BOO TIME for BOD BUILDERS
Page 121
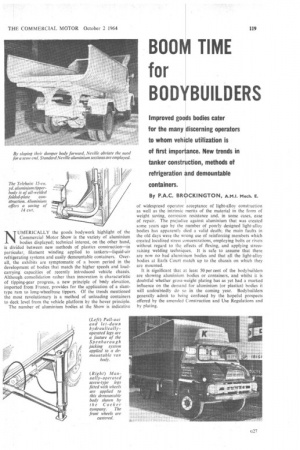
Page 122
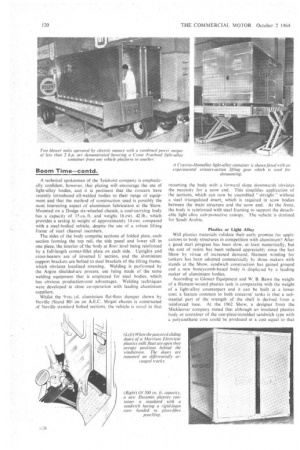
Page 123
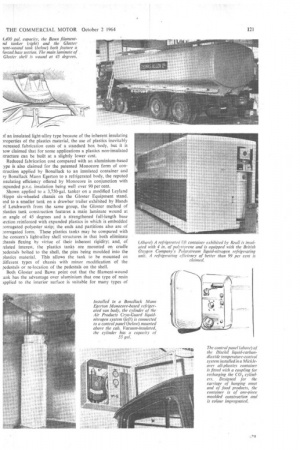
Page 124
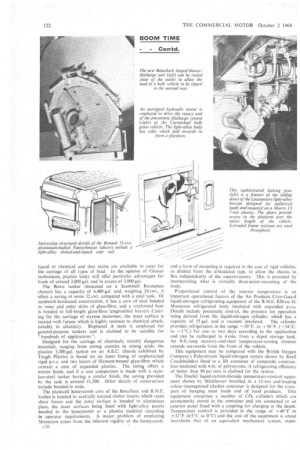
Page 125
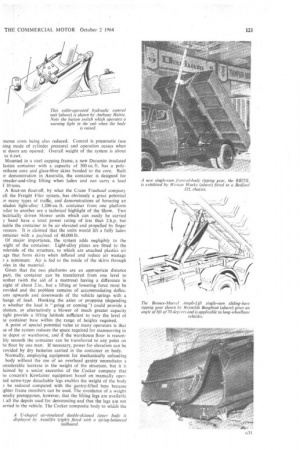
Page 126
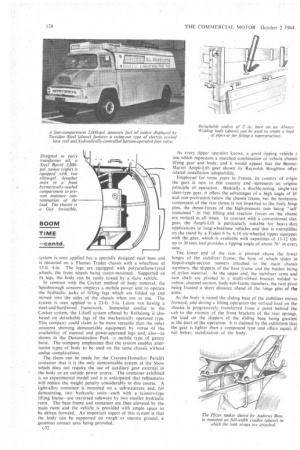
If you've noticed an error in this article please click here to report it so we can fix it.
By P.A.C. BR CKINGTON, Mech. E.
NUMERICALLY the goods bodywork highlight of the Commercial Motor Show is the variety of. aluminium bodies displayed; technical interest, on the other hand, is divided between new methods of plastics construction—in particular, filament winding applied to tankers—liquid-air refrigerating systems and easily demountable containers. Overall, the exhibits are symptomatic of a boom period in the development of bodies that match the higher speeds and loadcarrying capacities of recently introduced vehicle chassis. Although. consolidation rather than innovation is characteristic of tipping-gear progress, a new principle of body elevation, imported from France, provides for the application of a slanttype ram to long-wheelbase tippers. Of the trends mentioned the most revolutionary is a method of unloading containers to deck level from the vehicle platform by the hover principle.
The number of aluminium bodies at the Show is indicative of widespread operator acceptance of light-alloy construction as well as the intrinsic merits of the material in the form of weight saving, corrosion resistance and, in some cases, ease of repair. The prejudice against aluminium that was created some years ago by the number of poorly designed light-alloy bodies has apparently died a valid death; the main faults in the old days were the wrong use of reinforcing members which created localized stress concentrations, employing bolts or rivets without regard to the effects of flexing, and applying stressraising welding techniques. it is safe to assume that there are now no bad aluminium bodies and that all the light-alloy bodies at Earls Court match up to the chassis on which they are mounted.
It is significant that at least 50 per cent of the bodybuilders are showing aluminium bodies or containers, and whilst it is doubtful whether gross-weight plating has as yet had a marked influence on the demand for aluminium (or plastics) bodies it will undoubtedly do so in the coming year. Bodybuilders generally admit to being confused by the hopeful prospects offered by the amended Construction and Use Regulations and by plating. A technical spokesman of the Telehoist company is emphatically confident, however, that plating will encourage the use of light-alloy bodies, and it is pertinent that the concern have recently introduced all-welded bodies to their range of equipment and that the method of construction. used is possibly the most interesting aspect of aluminium fabrication at the Show. Mounted on a Dodge six-wheeled chassis,.a coal-carrying body has a capacity of 15 Cu. ft.. and weighs• 16 cwt. 42 lb., which provides a saving in weight of approximately 14 cwt. compared with a steel-bodied vehiele, despite the use of a robust lifting frame of steel channel members,
The sides of the body comprise sections of folded plate, each section forming the top rail, the side panel and lower sill in one piece, the interior of the body at floor level being reinforced by a full-length corner-Fillet plate on each side. Uprights and cross-bearers are of inverted .0 section, and the aluminium support brackets are bolted to steel brackets of the lifting frame, which obviates localized stressing. Welding is performed by the Argon shielded-arc process, use being made of the same welding equipment that is employed for steel bodies, which has obvious production-cost advantages. Welding techniques were developed in close co-operation with leading aluminium
suppliers.
Whilst the 9-cu. yd. aluminium flat-floor dumper shown by Neville (Stand SO on an A.E.C. Mogul chassis is constructed of Neville standard bolted sections, the vehicle is novel in that
mounting the body with a forward slope downwards obviates the necessity for a scow end, This simplifies application of the sections, which can now be assembled " straight " without a steel triangulated insert, which is required in scow bodies between the main structure and the scow end. At the front. the body is reinforced with steel framing to support the detachable light alloy cab-protective canopy, The vehicle is destined for Saudi Arabia.
Plastics or Light Alloy Will plastics materials validate their early promise for applications to body structures in competition with aluminium? After a good start progress has been slow, at least numerically, but the cost of resins has been reduced appreciably since the last Show by virtue of increased demand, filament winding for tankers has been adopted commercially by three makers with stands at the Show, sandwich construction has gained ground and a new honeycomb-based body is displayed by a leading maker of aluminium bodies.
According to Gloster Equipment and W. B. Bawn the weight of a filament-wound plastics tank is comparable with the weight of a light-alloy counterpart and it can be built at a lower cost; a feature common to both concerns' tanks is that a substantial part of the strength of the shell is derived from a reinforced base. At the 1962 Show, a designer from the MickIeover company stated that although an insulated plastics body or container of the one-piece-moulded sandwich type with a polyurethane core could be produced at a cost equal to that
)1' an insulated light-alloy type because of the inherent insulating 3roperties of the plastics material, the use of plastics inevitably ncreased, fabrication costs of a standard box body, but it is low claimed that for some applications a plastics non-insulated itructure can be built at a slightly lower cost.
Reduced fabrication cost compared with an aluminium-based .ype is also claimed for the patented Monocore form of con;truction applied by BonalIack to an insulated container and )3/ Bonallack Mann Egerton to a refrigerated body, the reputed nsulating efficiency offered by Monocore in conjunction with :.xpanded p.v.c. insulation being well over 90 per cent.
Shown applied to a 3,750-gal. tanker on a modified Leyland Hippo six-wheeled chassis on the Gloster Equipment stand, md to a smaller tank on a drawbar trailer exhibited by Hands )f Letchworth from the same group, the Gloster method of lastics tank construction features a main laminate wound at tri angle of 45 degrees and a strengthened full-length base iection reinforced with expanded plastics in which is embedded iorrugated polyester strip; the ends and partitions also are of i-orrugated form. These plastics tanks may be compared with he concern's light-alloy shell structures in that both eliminate ;hassis flexing by virtue of their inherent rigidity; and, of related interest, the plastics tanks are mounted on cradle ?edestals bolted to the shell, the pins being moulded into the llastics material. This allows the tank to he mounted on Jitferent types of chassis with minor modification of the ?edestals or re-location of the pedestals on the shell, Both Gloster and Bawn point out that the filament-wound ank has the advantage over aluminium that one type of resin ipplied to the interior surface is suitable for many types of liquid or chemical and that resins are available to eater for the carriage of all types of load. In the opinion of Gloster technicians, plastics tanks will offer particular advantages for loads of around 2,000 gal. and in excess of 3,000 gal.
The Bawn tanker (mounted on a Scartimell Routeman chassis) has a capacity of 4,400 gal. and, weighing 28 cwt., it offers asaving of some 32 cwt. compared with a steel tank. Of sandwich-laminated construction, it has a core of sisal bonded to inner and outer skins of glass-fibre, and a reinforced base is bonded to full-length glass-fibre longitudinal bearers. Catering for the carriage of styrene monomer, the inner surface is treated with furane which is highly resistant to chemical attack, notably to alkalinity. Bisphenol A resin is employed for general-purpose tankers and is claimed to be suitable for "hundreds of applications ".
Designed for. the carriage of chemicals, notably dangerous materials, ranging from strong caustics to strong acids, the plastics 3,300 gal. tanker on an A.E.C. chassis exhibited by Tough. Plastics is based on an inner lining of unplasticized rigid p.v.c. and two layers of filament-wound glass-fibre which contain a core of expanded plastics. The lining offers a mirror finish, and if a cost comparison is made with a stainless-steel tanker having a similar finish, the saving provided by the tank is around £1,500. Other details of construction include bonded-in ,ends.
The plastic& honeycomb core of the Bonallack and B.M.E. bodies is bonded to centrally located, timber inserts which resist shear forces and the outer surface is bonded to aluminium plate, the inner surfaces being lined with light-alloy panels bonded to the honeycomb or a plastics material according to operator requirements. A major problem of employing Monocore arises from the inherent rigidity of the honeycomb.
(;30 and a form of mounting is required in the case of rigid vehicles, as distinct from the articulated type, to allow the chassis to flex independently of the superstructure. This is provided by incorporating what is virtually three-point-mounting of the body.
Proportional control of the interior temperature is an important operational feature of the Air Products Cryo-Guard liquid-nitrogen refrigerating equipment of the B.M.E. 820-cu.-ft. Monocore refrigerated body insulated with expanded p.v.c. Details include pneumatic control, the pressure for operation being derived from the liquid-nitrogen cylinder, which has a capacity of 55 gal. and is vacuum insulated. The cylinder provides refrigeration in the range —30'F. to +30°F. (-34°C. to —PC.) for one to two days according to the application and can be recharged in 4min. from a depot storage tank. An 8-ft.-long mercury-and-steel temperature-sensing element extends rearwards from the front of the vehicle.
This equipment may be compared with the British Oxygen Company's Polarstream liquid-nitrogen system shown by Reall Coachbuilders fitted to a lift container of composite construction insulated with 4-in, of polystyrene. A refrigerating efficiency of better than 90 per cent is claimed for the system.
The Dischil liquid-carbon-dioxide temperature-control equipment shown by Mickleover installed in a 12-ton end-loading colour-impregnated plastics container is designed for the transport of hanging meat loads and of food products. This equipment comprises a number of CO2 cylinders which are permanently stored in the container and are connected to an exterior panel fitted with a coupling for charging at the depot. Temperature control is provided in the range of +40°F to +32°F (4-5°C to 0°C) and the cost of the equipment is about two-thirds that of an equivalent mechanical system, main
!ranee costs being also reduced. Control is pneumatic (use eing made of cylinder pressure) and operation ceases when le doors are opened. Overall weight of the system is about to .6 cwt.
Mounted in a steel capping frame, a new Duramin insulated Iastics container with a capacity of 500 cu. ft. has a polyrethane .core and glass-fibre skins bonded to the core. Built 31demonstration in Australia, the container is designed for areader-and-sling lifting when laden and can carry a load f 10 tons.
A float-on float-off, by what the Crane Fruehauf company all the Freight Flier system, has obviously a great potential )r many types of traffic, and demonstrations of hovering an nladen 1,200-cu. ft container from one platform .ailer to another are a technical highlight of the Show. Two tectrically driven blower units which can easily be carried y .hand have a total power rating of less than 2 h.p. but nable the container to be air elevated and propelled by finger ressure. It is claimed that the units would lift a fully laden ontainer with a payload of 40,00016.
Of major importance, the system adds negligibly to the 7eight of the container. Light-alloy plates are fitted to the nderside of the structure, to which are attached plastics air ags that form skirts when inflated and reduce air wastage ) a minimum. Air is fed to the inside of the skirts through oles in the material.
Given that the two platforms are an appropriate distance part, the container can be transferred from one level to nother (with the aid of a mattress) having a difference in eight of about 2 in., but a lifting or lowering force must he rovided and the problem remains of accommodating deflecLons upwards and downwards of the vehicle springs with a hange of load. Hooking the axles or propping (depending n whether the load is "going or coming ") could provide a olution, or alternatively a blower of much greater capacity light provide a lifting latitude sufficient to vary the level of
le container base within the range of heights required. . A point of special potential value to many operators is that se of the system reduces the space required for manceuvring in le depot or warehouse, and if the warehouse floor is reasonbly smooth the container can be transferred to any point on he floor by one man. If necessary, power for elevation can be rovided by dry batteries carried in the container or body. Normally, employing equipment for mechanically unloading body without the use of an overhead gantry necessitates a onsiderable increase in the weight of the structure, but it is !aimed by a senior executive of the Cocker company that ise concern's Kewtainer equipment based on manually operted screw-type detachable legs enables the weight of the body 3 be reduced compared with the gantry-lifted type because ighter frame members can be used. The avoidance of a weight erialty presupposes, however, that the lifting legs are available t all the depots used for demounting and that the legs are not arried in the vehicle. The Cocker composite body to which the system is seen applied has a specially designed steel base and is mounted on a Thames Trader chassis with a wheelbase of 13 ft. 4 in. The legs are equipped with polyurethane-tyred wheels, the front wheels being castor-mounted. Supported on its legs, the body can be easily towed by a slave vehicle.
In contrast with the Cocker method of body removal, the Spenborough concern employs a mobile power unit to operate the hydraulic jacks of lifting legs which are folded up and moved into the sides of the chassis when not in use. The system is seen applied to a 23-ft. 5-in. Luton van having a steel-and-hardwood framework. Somewhat similar to the Cocker system, the Liftoff system offered by Rollalong is also based on detachable legs of the mechanically operated type. This company could claim to be more versatile than the other concerns showing demountable equipment by virtue of the availability of manual and power-operated legs and, also—as shown in the Demonstration Park—a mobile type of gantry hoist. The company emphasizes that the system enables alternative types of body to be used on the same chassis without undue complications.
The claim can be made for the Cravens-Homalloy Paralift container that it is the only demountable system at the Show which does not require the use of auxiliary gear external to the body or an outside power source. The container exhibited is an experimental model and it is anticipated that refinements will reduce the weight penalty considerably in due course. A light-alloy container is mounted on a sub-structure and, for demounting, two hydraulic units—each with a scissors-type lifting frame—are traversed sideways by two smaller hydraulic rams. The base framc and container are then elevated by the main rams and the vehicle is provided with ample space to be driven forward. An important aspect of this system is that the body can be supported on rough or uneven ground, a generous contact area being provided.
632 As every tipper operator knows, a good tipping vehicle i one which represents a matched combination of vehicle chassis lifting gear and body, and it would appear that the Rennes Ivlarrel Ampli-Lift gear shown by Reynolds Boughton offer related installation adaptability.
Employed for some years in France, its country of origin the gear is new to this country and represents an origina principle of operation. Basically a double-acting, single-ran slant-type gear, it offers the advantages of a high angle of lif and non-protrusion below the chassis frame, but the horizonta component of the ram thrust is not imparted to the body hingt pins, the thrust-forces of the high-pressure ram being " self contained" in that lifting and reaction forces on the chassi! are vertical at all times. In contrast with a conventional slan. gear, the Ampli-Lift is particularly suitable for heavy-dut3 applications to long-wheelbase vehicles and this is exemplifier on the stand by a Foden 6 by 6/10 six-wheeled tipper equipper: with the gear, which is available with capacities of 11-12 tom up to 30 tons and provides a tipping angle of about 70° in every case.
The lower end of the ram is pivoted above the lower hinges of the stabilizer frame, the base of which slides in lipped-angle-section runners attached to the main chassis members, the slippers of the base frame and the bushes being of nylon material. At the upper end, the stabilizer arms and ram shaft are pivoted to a multi-ribbed bracket welded to robust. channel-section, body-sub-frame members, the ram pivot being located a short distance ahead of the hinge pins of the arms.
As the body is raised the sliding base of the stabilizer moves forward, and during a lifting operation the vertical load on the chassis is progressively transferred from a point behind the cab to the vicinity of the front brackets of the rear springs, the load on the slippers of the sliding base being greatest at the start of the operation. It is claimed by the exhibitors that the gear is lighter than a compound type and offers equal, if not better, stabilization of the body.