COMFORT
Page 108

Page 109
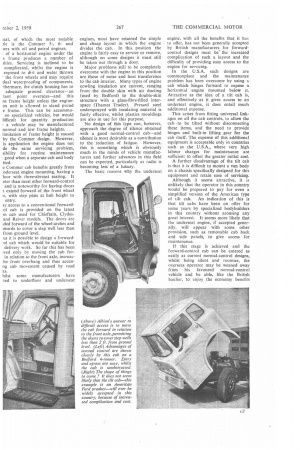
Page 110
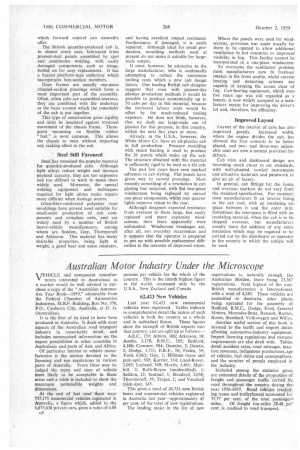
If you've noticed an error in this article please click here to report it so we can fix it.
versus
UTILITY
Forward-control Cabs Have Not Reached a Stage Yet Where They Can Be Generally. Accepted by Operators Overseas By Anthony Ellis
IN considering comfort for the driver— a vital matter in vehicle operation—it is difficult to 'explain the evolution of the conventional forwardcontrol cab in which the engine bisects the space. Its evolution and popularity are the result largely of the need for maximum manoeuvrability on overcrowded roads and of legal limitations on overall vehicle lengths.
This is the great advantage of the forward-control layout. Cab depth can be reduced allowing the maximum body length to be accommodated within the minimum overall length. Other than this it has precious little to offer.
Overseas, where climatic conditions and inferior roads make greater, demands on the driver, normal-control cabs are still by far the more popular. Normal control places the driver well behind the front axle,, which increases comfort. It also solves the problem of providing easy entry to the cab. Cab floor heights are not determined by wheel and tyre dimensions and can be low, whilst running boards can be fitted inside the overall width of the vehicle to provide effective intermediate steps.
Cab access is the major difficulty with
most forward-control designs. Doors over the front wheels make hub-mounted step-rings or awkwardly,..;.placed, steps essential without ever providing really easy access. This layout rules out such a vehicle for effective local delivery work.
G6
Particularly for export, three-abreast seating is most desirable. It is difficult, if not impossible, to provide in forwardcontrol cabs into which the engine compartment impinges. but it is simply incorporated in a normal-control cab where the .floor is flat and a full-width bench seat can be employed.
A criticism of normal control is that forward vision for the driver can never be as good as that achieved with a flat fronted forward-control cab. This is certainly so, but recent developments in normal control, notably by Bedford in the new range introduced last year. have shown that by lowering bonnet lines and deepening windscreens, vision can be much improved.
A major contribution which forward control makes to good design is in permitting perfect axle loadings, particularly on a two-axled vehicle with twin rear Wheels. Such distribution cannot he arrived at easily with normal-control designs.
Different requirements force British manufacturers, who wish to have an equal footing in both the home and export markets, to produce similar vehicles with both forward and normal control. Overseas, the demand is still in the main for normal control, whilst at home forward control is in the ascendancy, with normal-control vehicles still popular for local delivery work and other applications where body space is not the most important requirement and can be sacrificed to simplify the drivers work.
For simplicity I have divided cab types. up to this point, into normal-control and forward-control designs in which the engine bisects the cab. However, some manufacturers have attempted to overcome the problems which forward control presents by opting for semiforward-control layouts or underfloor and underseat engines.
The latest example of semi-forwardcontrol is that used by Ford for the Thames Trader range. In this design less than half the engine is inside the cab, the forward portion of .it being located under a short bonnet.
Although the doors are still over the wheels, there is more space in the cab and a two-man passenger seat is provided. Little body space is lost and vision ahead is almost as good as that provided by the flat front of the forwardcontrol cab. As there is less engine cowling area inside the cab it is easier to provide a reasonable degree of silence.
For maximum comfort in a forwardmounted cab, the full-forward-control layout is obviously the nearest approach to the idea so far 'made in Britain. Such a layout can be Obtained by mounting a horizontal engine under the chassis frame behind_the cab, as has been .done by Rowe, Fodert..Albion and others, or by locating the engine partly under the ,eat, of which the most notable sle is the Commer 5-, 6and iers with oil and petrol engines_ of a horizontal engine under the s frame produces a number of ilties. Servicing is inclined to be complicated, whilst the engine is exposed to dirt and water thrown • the front wheels and may require dual waterproofing of components. ihermore, the clutch housing has to adequate ground clearance—an • tant point overseas—and this is frame height unless the engineox unit is allowed to stand proud e frame. This can be accommoon specialized vehicles, but would lifficult for quantity production ; a vehicle may be manufactured normal and low frame heights.
limitation of frame height is caused by the Commer design. However, is application the engine does not de the same servicing problem, sibility for routine maintenance good when a separate cab and body tted.
e Commer cab benefits greatly from nderseat engine mounting, having a Icor with three-abreast seating. It eter than most other forward-control and is noteworthy for having doors I extend forward of the front wheel • with step pans at hub height to entry.
sy access to a conventional forwardol cab is provided on the latest m cab used for Chieftain, Clydesand Reiver models. The doors are ided forward of the wheel-arches and wards to cover a step well less than from ground level.
us it is possible to design a forward e l cab which would be suitable for delivery work. So far this has been :ved only by moving the cab forin relation to the front axle, increas:he front overhang and thus accenng cab movement caused by road s.
hilst some manufacturers have /ed to underfloor and underseat engines, most have retained the simple and cheap layout in which the engine divides the cab. In this position the engine is fairly easy to service or remove, although on some designs it must still be taken out through a door.
Major problems still to be completely overcome with the engine in this position are those of noise and heat transference to the cab interior. Many types of engine cowling insulation are current, ranging from the double skin with air ducting (used by Bedford) to the double-skin structure with a glass-fibre-filled interspace (Thames Trader). Pressed steel undersprayed with insulating material is fairly effective, whilst plastics mouldings are also in use for this purpose. • No design of this type can, however, approach the degree of silence obtained with a good normal-control cab—and silence is most desirable as a contribution to the reduction of fatigue. However, this is something which is obviously much in the minds of vehicle manufacturers and further advances in this field can be expected, particularly as radio is becoming less" of a luxury.
The basic reasons why the underseat engine, with all the benefits that it has to offer, has not been generally accepted by British manufacturers for forwardcontrol designs must be' the increased complication of such a layout and the difficulty of providing easy access to the engine for servicing.
In the U.S.A. such designs are commonplace and the maintenance problem has been overcome by using a cab which hinges forward to expose a horizontal engine mounted below it. Attractive as the idea of a tilt cab is, and effectively as it gives access to an underseat engine, it does entail much additional expense.
This arises from fitting universal link. ages on all the cab controls, to allow the cab .to be tilted without disconnecting these items, and the need to provide hinges and built-in lifting gear for the cab itself. The expense of this additional equipment is acceptable only in countries such as the U.S.A., where very high labour charges for maintenance are sufficient to offset the greater initial cost.
A further disadvantage of the tilt cab is that it is difficult to mount a van body on a chassis specifically designed for this equipment and retain ease of servicing.
Although it seems attractive, it is unlikely that the operator in this country would be prepared to pay for even a simplified version of the American type of tilt cab. An indication of this is that tilt cabs have been on offer for some years by specialized bodybuilders in this country without arousing any great interest. It seems more likely that the underseat engine, if accepted generally, will appear with some other provision, such as removable cab back and side panels, to give access for maintenance.
If this stage is achieved and the forward-control cab can be entered as easily as current normal-control designs, whilst being silent and roomier, the overseas operator may be weaned away from his favoured normal-control vehicle and be able, like the British haulier, to enjoy the economy benefits which forward control can assuredly offer.
The British quantity-produced cab is, in almost every case, fabricated from pressed-steel panels assembled by spot and continuous welding, with easily damaged components, such as wings, bolted on for easy replacement. It has a braced platform-type undertray which incorporates box-section members.
Door frames are usually one-piece channel-section pressings which form a most important part of the assembly. Often, when cabs are assembled overseas, they are combined with the undertray as the basis around which the remainder of the cab is put together.
This type of construction gives rigidity and must be insulated against torsional movement of the chassis frame. Threepoint mounting on flexible rubber " feet " is most common. This allows the chassis to twist without imparting any racking effect to the cab.
Steel Still Favoured
Steel has remained the popular material for quantity-produced cabs. Although light alloys reduce weight and increase payload capacity, they are too expensive and too difficult to work to make them widely used. Moreover, the special welding equipment and techniques required for light alloys make repairs more difficult when damage occurs.
Glass-fibre-reinforced polyester resin mouldings have proved most suitable for small-scale production of cab components and complete cabs, and are widely used by a number of British heavy-vehicle manufacturers, among whom are Seddon, Guy, Thornycroft and Atkinson. This material has many desirable properties, being light in weight, a good heat and noise insulator, and having excellent impact resistance. Furthermore. if damaged, it is easily repaired. Although ideal for small production, moulding methods used at present do not make it suitable for largescale output.
It must, however, be attractive to the large manufacturer, who is continually attempting to reduce the enormous tooling costs which a new cab design incurs. One leading British cab designer suggests that even with present-day plastics production methods it would be possible to produce economically up to 50 cabs per day in this material, because the increased labour costs would be offset by the much-reduced tooling expenses. He does not think, however, that we shall see large-scale use of plastics for this purpose, in this country, within the next five years or more.
Already, in the U.S.A., however, the White Motor Co. have an all-plastics cab in full production. Pressure moulding with steam heating is used to produce the 36 panels which make up the cab. The structure obtained with this material is sufficiently rigid to be used as a tilt cab.
The past few years have seen marked advances in cab styling. Flat panels have given way to curved pressings. Most recently something of a revolution in cab glazing has occurred, with flat two-piece windscreens being replaced by curved one-piece components, whilst rear quarter lights improve vision to the rear.
Although designers expected resistance from overseas to these large, less easily replaced and more expensive windscreens, their fears apparently were unfounded. Windscreen breakages are, after all, not everyday occurrences and it appears that the operator is prepared to put up with possible replacement difficulties in the interests of improved vision. Where flat panels were used for windscreens, provision was made usually for them to be opened to allow additional ventilation in hot countries or improved visibility in fog. This facility cannot be incorporated in a one-piece windscreen.
To overcome the ventilation problem most manufacturers now fit fresh-air intakes in the front scuttle, whilst current heating and demisting systems are capable of keeping the screen clear of fog. Cab-heating equipment, which even five years ago was still regarded as a luxury, is now widely accepted as a satisfactory means for improving the driver's lot and, therefore, his efficiency.
Improved Layout
Layout of the interior of cabs has also improved greatly. Increased width, where the engine divides the cab, has allowed the foot controls to be better placed, and twoand three-way adjustable seats are now a normal provision for drivers.
Cab trim and dashboard design are becoming much closer to car standards, with well-situated, cowled instruments and attractive materials and paintwork to give an air of luxury.
In general, cab fittings for the home and overseas markets do not vary from ' the standard specification. For instance. most manufacturers fit an interior lining to the cab roof, with an insulating airspace between it and the outer skin. Sometimes the interspace is filled with an insulating material, when the cab is to be shipped overseas, but manufacturers usually leave the addition of any extra insulation which may be required to be carried out by the distributor or operator in the country in which the vehicle will be used.