedom from piston scuffing. Out-of-roundness is a function of temperature difference round the bore and of mechanical strains such as are created by cylinder-head holding-down studs.
At a meeting of the Institution of Mechanical Engineers, automobile division, some
months ago, leading technicians of wellknown piston manufacturers complained that engine manufacturers were to blame for producing units whose bores did not stay round under operating conditions, which they cited as a major deficiency. The Leyland Series 500 engine qualifies as a revolutionary engine on the score that this deficiency has been eliminated by using a fixed head and by combining this feature with many outstanding innovations.
Corroborative evidence that employing a fixed-head reduces bore distortion to a minimum has been derived from observations of the effects of varying cylinder-bore finish. While the bore finish of a detachablehead engine is extremely critical, in that small deviations from the optimum can result in piston scuffing, the finish of the bores of a fixed-head engine is not critical. This -came as a welcome surprise" to Leyland technicians and is perhaps a good selling point. Piston scuffing is a phenomenon
that is well known to any operator who overhauls the engines of his vehicles.
Freedom from bore (and valve seat) distortion is mainly attributable to the absence of a "deck" between the head and the block which enables coolant to be circulated round the upper end of the bore. High-volume coolant flow through the head is facilitated by the absence of stud bosses and narrow passages. Showing the potential of the head design, a development engine was equipped with a specially matched turbocharger and intercooler and run at a sustained cylinder pressure well in excess of 2,240 p.s.i. It is reported that there was no distortion of the cylinder block or deterioration of crankshaft or journal bearings.
Manufactured to metric dimensions, the Series 500 has a capacity of 8.2 litres (500 cu.in.) and a bore and stroke of 118mm and 125mm (4.65in. and 4.92in.) respectively. In naturally-aspirated form its BS AU141 rating is 170bhp (I72bhp in metric units) at 2,600rpm, the equivalent alternative ratings being SAE, I83bhp (185bhp in metric units); DIN 70020, I73bhp. When turbocharged the ratings at the same maximum speed are respectively 260bhp (metric, 265bhp); 279bhp (metric, 284bhp); 266bhp. The maximum b.m.e.p.s. of the naturally aspirated and turbocharged engines are respectively 113.9 p.s.i. and 192.4 p.s.i.
Maximum torque of the naturally-aspirated engine is obtained at 1,800rpm and the BS AU141 rating is 375 lb.ft. Other ratings comprise SAE, 400 lb.ft.; DIN 70020, 383 lb.ft. The turbocharged engine develops its maximum torque at 1,700rpm and ratings are respectively 630 lb.ft.; 680 lb.ft.; 644 lb.ft.
Weighing 1,6391b (753 kg) the unit has a length, height and width of 52.36in. (1,330 mm). 41.73in. (1.060mm.) and 26.85in. (682mm.) respectively. When the engine is to be turbocharged, the compression ratio is reduced from 17 to 1 to 15.5 to 1. A special economy version of the turbocharged engine will also be available that develops 200bhp at 2,000rpm. Its minimum specific fuel consumption of 0.33 lb.bhp/h compares with a consumption of about 0.36 lb.bhp/h, (BS AU141 rating) derived from the naturally-aspirated engine and 0.335 lb.bhp/h of the 260bhp turbocharged unit. An approved type of Holset, CAV or Flygmotor turbocharger will be used. A special fuel-control device is fitted to control smoke emission during the initial acceleration phase and to enable the correct amount of fuel to be delivered to the cylinder if the engine is rapidly slowed down on a steep gradient. The device limits the maximum movement of the fuel rack according to manifold pressure.
Initially the engine will be marketed as a vertical unit but will later be available in horizontal form. The cylinder block is separate from the crankcase and mates with it when turned through 180 degrees so that the auxiliaries can be "reversed" to suit installation requirements. Full-torque drive can be taken from either end of the crank shaft and the crankshaft can be operated in either direction. Outstanding features of the engine, apart from the use of a fixed head, include an overhead camshaft operating direct on the valve stems through hardened tappets that cover each valve-spring assembly. Cam operation creates no side force on the valve stems, wear on the drive components is minimized and more accurate control of valve motion is provided. Moreover, the overhead camshaft arrangement would enable engine speed to be increased without difficulty. The engine is of the cross-flow type in that the inlet and exhaust manifolds are on opposite sides of the block.
Vibration reduced A gear train at the rear of the engine drives the camshaft, the gear of the fuel pump and compressor and the oil pump, while a second train at the front drives the water pump and radiator fan. The drives are separate from the block and are not disturbed when the block is reversed. Of operational importance, mounting the camshaft drive at the rear reduces torsional vibration of the seven-bearing crankshaft which is equipped with a rubber torsionalvibration damper at the front end.
The chrome-molybdenum crankshaft is nitrided, while the journal and crankpin diameters 3.5in. and 3in. respectively. The bearings are of Glacier steel-backed reticular-tin aluminium and this material is also used for the bearings of the camshaft which is housed in a lightweight aluminium casing. Inlet and exhaust valves are of heat-resisting 21 4NS steel having chrome-flashed stems and Stellite-hardened seats. Valmet renewable valve inserts are frozen into the block. There are two valves in each cylinder and each valve is fitted with dual springs in the interests of operational stability. Diameters of the inlet and exhaust valve are 52.9/53.1mm and 45.9/46.1mm respectively.
Developed from the toroidal combustion chamber, the chambers of the Series 500 engine are of spheroidal form machined in the crowns of the Wellworthy aluminium pistons, Located at 20 degrees to the vertical, the injectors have nozzles with four holes of 0.014in. diameter which give an inverted-cone spray with an angle of 140 degrees at a release pressure of 180/185 atmospheres. Each injector is held on its seat by a rectangular-section helical spring that is compressed by a clamping plate.
The pistons are of silicon-aluminium alloy and have Alfin cast-iron inserts which carry the top compression ring, the second compression ring and oil scraper ring being also located above the gudgeon pin. The compression rings are of wedge section and are internally stepped. Of the conformable type, the scraper ring incorporates two rails that contact the cylinder wall and are backed by a helical spring.
Oil cooling of the pistons is provided by a continuous spray of lubricant fed from ducts in the crankshaft and connecting rod. In the case of the turbocharged engines, cooling is enhanced by using pistons with an annular chamber under the crown through which oil from the little end is circulated and in which the oil is agitated further to assist cooling. A water/oil heat exchanger is available to cool the lubricant of turbocharged engines. It can also be fitted to a naturally aspirated unit.
The pistons operate in Cromard dry press-fit liners of the centrifugally-cast chromium-plated type which have a hardness of over 900 Vickers Diamond Pyramid. Designed to give an exceptionally long life, the liners would not normally be replaced; it would be more economical to fit a new fully-fitted block available through the Leyland remanufactured-unit scheme.
The crankcase The crankcase is designed to cater for all the units in the series including industrial and marine engines. Provision is made for the oil pump to be driven from the front or rear of the crankshaft according to the application, and the 4 gal pressed-steel sump is reversible. The engine will operate at tilt angles up to 45 degrees. If necessary the oil can be stored in a remote tank or a dry sump system can be used.
In contrast to normal practice the fan and water pump are driven by separate spindles. The 50gal/min water pump can be mounted on either side of the block (it is driven at 1.3 times engine speed) and while the fan is mounted in a low position for automotive applications it is mounted in a high position on either end of the unit for industrial use.
The drive in standard form incorporates a clutch that slips if more than 10hp is absorbed by the fan, which obviates fanblade overloading and excessive snatch during gear changing and rapid changes in engine rpm. Alternatively a Leylandpatented thermostatically-controlled oiloperated clutch can be fitted which is controlled by a wax capsule in the cylinder block side cover. The fan is driven at 1.2 times engine speed.
Coolant is circulated from a water rail below the inlet manifold (after passing through the heat exchanger, if one is fitted) to two ports of varying size in the cylinder block. On its way to the cylinder-head passages it flows through special throats that increase its velocity, the jackets round the injectors and valve seats being specially designed to improve cooling. Finally the coolant leaves the block through a singleor double-wax capsule type of thermostat which opens at 75/80 degrees C.
Gear type oil pump
Lubricating oil is drawn by the gear type oil pump through a gauze filter and is delivered at a pressure of 60 p.s.i. through a full-flow 5/10-micron paper-element filter to two main full-length galleries, one on each side of the crankcase. A Leyland Minimec fuel-injection pump is fitted to the naturallyaspirated engine, while the turbocharged version will be equipped with a Majormec pump.
The starter motor and alternator are Leyland Butec units and it is notable that the Series 5b0 is the first engine to be built at Leyland with Butec electrical equipment A Torkdrive is fitted to the 24V 8hp starter motor, a 10hp motor being available as an option. In standard form, the alternator is a 30arnp unit, but is available as a 60amp machine.
Driven in tandem with the fuel pump, the Leyland air compressor has an output of 12 cu.ft./min at 2,600rpm. The cylinder head is cooled by water from the engine cooling system. A wide variety of flywheels and clutches is available, the standard units of a naturally-aspirated engine being a 15in. dry-plate clutch and a No. 2 SAE flywheel housing. The turbo-charged engine is fitted as standard with a No. 1 SAE housing (it is optional on the naturally-aspirated unit) which can take a 17in. clutch. A Leyland 15+in. fluid coupling can be fitted to the No. 2 housing and a 17-,tin. coupling to the No. 1 housing.
Options not mentioned in preceding paragraphs include a Glacier centrifugal oil filter, hydraulic pump power take-off, viscous torsional vibration damper, a one-in-one sump, front power take-off, Frankmarm oil-level gauge, Gardoil oil-level device, Smith's oil-level indicator, oil-pressure warning switch and water-temperature Alarmstat.