PARTI CU L A R
Page 40
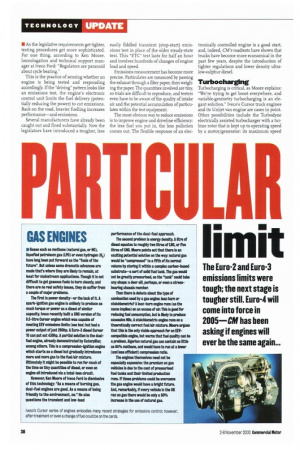
Page 41
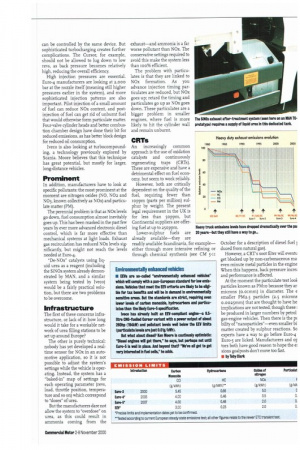
If you've noticed an error in this article please click here to report it so we can fix it.
• As the legislative requirements get tighter, testing procedures get more sophisticated. For one thing, according to Ken Moore, homologation and technical support manager at Iveco Ford: "Regulators are paranoid about cycle beating."
This is the practice of sensing whether an engine is being tested and responding accordingly. if the "driving" pattern looks like an emissions test, the engine's electronic control unit limits the fuel delivery (potentially reducing the power) to cut emissions. Back on the road, heavier fuelling increases performance—and emissions.
Several manufacturers have already been caught out and fined substantially. Now the legislators have introduced a tougher, less easily fiddled transient (stop-start) emissions test in place of the older steady-state test. This "ETC" test lasts for half an hour and involves hundreds of changes of engine load and speed.
Emissions measurement has become more precise. Particulates are measured by passing the exhaust through a filter paper, then weighing the paper. The quantities involved are tiny, so trials are difficult to reproduce, and testers even have to be aware of the quality of intake air and the potential accumulation of particulates within the test equipment.
The most obvious way to reduce emissions is to improve engine and driveline efficiency: the less fuel you put in, the less pollution comes out. The flexible response of an elec tronically controlled engine is a good start, and, indeed, CM's roadtests have shown that trucks have become more economical in the past few years, despite the introduction of tighter regulations and lower density ultralow-sulphur diesel,
Turbocharging
Turbocharging is critical, as Moore explains: We're trying to get boost everywhere, and variable-geometry turbocharging is an elegant solution," Iveco's Cursor truck engines and its [hill et van engine are cases in point. Other possibilities include the Turbodyne electrically assisted turbocharger with a turbine rotor that is kept up to operating speed by a motor/generator: its maximum speed can be controlled by the same device. But sophisticated turbocharging creates further complications. The Cursor, for example, should not be allowed to lug down to low revs, as back pressure becomes relatively high, reducing the overall efficiency.
High injection pressures are essential. Euro-4 manufacturers are looking at 2,000 bar at the nozzle itself (meaning still higher pressures earlier in the system), and more sophisticated injection patterns are also important. Pilot injection of a small amount of fuel can reduce NOx content, and post. injectionof fuel can get rid of unbumt fuel that would otherwise form particulate matter. Four-valve cylinder heads and better combustion chamber design have done their bit for reduced emissions, as has better block design for reduced oil consumption.
Iveco is also looking at turbocompounding, a technology previously explored by Scania. Moore believes that this technique has great potential, but mostly for larger, long-distance vehicles.
Prominent
In addition, manufacturers have to look at specific pollutants: the most prominent at the moment are nitrogen oxides (NO, NO2 and NO3, known collectively as NOx) and particulate matter (PM).
The perennial problem is that as NOx levels go down, fuel consumption almost inevitably goes up. This has been masked in the past few years by ever more advanced electronic diesel control, which is far more effective than mechanical systems at light loads. Exhaust gas recirculation has reduced NOx levels significantly, but might not reach the levels needed at Euro-4.
"De-NOx" catalysts using liquid urea as a reagent (including the SiN0x system already demonstrated by MAN, and a similar system being tested by Iveco) would be a fairly practical solution, but there are two problems to be overcome.
Infrastructure
The first of these concerns infrastructure, or lack of it: how long would it take for a workable network of urea filling stations to be set up around Europe?
The other is purely technical: nobody has yet developed a realtime sensor for NOx in an automotive application, so it is not possible to adjust the system's settings while the vehicle is operating. Instead, the system has a "baked-in" map of settings for each operating parameter (revs, load, throttle position, temperature and so on) which correspond to "doses" of urea.
But the manufacturers dare not allow the system to "overdose" on urea, as this could result in ammonia coming from the exhaust—and ammonia is a far worse pollutant than NOx. The conservative settings required to avoid this make the system less than ro o% efficient.
The problem with particulates is that they are linked to NOx formation. As you advance injection timing particulates are reduced, but NOx goes up: retard the timing and particulates go up as NOx goes down. These particulates are a bigger problem in smaller engines, where fuel is more likely to hit the cylinder wall
and remain unburnt.
CRTs
An increasingly common approach is the use of oxidation catalysts and continuously regenerating traps (CRTs). These are expensive and have a detrimental effect on fuel economy, but seem to work reliably.
However, both are critically dependent on the quality of the fuel, requiring fewer than roppm (parts per million) sulphur by weight. The present legal requirement in the UK is for less than 5oppm, but Continental suppliers are offering fuel at up to 25oppm.
Lower-sulphur fuels are already available—they are readily available Scandinavia, for example— either through more intensive refining or through chemical synthesis (see CM -ix October for a description of diesel fuel duced from natural gas).
However, a CRT's soot filter will eventh get blocked up by non-carbonaceous ma even minute metal particles in the engine When this happens, back pressure incre; and performance is affected.
At the moment the particulate test loot particles known as PM ro because they ar microns (o.ormm) in diameter. The e smaller PM2.5 particles (2.5 microns 0.0025mm) that are thought to have he implications are not tested, though these I be produced in larger numbers by petrol gas-engine vehicles. Then there is the pc bility of "nanoparticles"—even smaller bi matter created by sulphur reactions. So experts have a way to go before Euro-4 Euro-5 are licked. Manufacturers and op tors both have good reason to hope the e] sions goalposts don't move too fast.
III by Toby Clark